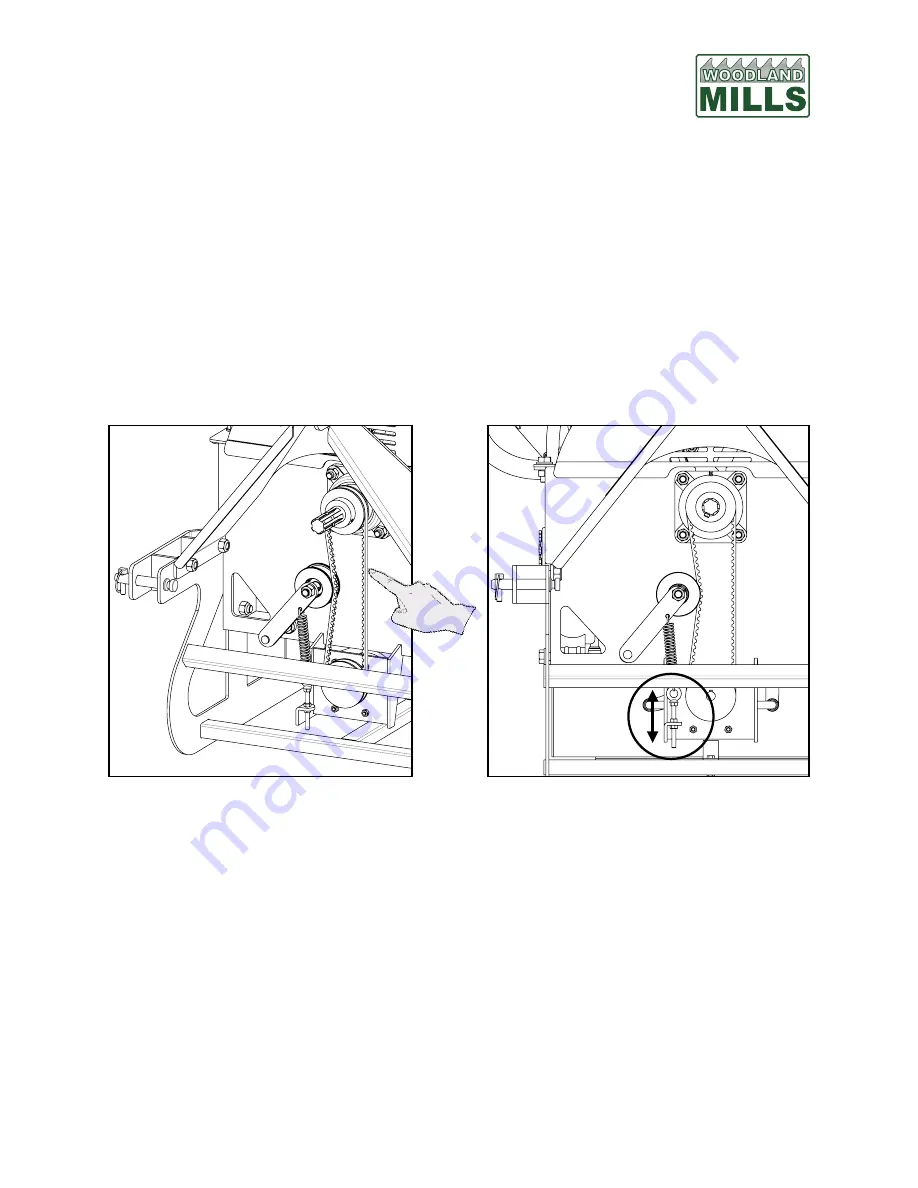
WC68 Operator’s Manual
ADJUSTING THE HYDRAULIC PUMP BELT TENSION
Check the condition and tension of the hydraulic pump belt after every 30 hours of operation.
The belt is self-tensioning via an extension spring. The amount of tension can be adjusted by
following these steps:
1. If installed, disconnect the PTO shaft from the wood chipper for safety and to allow
rotation of the belt and pulleys.
2. Check the belt tension by pressing on it with your finger (see “
Checking Belt Tension
”
below). There should not be any free slack in the belt. It should be under firm tension.
3. If the belt requires more tension, the eyebolt connected to the spring can be adjusted by
moving the M8 hex nuts (see “
Adjusting Belt Tension
” below). This will stretch the spring
and increase the belt tension until the proper tension is achieved.
WC68-MY2019: Rev A
Page
of
34
49
27-Sep-2018
Checking Belt Tension
Adjusting Belt Tension