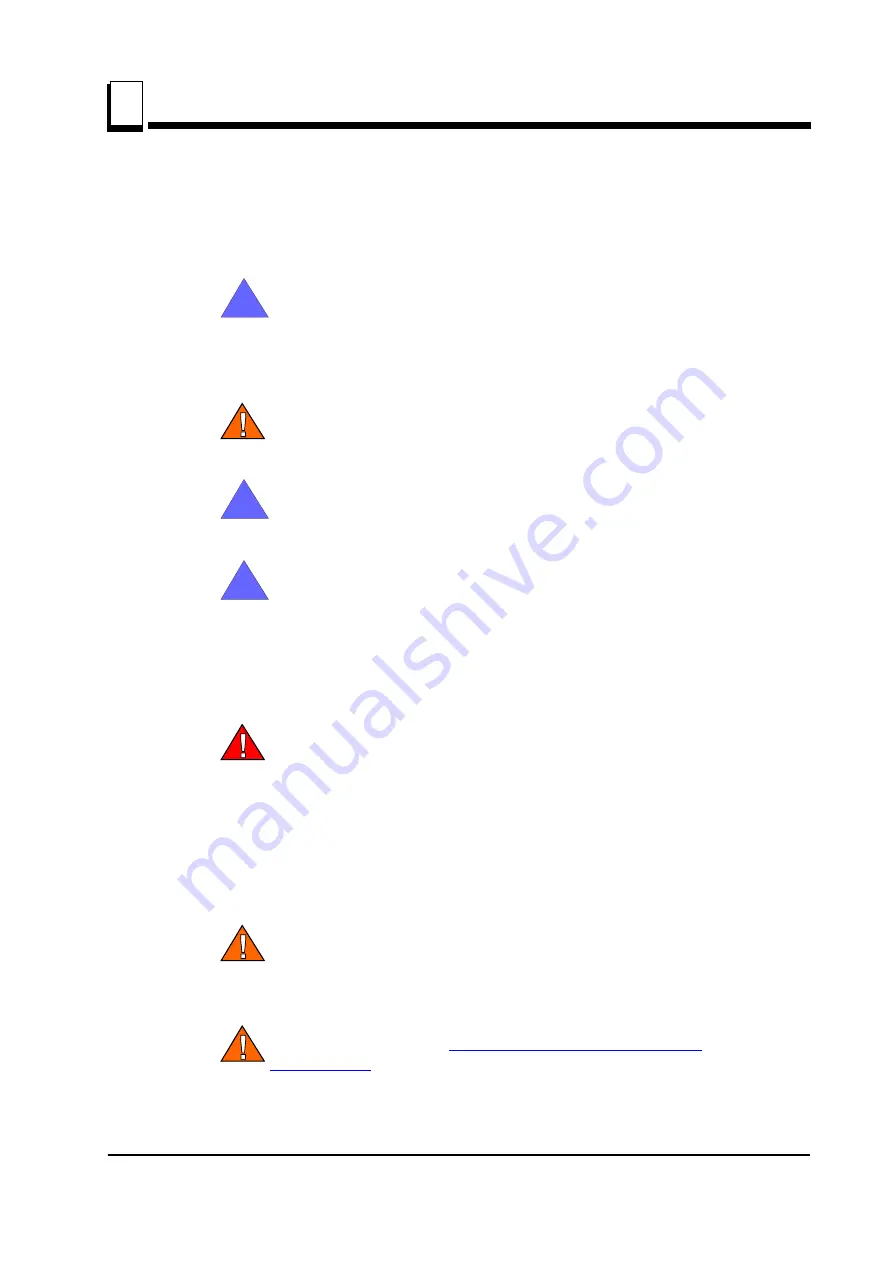
SETUP & OPERATION
Starting The Motor
2
2-8
A30Sdoc092506
SETUP & OPERATION
2.6
Starting The Motor
See the appropriate manual supplied with your specific motor configuration for starting
and operating instructions.
IMPORTANT!
For safe operation of the sawmill, one
person is sufficient, however in case of manual collection of
sawn material, at least two persons shall be assigned to
these activities in order to not exceed the manual load
lifting standard.
CAUTION!
Before starting the machine, the operator must
warn the people who are nearby about the intention of
starting the machine.
IMPORTANT NOTE!
The sawmill shall be operated only by
a person of age, who has adequate training and is in good
health condition confirmed by a medical certificate.
IMPORTANT!
When starting the machine for the first time,
check that main motor rotation direction is as indicated by
the arrow located on the motor body (fan guard). If the
rotation direction is incorrect, invert the phases in the phase
inverter located in the power socket (electric box). Setting
the phases in the phase inverter correctly will ensure
correct rotation directions of all sawmill motors.
DANGER!
Make sure all guards and covers are in place
and secured before operating or towing the sawmill. Failure
to do so may result in serious injury. Be sure the blade
housing cover is in place and secured.
DANGER!
Do not start the motor when the clutch/brake
lever is in the engaged position. Always be sure the blade is
disengaged and all persons are out of the path of the blade
before starting the motor.
WARNING!
Always wear eye, ear, respiration and foot
protection when operating the machine. Secure all loose
clothing and jewelry before operating the sawmill. Failure to
do so may result in serious injury.
CAUTION!
The sawdust extractor (according to the
specification given in
Section 1.12 Sawdust Extractor
) must be connected to the sawdust chute
and started before operating the sawmill.
!
!
!