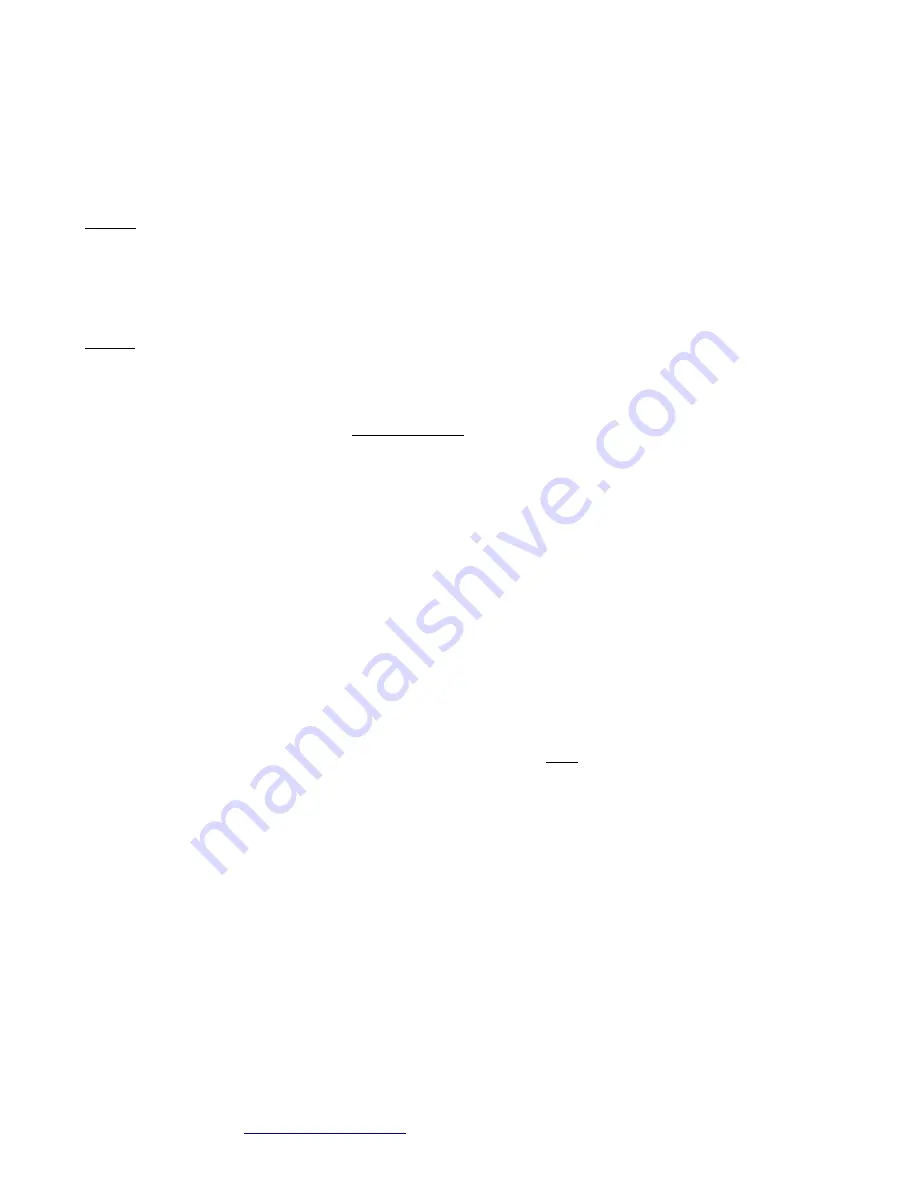
Wooden Gear Clocks UK
316 Pickering Road, Hull, East Yorkshire, UK Tel 01482 509277
http://wooden-gear-clocks.co.uk/
Aerosol can of automotive clear spray lacquer.
Jig as drawing Clockerel-0016
8mm drill bit or countersink bit
Flat 300mm steel rule
SKILLS
A knowledge of basic wood finishing techniques and the ability to read drawings. Basic soldering skills are also
required, but not essential as you could always get someone with the skills to perform these tasks. Six soldered
joints are required to complete the clock.
These instructions are to be read in conjunction with drawings Clockerel-0001 to 0017.
PARTS
Please check all parts against the parts list (BOM). If any parts are missing then please contact us immediately.
INSTRUCTIONS
1. Drawing
Clockerel-0001
Carefully remove the cutter radii from the frame hole in item 2 with a sharp chisel or square file. This is
the most difficult part of the build and will reflect in quality of the finished clock. When these corners are
square trial fit the frame into the hole. If it is too tight then carefully sand the frame where it fits into the
hole. It is easier to make this part smaller than make the hole larger. Only a small amount of sanding
should be required.
Repeat this process with the switch hole and trial fit the switch.
Apply PVA adhesive to one of the mating surfaces and press together with part 1. Place the base on a
flat surface with a heavy object to sandwich the assembly. Ensure that the two parts are correctly
aligned around the edges. Leave for 4 hours and then finish as per preparation of the MDF parts.
2. Preparation of parts
MDF parts:
It is very important that the edges of these parts are well sanded to a smooth finish. The finish of the
edges will reflect in the overall appearance of the clock. All machining marks must be removed with 80
grade abrasive paper. Only sand in the direction of the edge, NOT across it. Sanding across the edge
could break away the veneer as well as not giving a good finish. Work your way down to the 180 grade
paper and finish with a Scotchbrite pad. The edges should now be smooth with an even texture. The
veneered side can be sanded with just the 180 grade abrasive paper and Scotchbrite, working in the
direction of the grain. Only a light sanding is required.
After preparation apply shellac to all exterior surfaces and sand with a Scotchbrite when dry, paying
particular attention to the edges. Repeat this process until the edges are smooth with an even dark
texture (approximately 3 times).
Plywood parts:
The faces should be carefully sanded with 180 grade abrasive paper wrapped around a sanding block.
Lay the parts on a flat surface and carefully sand the faces in the direction of the grain. The faces can
also be sanded by gluing a sheet of 180 grade to a flat surface and rubbing the parts on this.
Wrap a small amount of 180 grade paper into the size of a flattened cigarette to do the inner edges and
teeth. Only sand the teeth to remove ragged edges. DO NOT sand too much as the profile of the teeth
may be effected. The faces of the parts may be treated with shellac as above if required.
3. Drawing Clockerel-0002
Countersink the 4 holes in the base cover (9) and screw to the base using the 4 screws (10). The holes
in the base (3) may need pilot drilling in order to insert the screws easily. Attach the 4 felt pads (11) to