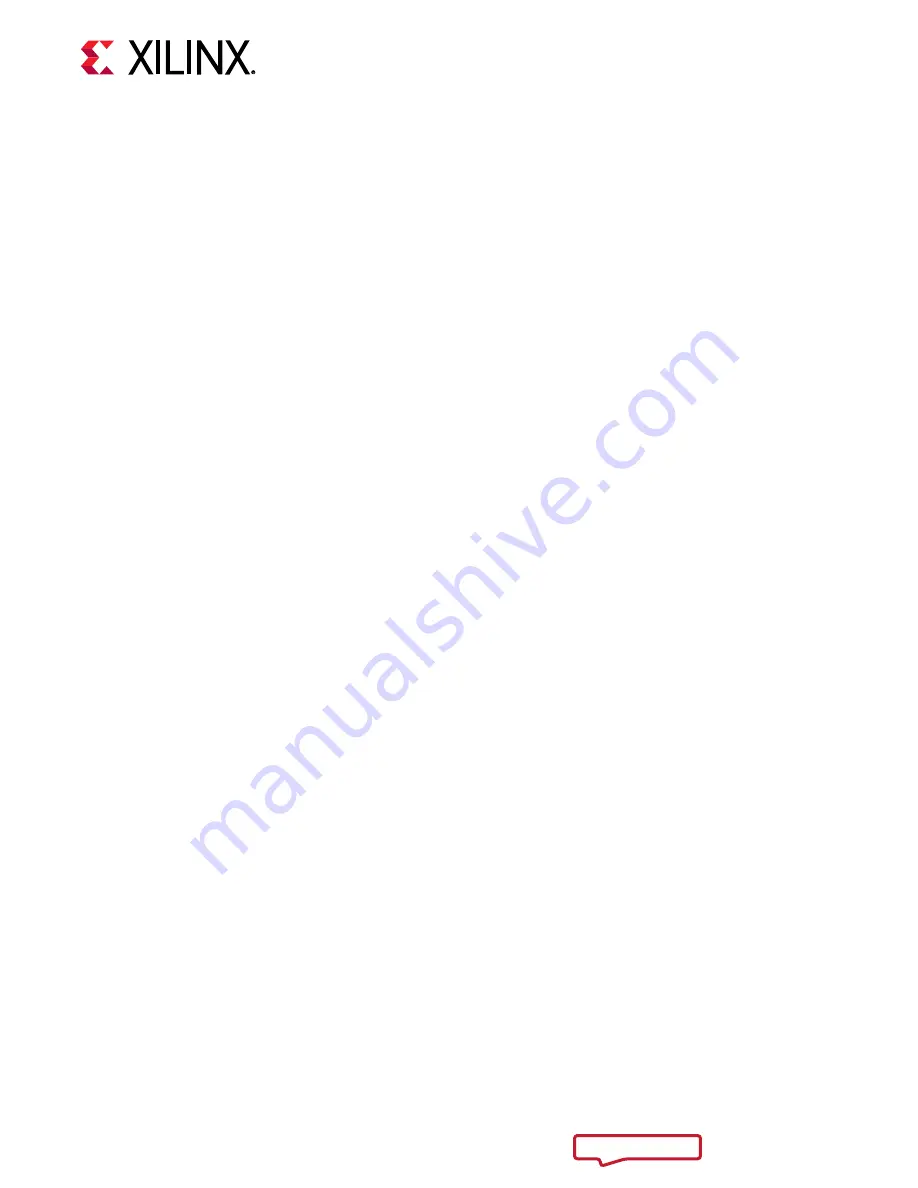
AUTOMOTIVE APPLICATIONS DISCLAIMER
AUTOMOTIVE PRODUCTS (IDENTIFIED AS "XA" IN THE PART NUMBER) ARE NOT
WARRANTED FOR USE IN THE DEPLOYMENT OF AIRBAGS OR FOR USE IN APPLICATIONS
THAT AFFECT CONTROL OF A VEHICLE ("SAFETY APPLICATION") UNLESS THERE IS A
SAFETY CONCEPT OR REDUNDANCY FEATURE CONSISTENT WITH THE ISO 26262
AUTOMOTIVE SAFETY STANDARD ("SAFETY DESIGN"). CUSTOMER SHALL, PRIOR TO USING
OR DISTRIBUTING ANY SYSTEMS THAT INCORPORATE PRODUCTS, THOROUGHLY TEST
SUCH SYSTEMS FOR SAFETY PURPOSES. USE OF PRODUCTS IN A SAFETY APPLICATION
WITHOUT A SAFETY DESIGN IS FULLY AT THE RISK OF CUSTOMER, SUBJECT ONLY TO
APPLICABLE LAWS AND REGULATIONS GOVERNING LIMITATIONS ON PRODUCT
LIABILITY.
Copyright
© Copyright 2021 Xilinx, Inc. Xilinx, the Xilinx logo, Alveo, Artix, Kintex, Spartan, Versal, Virtex,
Vivado, Zynq, and other designated brands included herein are trademarks of Xilinx in the United
States and other countries. AMBA, AMBA Designer, Arm, ARM1176JZ-S, CoreSight, Cortex,
PrimeCell, Mali, and MPCore are trademarks of Arm Limited in the EU and other countries. PCI,
PCIe, and PCI Express are trademarks of PCI-SIG and used under license. The DisplayPort Icon is
a trademark of the Video Electronics Standards Association, registered in the U.S. and other
countries. All other trademarks are the property of their respective owners.
Appendix A: Additional Resources and Legal Notices
UG1091 (v1.0) April 20, 2021
Carrier Card Design for Kria SOM
59