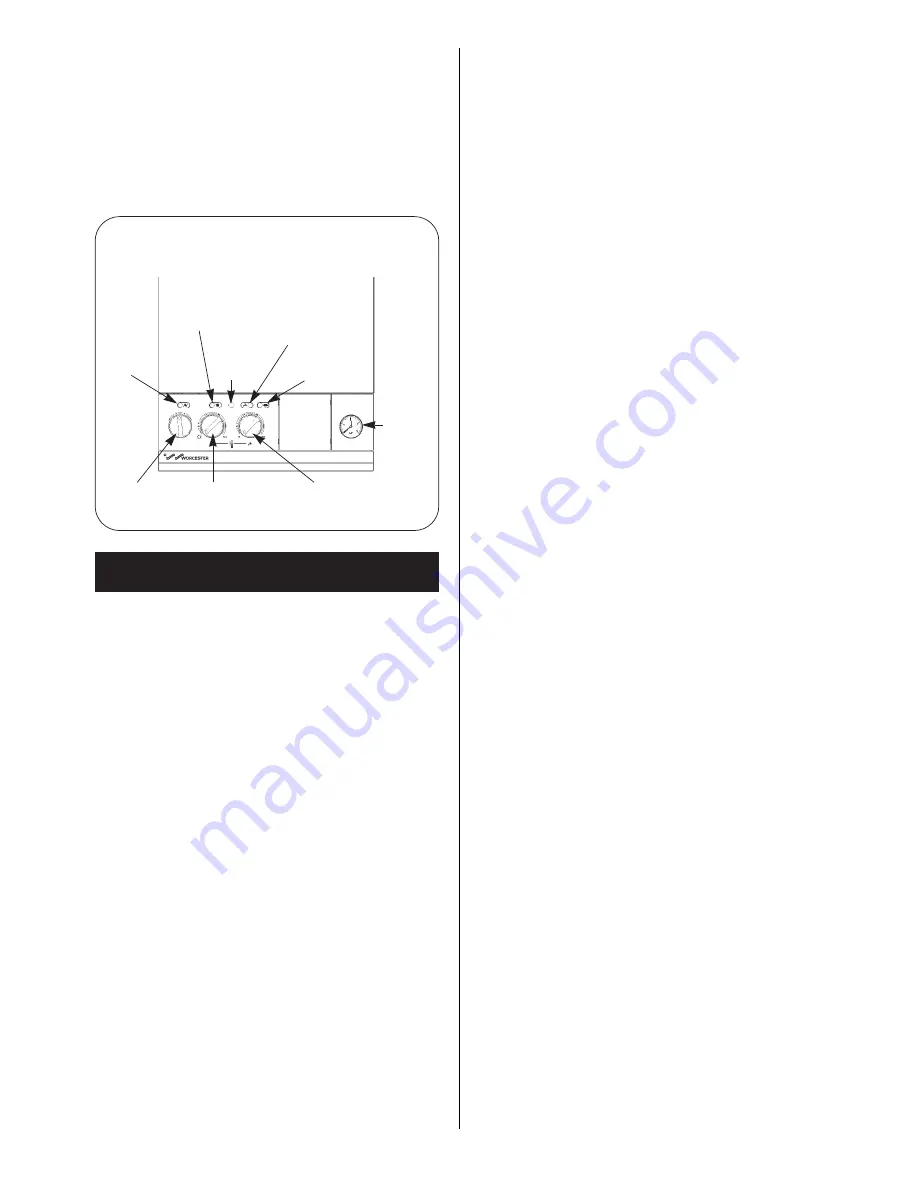
12.6
If an external programmer has been fitted which has a
programmable domestic hot water facility then it is suggested
that this be set to Continuous or the equivalent.
12.7 Tell the user, because the appliance is operating at high
efficiency, a white plume of vapour will be emitted from the flue
terminal. The plume will be more noticeable during cooler
weather.
12.8 Tell the user about the safety devices and hazard notices.
13.1 SERVICING
To ensure continued efficient operation of the appliance it
must be checked and serviced as necessary at regular
intervals. The frequency of servicing will depend upon the
particular installation conditions and usage, but once per
year should generally be adequate. The extent of the service
required by the appliance is determined by the operating
condition of the appliance when tested by fully qualified
engineers.
