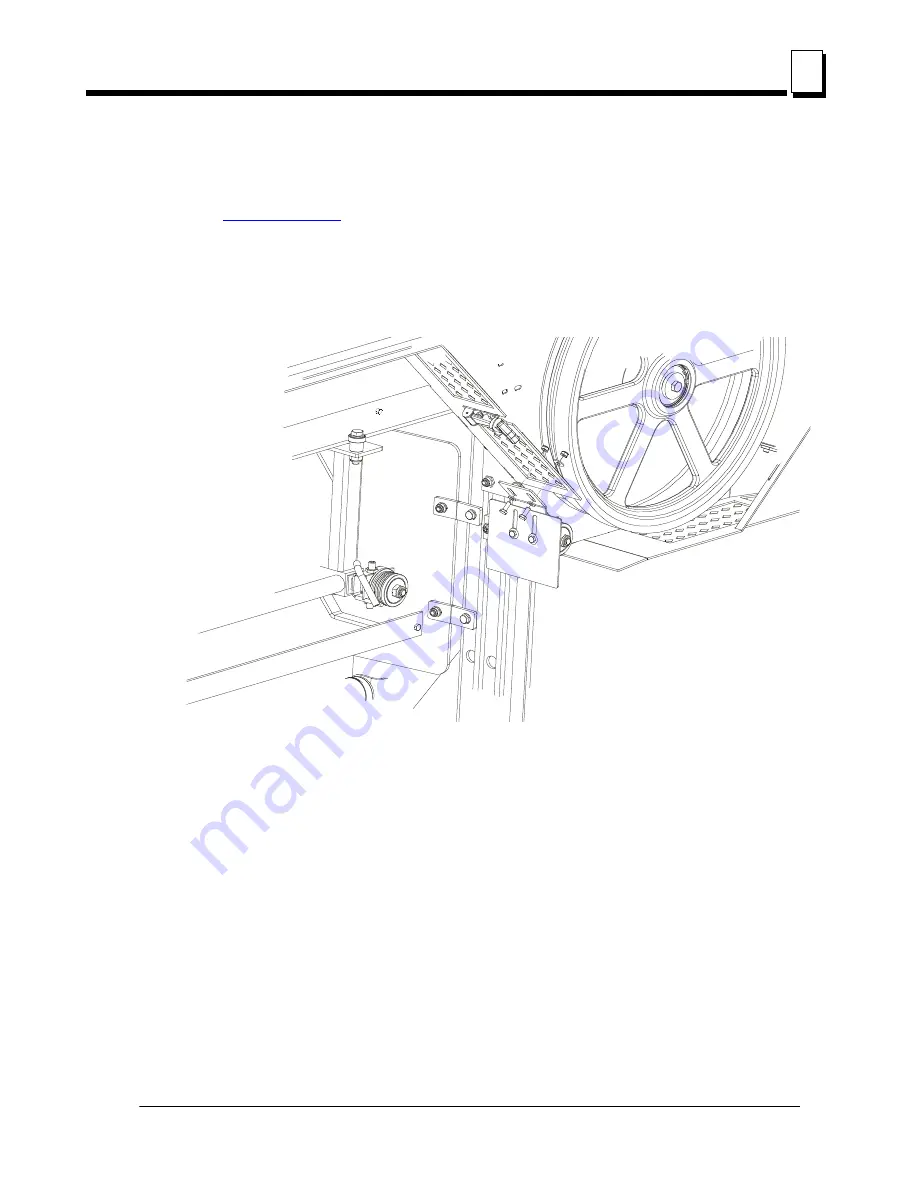
Setup & Operation
Sawmills with gas blade drive engine:
Setup & Operation
doc022219
3-9
3
guides and adjust if necessary.
14.
Install the blade height scale. To do that, first measure the distance from the bottom edge on a
down-set tooth of the blade to the top of the bed rail. Then stick the blade height scale on the
mounting bracket so that it indicates the true distance from the blade to the bed. Adjust the scale if
necessary.
See Section 6.13
.
15.
Bolt the blade guide guard so that its bottom edge is about 5 mm above the blade.
See Figure 3-7.
FIG. 3-7
Содержание LT15SA
Страница 1: ......
Страница 2: ......
Страница 88: ...1 2 30doc022219...
Страница 92: ...1 4 30doc022219...