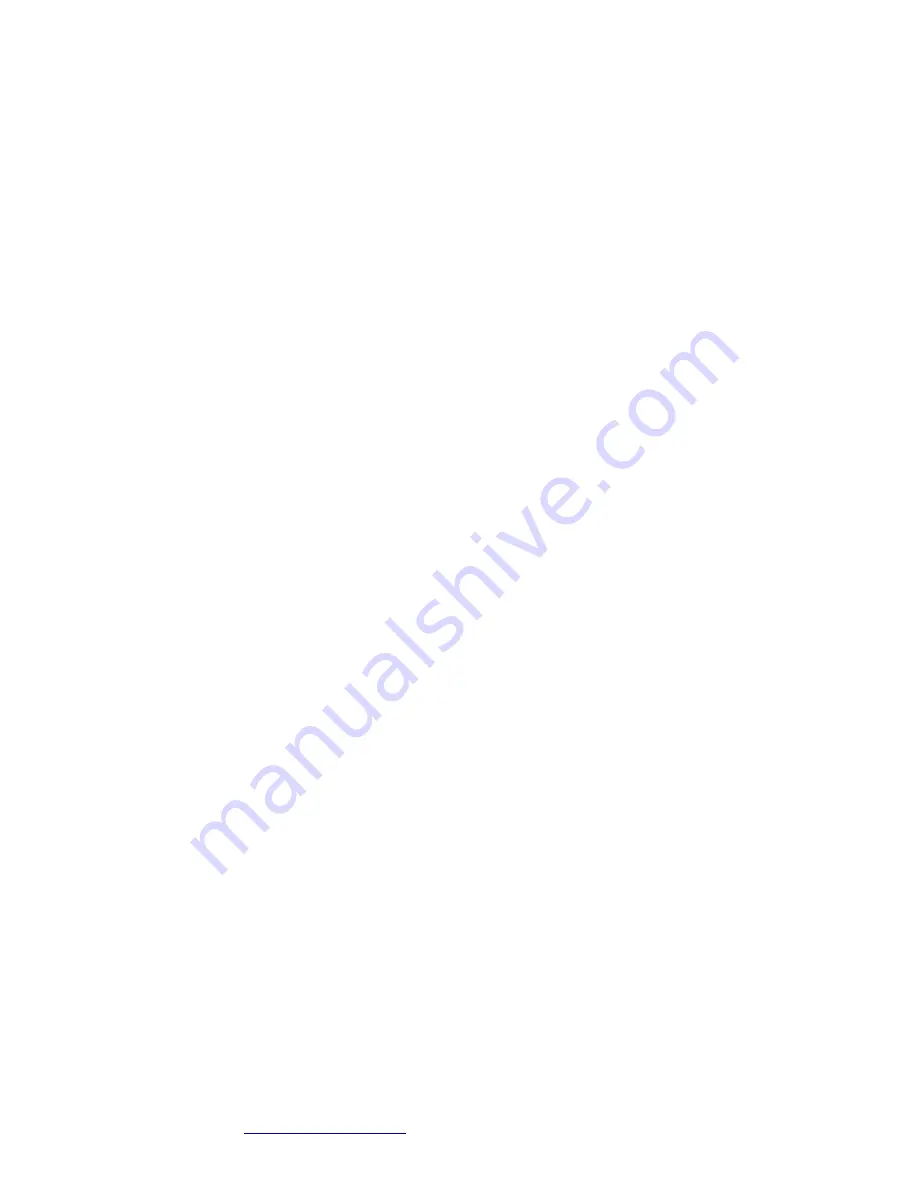
Wooden Gear Clocks UK
316 Pickering Road, Hull, East Yorkshire, UK Tel 01482 509277
http://wooden-gear-clocks.co.uk/
part 3 back up to adhere to it. Leave until remaining epoxy mix has almost dried and then carefully
withdraw from the shaft without misaligning the parts. Allow it to dry thoroughly. Remove any epoxy from
the end of the shaft which may have leaked out.
The part can now be fitted to the clock temporarily with the 2 washers (5). The part should have
approximately 1mm of end float (side to side movement) when assembled in the frame. File the end of
the shaft until the desired end float is achieved. Ensure that part 4 is fitted fully onto the shaft. The part
should spin freely.
6.
Clockerel-0008 / 60 tooth wheel assembly
Cut part 1 to length from the remaining 3mm diameter brass rod. Make this part 70mm long.
Repeat the basic assembly instructions as above for the 30 tooth wheel assembly.
7.
Clockerel-0011 / 64 tooth wheel assembly
Cut part 1 to length from the remaining 3mm diameter brass rod. Make this part 112mm long.
Repeat the instructions as above for the 30 tooth wheel assembly and the 60 tooth wheel assembly.
This assembly cannot be adjusted for end float until the final assembly.
8.
Clockerel-0006 / Ratchet wheel assembly
Cut part 1 to length from the remaining 3mm diameter brass rod. Make this part 51mm long.
Repeat the sanding instructions on the rod as above.
Place some epoxy resin inside the hole of part 2 and a small mount on the mating face. Position part 2
on the shaft as shown. Slide part 3 down the shaft and into position whilst holding part 1 so that it does
not push off. Allow the sub assembly to dry.
Lay part 4 on the assembly jig, paying attention to the orientation of the ratchet. The wheel should drive
in a clockwise direction as shown. Place a small amount of epoxy on the mating face of part 3 and a
small amount on the shaft adjacent to the mating face (no more than 6mm along the shaft). Push the
shaft through the hole in part 4 and through the hole in the jig until fully home. Leave to dry.
Remove from the jig as previously described and place a small amount of epoxy onto the mating face of
part 4. Push part 3 into position until full home.
The part can now be fitted to the clock temporarily with the 2 washers (5) and part 6. The part should
have approximately 1mm of end float (side to side movement) when assembled. File the end of the shaft
until the desired end float is achieved. Ensure that part 6 is fitted fully onto the shaft. The part should
spin freely.
9.
Clockerel-0005 / Pendulum pawl assembly
Cut part 1 to length from the remaining 3mm diameter brass rod. Make this part 56mm long.
Repeat the sanding instructions on the rod as above.
Place some epoxy resin inside the hole of part 2. Position part 2 on the shaft as shown and allow it to
dry. Clean away any epoxy that has oozed from the hole with a sharp knife before it has full dried.
Lay part 3 on the assembly jig, paying attention to the orientation. Place a small amount of epoxy on the
mating face of part 2 and a small amount on the shaft adjacent to the mating face (no more than 6mm
along the shaft). Push the shaft through the hole in part 3 and through the hole in the jig until fully home.
Leave the sub assembly to dry.
Lay part 5 onto a flat surface viewed as shown in the bottom left view. Place a very small amount of
epoxy on the inside of the leading edge of the bearing hole. Push the bearing 8 squarely into place using
the flat side of a 25mm wide steel rule or similar until flush with the front surface of the part.
Remove the sub assembly from the jig. Cut part 10 to length. Make this part 16mm long. Place a small
amount of epoxy inside the hole in part 3 and insert the pin 10 from the back to ensure no epoxy gets
onto the shaft. Leave the part to dry.
Place a washer over the pin 10 followed by part 4 as shown. Secure the parts in place with part 11.
place a washer over the shaft 1 followed by part 4 as shown. A further 4 washers are placed along the
shaft followed by part 6. Part 5 should pivot freely at this point as the washers should ensure clearance
between it and the adjacent parts. If it does not pivot freely check the bearing 8 for freedom of rotation.