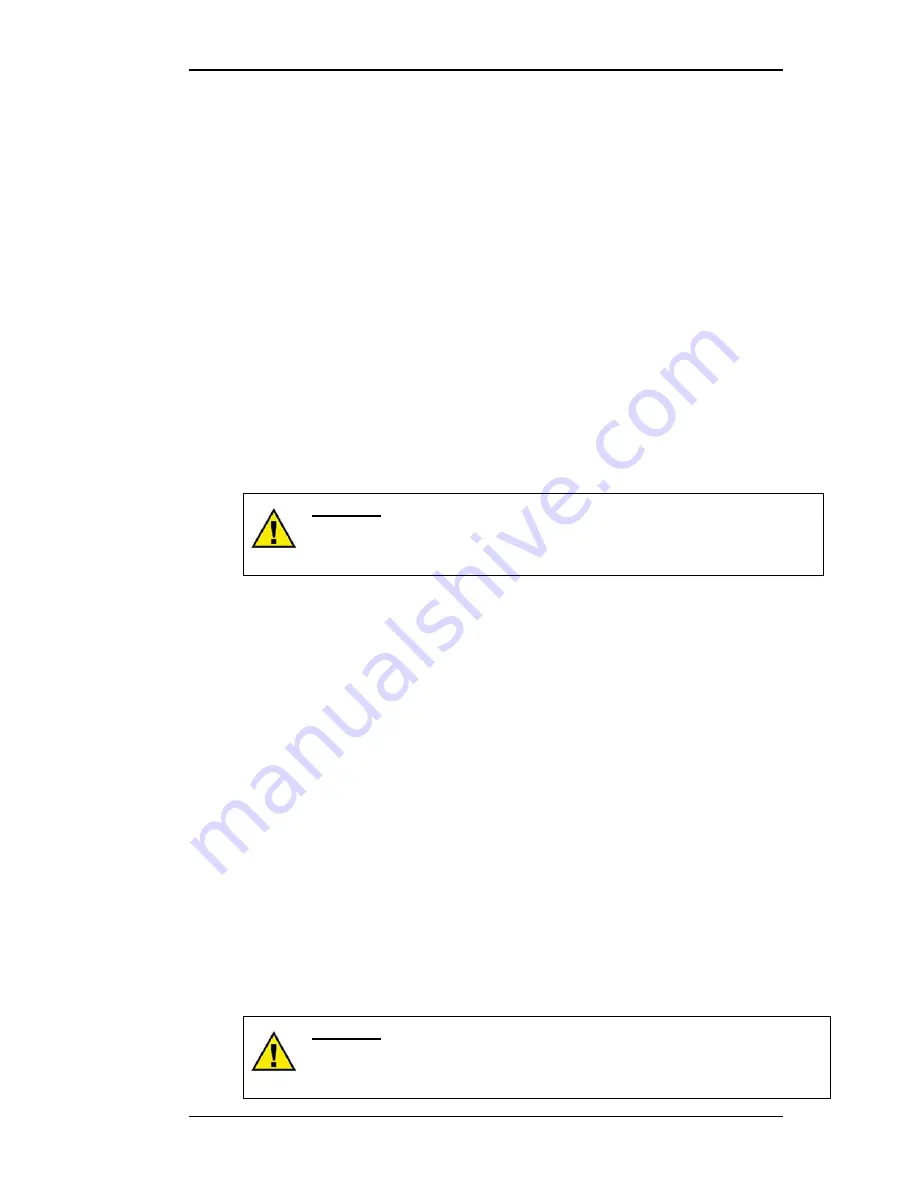
Manual 36523B
DPG-2201-00X Digital Controllers
Woodward
17
amperes of current flowing through the actuator. Fuel limiting is achieved by
setting the maximum level of electrical current allowed to flow through the actuator
during normal operation.
NOTE: If the value is set too low the engine will not be able to carry its rated load.
3.19 Integral Low Limit (optional)
The integral low limit prevents "integral windup" in the negative direction. In other
words, the integral low limit parameter is used to reduce under speed duration
after a long or sustained over speed condition was present. The low limit helps
reduce the duration and amount of engine under speed by maintaining a minimum
actuator position.
When smaller PWM duty cycle values do not reduce the engine speed any further
but an off speed (measured speed greater than the target speed) remains, letting
the Integral term grow more negative is not beneficial. Unused negative
integration would cause a slower recovery from an under speed condition.
The integral low limit specifies the PWM duty cycle where the integrator’s
influence on lowering PID output must stop. The default value is 0%. The value
can be adjusted from 0% to 90% in 1% increments.
CAUTION—Use carefully, as improper use can prevent the controller
from ever reaching the target speed. The first line of defense in
reducing overspeed or under speed errors is a well-tuned controller
via the PID terms.
3.20 Integral High Limit (optional)
The integral high limit prevents "integral windup" in the positive direction. In other
words, the integral high limit parameter is used to reduce over speed duration
after a long or sustained under speed condition was present. The high limit helps
reduce the duration and amount of engine over speed by maintaining a maximum
actuator position.
When larger PWM duty cycle values do not increase the engine speed any further
but a negative off speed (measured speed less than the target speed) remains,
letting the Integral term grow more positive is not beneficial. Unused positive
integration would cause a slower recovery from an over speed condition.
If an engine overload situation causes the engine speed to remain below the
target speed for some period of time, then the integral portion of PID output would
grow larger than otherwise needed (would windup). Therefore, when the load is
removed the engine may over speed because it takes time for the integral portion
of PID output to shrink or “unwind.” This is where reducing the Integral Limit High
value can help by preventing excessive windup in the PID output’s integration
term.
The integral high limit specifies the PWM duty cycle where the integrator’s
influence on raising PID output must stop. The default value is 99%. The value
can be adjusted from 99% down to 10% in 1% increments.
CAUTION—Use carefully, as improper use can prevent the controller
from ever reaching the target speed. The first line of defense in
reducing overspeed or under speed errors is a well-tuned controller via
the PID terms.