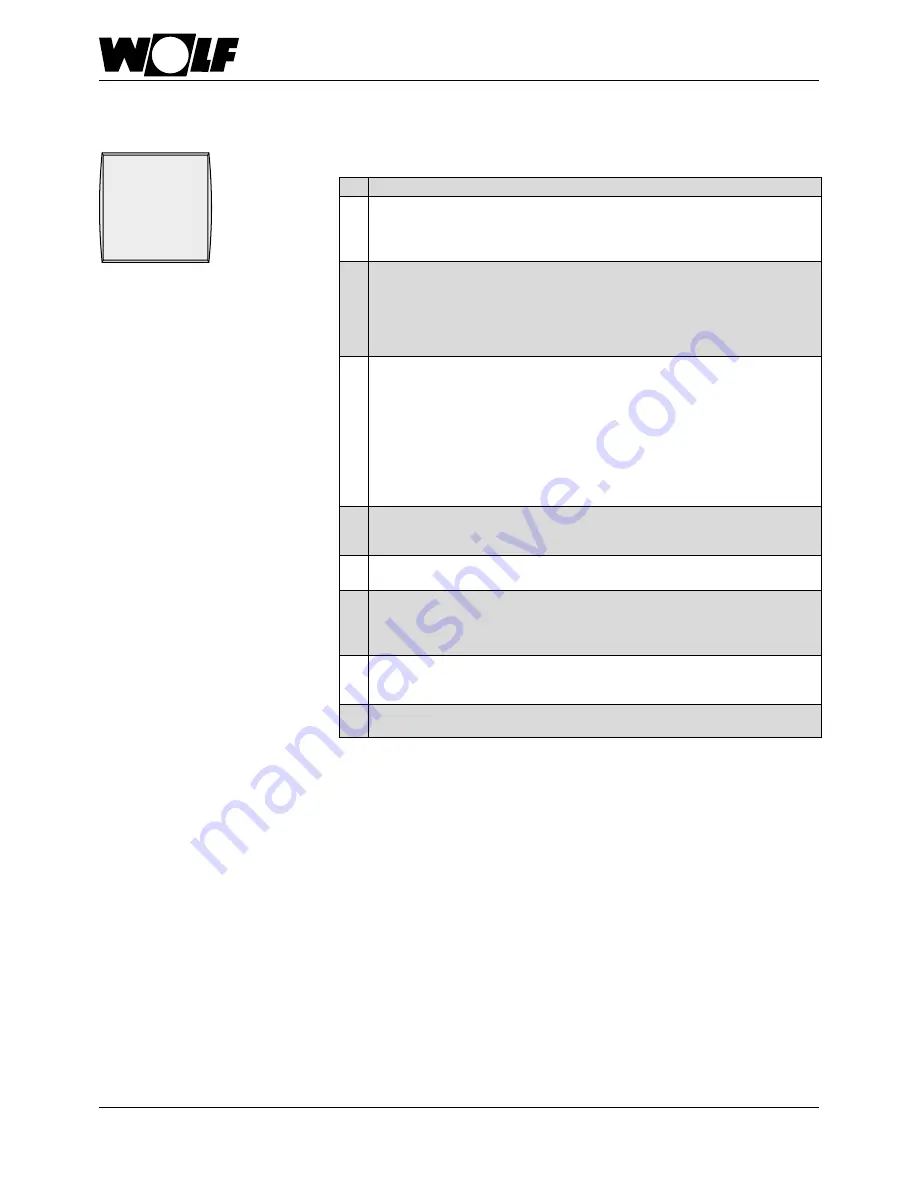
35
3062547_201802
The functions of input E1 can only be scanned and adjusted with Wolf control accessories
with eBUS capability.
The following functions can be allocated to input E1:
Programmable
Input E1
Parameters HG13
HG13
1
Factory setting: 1
Setting range: 1 to 10
Meaning
1
Room thermostat
Closed contact is a prerequisite for enabling the burner in
heating mode No function for DHW modeNo function for emissions test mode and
frost protection, no error messageOpen contact blocks the enabling of the heating and
the heating circuit pump (pump run-on)
2
Maximum thermostat/system pressure switch
Closed contact is a
prerequisite for enabling the burner in heating and DHW mode When the
contact is opened, the burner switches off and the pump run-on begins - no
error message. Applies to all pumps.
When the mains power is on and the contact is open, there is only a pump
kick, no run-on
5
Flue gas/ventilation air damper
Function monitoring of the flue gas/ventilation air
damper with floating contact, Closed contact is a prerequisite for enabling the fan
and burner in heating, DHW, cascade and emissions test mode.
Output A1
must
be programmed for flue gas/ventilation air damper function.
If output A1 is controlled and does not close input E1 within two minutes, fault
code 8 is issued.
If output A1 is not controlled, input E1 must also open within two minutes.
Otherwise FC8 is generated.
With FC8, the fan is controlled with 65% of speed stage 1.
6
DHW circulation remote control
After the DHW circulation button is activated,
output A1 is switched on for 5 minutes, if output A1 is programmed as DHW
circulation pump (A1 = 13)
7
Header sensor
A header sensor (5K-NTC) is connected at E1; observe
parameter HG 06
8
Burner block
Operation without burner Closed contact, burner blocked Heating circuit pump
and cylinder charging pump operate in standard modeIn emissions test mode
and frost protection, the burner is enabledOpen contact enables the burner again
10
External burner demand
Closed contact, TKset is set to TKmax -5 K Demand
also functions in standby; cycle block active (Control of output A1 when
parameter output A1 = 14)
0, 3, 4, 9, 11 have no function
23 Contractor level parameters
Содержание COB
Страница 78: ...78 3062547_201802 43 Notes ...
Страница 79: ...79 3062547_201802 43 Notes ...