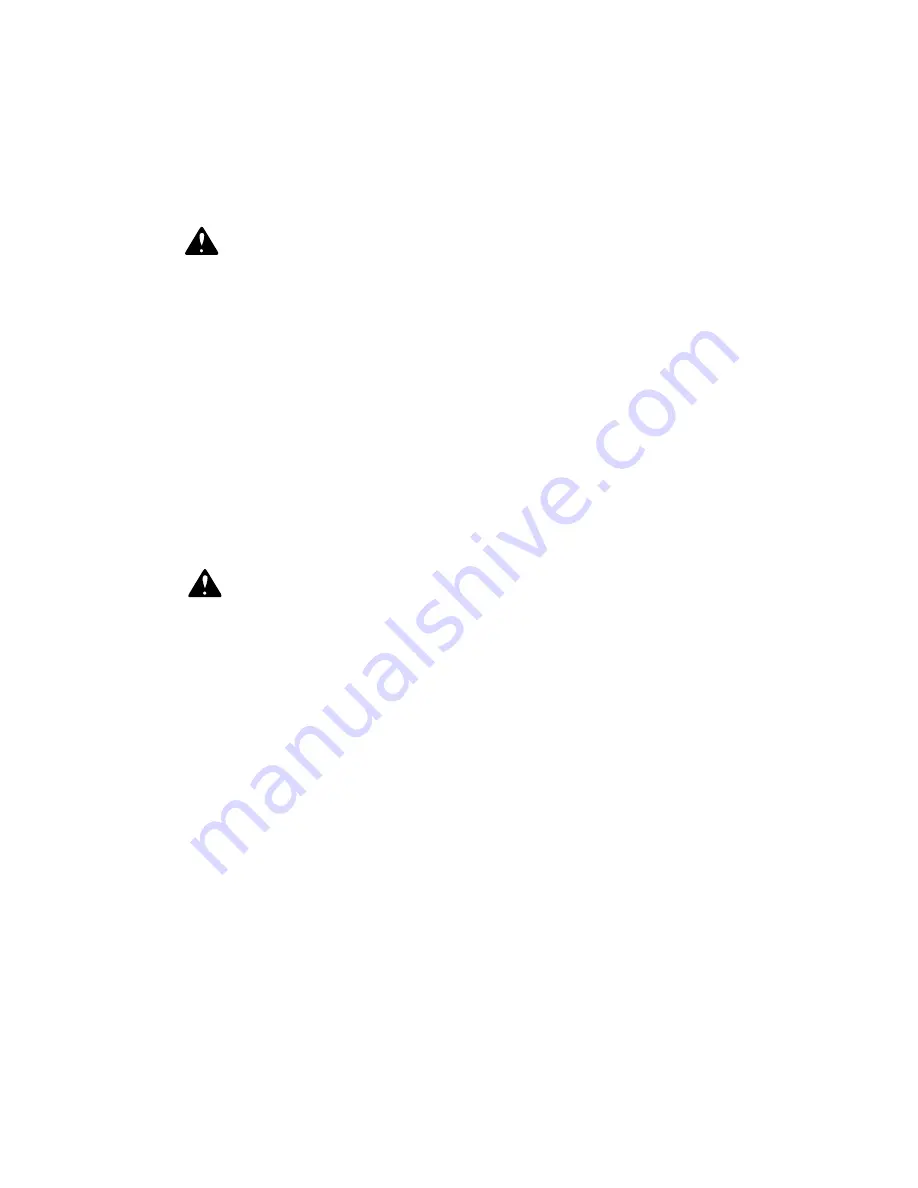
18
PN 55191 (4/22/99)
DEALER SERVICE
The information in this section is written for dealer
service personnel. The repair described herein re-
quires special skills and tools. If your shop is not
properly equipped or your mechanics are not properly
trained in this type of repair, you may be time and
money ahead to replace complete assemblies.
WARNING
J
Never go underneath equipment low-
ered to the ground or raised, unless it is
properly blocked and secured. Never place
any part of the body underneath equipment
or between moveable parts even when the
engine has been turned off. Hydraulic sys-
tem leak down, hydraulic system failures,
mechanical failures or movement of control
levers can cause equipment to drop or ro-
tate unexpectedly and cause severe injury
or death. Follow Operator’s Manual instruc-
tions for working underneath and blocking
requirements, or have work done by a quali-
fied dealer.
J
Keep all persons away from operator
control area while performing adjust-
ments, service or maintenance.
CAUTION
J
Always wear relatively tight and belted
clothing to avoid entanglement in moving
parts. Wear sturdy, rough-soled work
shoes and protective equipment for eyes,
hair, hands, hearing and head.
BLOCKING METHOD
Refer to instructions on page 14.
SPINDLE REPAIR
Blade Spindle Removal
(Figure 11)
Remove belt shield.
Remove blade from spindle. (See Blade Removal on
page 16 in Owner Service section.)
Remove belt from pulleys.
Remove cap screw and flat washer from top of
spindle shaft.
Disassemble split taper bushing (located on top of
pulley) by removing the two cap screws and inserting
them into the threaded holes in bushing flange.
Tighten cap screws alternately to remove split taper
bushing.
Remove pulley.
Remove grease fitting extension.
Remove the cap screws attaching spindle to mower
frame and remove spindle.
Spindle Repair Tips
As a reference point, the top of spindle housing is the
short portion.
To minimize wear, bearing cups, cones and sleeves
are press fit to shaft and will require a press or similar
device for removal.
When disassembling, support housing casting to
prevent damage.
Remove bearing cups by placing a punch in housing
slots and drive cup out. Alternate punch positions
from side to side. Use care to prevent housing
damage.
Bore-tite
sealant is used on the outer diameter of the
seals. Substitute seals may not meet original equip-
ment specifications and could cause leakage.
Blade Spindle Disassembly
(Figure 11)
Support spindle in a press and push shaft (7) down
through housing (5).
Remove seals from housing.
Remove bearing cups from housing as described in
Spindle Repair Tips section.
Remove bearing cone (4) from shaft (7).
Blade Spindle Assembly
(Figure 11)
Bearing cups and cones are designed to work
together. It is important to position them so bearing
cone taper mates with bearing cup taper.
Lubricate new cups (6) with a light oil. Place them in
spindle housing (5) so they will mate with cones (4).
Seat cups (6) against machined shoulder of housing
with a press or by placing a large drift on the flat lip
and driving them into housing.
Place bottom bearing cone (4) onto spindle shaft (7)
with taper up. Seat on bottom shoulder of shaft with a
press.
Insert shaft and bearing cone assembly through
bottom of housing (5). Fill housing cavity with a lithium
grease of #2 consistency with a MOLY (molybdenum
disulfide) additive. Place top bearing cone (4) on shaft
(7) to mate with top bearing cup.
IMPORTANT
J
Bearing adjustment is set by pressing
sleeve against bearing cone until proper
adjustment is attained.
Install sleeve (3) on shaft and press sleeve and
bearing cone onto shaft until all bearing free play is
removed and there is a slight drag (similar to adjusting
the front wheel bearings on an automobile). Check by
spinning spindle. It should turn freely.
Be careful not to overtighten bearings. Proper bearing
adjustment is essential to good bearing life.
Bore-tite is a registered trademark of Chicago Rawhide Industries.