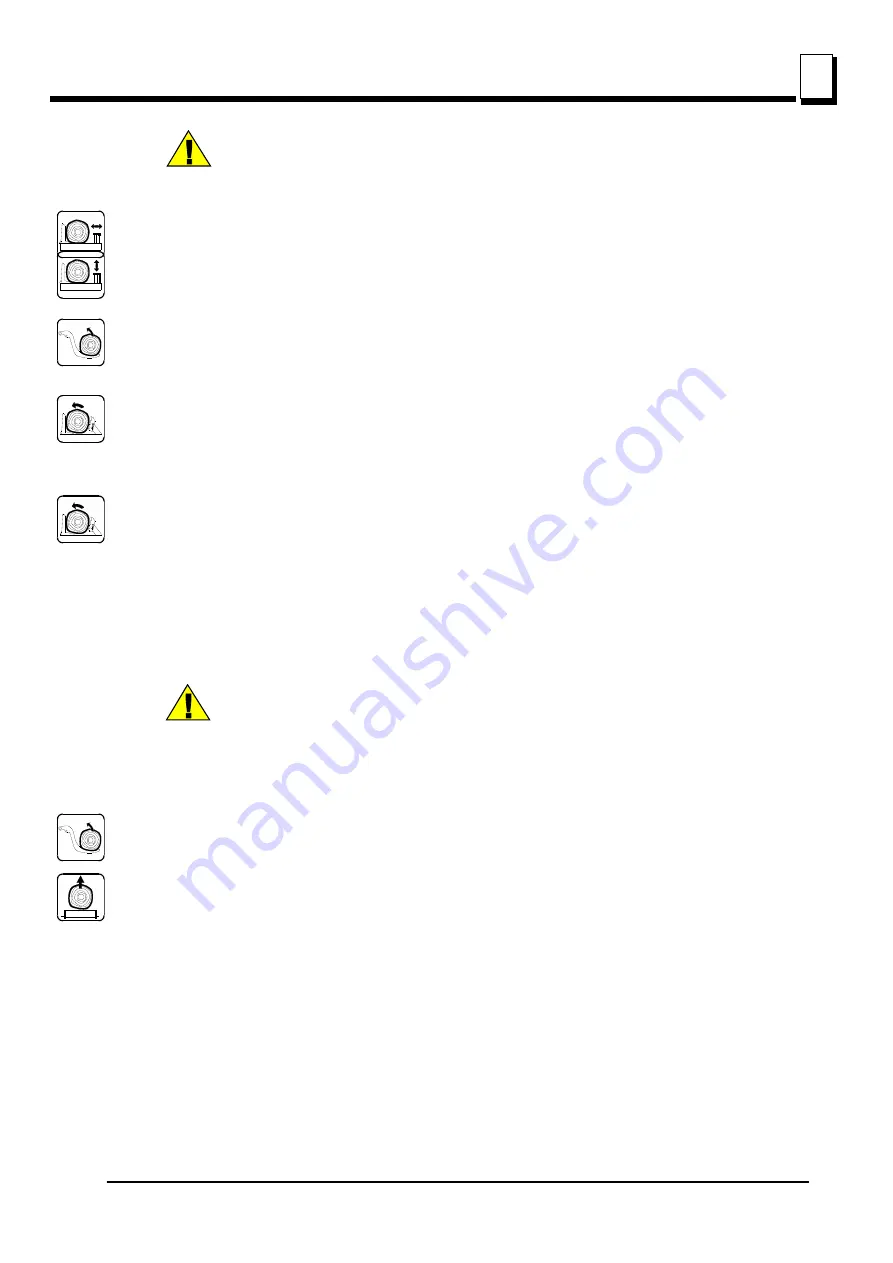
Setup & Operation
Hydraulic Control Operation
Setup & Operation
HDSdoc030722
2-30
2
CAUTION!
Always make sure the engine is running before operating
the hydraulic controls.
1.
Move the clamp out and down so it will not get in the way of logs being loaded onto the bed.
Lower the clamp in/out lever to move the clamp out toward the loading side of the sawmill.
Lower the clamp up/down lever to lower the clamp below bed level.
2.
Raise the log loader lever to extend the legs of the log loader out as far as they will go.
3.
The chain securing the log loading arm to the log turner arm will be tight. Raise the log turner lever to
raise the turner arm until there is slack in the chain.
4.
Unchain the loading arm from the turner arm.
5.
Lower the turner lever to completely lower the turner arm. Notice that after the turner arm is all the
way down, the side support braces will begin to lower. Release the turner lever after the turner arm is
lowered, but before the side supports begin to lower. This stops the log being loaded from damaging
the turner and/or falling off the side of the sawmill.
6.
When raising the turner lever, the side supports rise first. After reaching a fully vertical position, the
turner arm will engage and start to rise.
7.
Manually lower the log loader so the legs rest on the ground.
CAUTION!
Be careful when manually lowering the log loader. Do not
drop the loader onto the ground or perform any action which might
break the velocity fuse valves on the loader cylinders. These valves
control hydraulic flow and are necessary to prevent the loading arm
from collapsing during use.
8.
Lower the loader lever to lower the loading arm as far as it will go. Logs must be rolled onto the
loading arm one at a time for loading onto the bed of the mill.
9.
The front and rear toe boards should be below bed level. Once a tapered log has been loaded, the
front or rear end of the log may be lifted to parallel the heart of the log to the path of the blade.
The front toe board is raised by lifting the front toe board lever up. The rear toe board is raised by
lifting the rear toe board lever up. Once a flat has been made and the log is ready to be turned, push
the appropriate toe board lever down to lower either toe board until it falls below the level of the bed.
Содержание LT40 AH Series
Страница 1: ...Table of Contents Section Page Table of Contents SW 07doc0328171...
Страница 2: ......
Страница 6: ...6 HDSdoc030722...
Страница 37: ...Setup Operation Sawmill Setup Setup Operation HDSdoc030722 2 4 2 sm0378...
Страница 43: ...Setup Operation Sawmills with cable guide Setup Operation HDSdoc030722 2 10 2 FIG 2 8 LT40MRC K 7 B5 1 B0 18...
Страница 90: ...Maintenance Up Down System 3 3 11 HDSdoc030722 Maintenance See Figure 3 9 FIG 3 9 Up Down Chain Adjustment Nuts...