Any service work must be carried out by competent
engineers such as British Gas or Corgi registered personnel.
13.2 PRE-SERVICE INSPECTION
Check that the flue terminal and the terminal guard, (if fitted), are
clear.
If the appliance is in a compartment, check that the ventilation
openings in the compartment door or walls are clear. Refer to
Section 6 - Air Supply.
Check the system and remake any joints or fittings which show
signs of leakage.
Check the plastic condensate pipe for leakage and clear any
debris collecting around the discharge point.
Refill, vent and re-pressurise sealed systems as described in
Section 11, Commissioning.
Operate the appliance and the system taking note of any faults.
Measurement of the flue gases
For consistency of results of the flue gas measurements it is
necessary to have a constant output and stationary equilibrium.
Switch on the appliance.
Switch to DHW and CH mode.
Hinge down the facia. Refer to 13.3(c).
Turn the Mode Switch to the ‘Max.’ position.
Wait until the appliance reaches stationary equilibrium
(approx. 10 minutes).
Remove the sealing screw on the flue turret. See fig. 20.
Insert the probe into the measurement gap up to a depth of
50mm.
Seal any gaps.
Expected measurements should be between:
CO:
0.001 and 0.005%.
CO
2
:
7.0 and 8.5%.
After taking the measurement:
Replace and tighten the sealing screw.
Turn the Mode Switch back to the ‘normal’ position.
Put the facia back in to the correct position.
WARNING:
Disconnect the electrical supply at the mains and turn off the
gas supply at the gas service cock on the appliance before
servicing. After completing the service always test for gas
soundness as indicated in BS 6891.
13.3 DISMANTLE THE APPLIANCE
To carry out a full and comprehensive service of the appliance
remove the following parts to gain access to the components
which need to be checked or serviced.
(a) Cabinet Front Panel
Remove by lifting off the supports.
(b) Inner Casing Cover
Check the electricity supply to the appliance is turned off.
Remove the cabinet front panel. Unscrew the four screws
securing the cover to the easing and lift off. See fig. 27.
(c) Facia Panel
Check the electricity supply to the appliance is turned off.
Remove the cabinet front panel. Unscrew the two upper screws
and hinge down the facia into the Service Position. Take care not
to damage the pressure gauge capillary tube or electrical
connections. See fig. 27.
(d) Bottom Panel
Hinge down the facia panel. Disengage the front edge of the
bottom panel from the two clips and remove from the appliance.
See fig. 27.
(e) Fan Assembly
Remove the inner easing cover. Carefully unplug the electrical
connections and pull off the sensing tubes. Unscrew the two
fixing screws locating the side of the fan assembly to the flue
hood. Unscrew one fixing screw locating the fan outlet spigot to
the secondary heat exchanger.
Ease the fan assembly clear of the inner casing. Ensure the
sealing gasket fitted between the fan outlet spigot and
secondary heat exchanger is not damaged. See fig. 32.
When refitting the fan assembly ensure the gasket seal is
replaced correctly. If there is any sign of damage it must be
replaced. Connect the red sensing tube to the lower position
marked ‘+’ positive and the clear tube to the top position
marked ‘–’ negative.
Connect the Black wire to terminal No. 1, Red wire to terminal
No. 3 and White wire to terminal No. 4.
(f) Flue Hood Assembly
Remove the fan assembly. Undo the two screws securing the flue
hood. Lift and slide the flue hood assembly forwards clear of the
appliance. See fig. 32.
When refitting the hood ensure that the rear return edge passes
under the lip at the rear of the combustion chamber. See fig. 32.
(g) Combustion Chamber Front and Sides Assembly
Remove the inner casing cover, fan and flue hood assembly.
Slacken off to the end of the thread but do not remove the two
wing nuts securing the combustion chamber.
13. Inspection and Servicing
23
Fig. 31. User controls.
C.H. demand
indicator
D.H.W. demand
indicator
Mains
indicator
Mains
switch
C.H. temp
control knob
D.H.W. temp
control knob
System
pressure
gauge
Reset
button
Flame
indicator
26CDi Xtra
Содержание 26CDi Xtra
Страница 35: ...35 96 NG OR LPG NG OR LPG 109 201 ...
Страница 47: ...47 ...