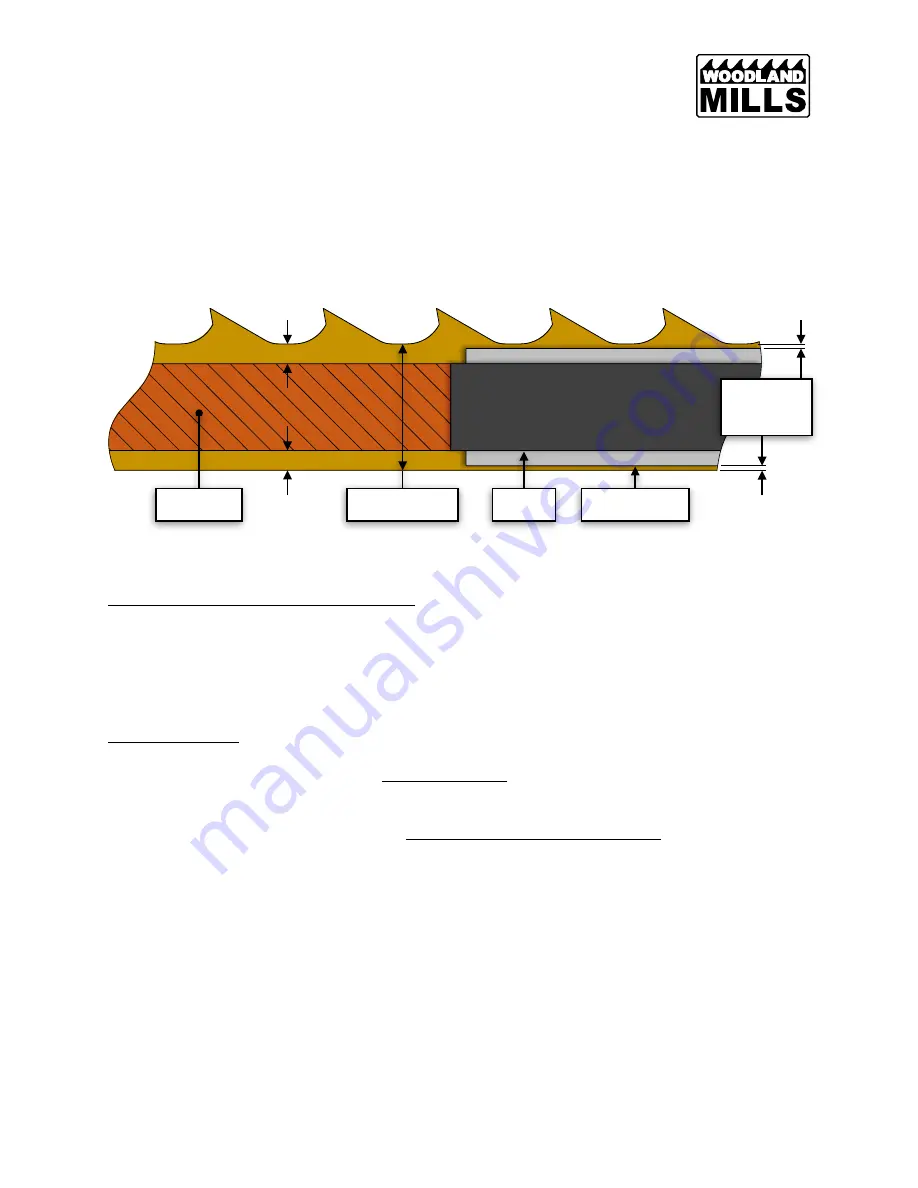
HM126 Operator’s Manual
BLADE TRACKING
Blade tracking is the fine-tuning of the band wheel angles to “hold” the blade during cutting.
This “hold” position maintains the blade’s location during most sawing conditions, with the guide
bearings and blocks acting as occasional supports. A properly tracked sawmill will hold the
band portion of the blade centred on the belts without any guides in contact with the blade.
This image shows the “ideal position” with the blade band centred on the belts & band wheels.
Precise measurements are not required to centre the blade band with the belts & band wheels.
Visually confirming the front and back of the blade overhang a similar amount is adequate.
What Happens when Tracking is “Off?”
‣
Excessive blade guide bearing wear
‣
Wavy cuts caused by uneven tension within the blade
‣
Overheating blades / blade breakage
‣
Excessive belt wear
‣
Blade will not stay on the belts
Important Points
:
‣
Tracking testing can only be made with a blade installed.
‣
Tracking
testing
is done under full blade tension. A fully tensioned blade is when tension
is set to 25 ft•lb using a torque wrench—or—when the tension handle is snugged to the
thrust bearing and then rotated a further three (3) full turns.
‣
Tracking
adjustments
are made at three (3) turns off full blade tension.
‣
The blade should run in the same location on both the follower and drive-side belts.
‣
Guide assemblies should
always
be pushed all the way back, clear of the back of the
blade. Nothing should ever be in contact with the blade when testing or making tracking
adjustments.
‣
The following test and adjustments should only be attempted with drive and follower belts
that are in good repair and keeping the blade up off the cast iron band wheels.
‣
Tuning the blade tracking is a process of testing and adjusting—re-testing and adjusting—
re-testing and adjusting. The number of cycles is determined by how far off the tracking
was at the start of the process.
‣
Please see the following pages for testing and adjustment procedures.
HM126-MY2021-EN: Rev F
Page
of
73
112
14-Jul-2021
Band Wheel
Belt
Blade Band
=
=
Belt Path
Similar
Overhang
Содержание HM126
Страница 2: ...This page intentionally left blank ...
Страница 114: ...HM126 Operator s Manual NOTES HM126 MY2021 EN Rev F Page of 112 112 14 Jul 2021 ...
Страница 115: ...This page intentionally left blank ...
Страница 116: ......