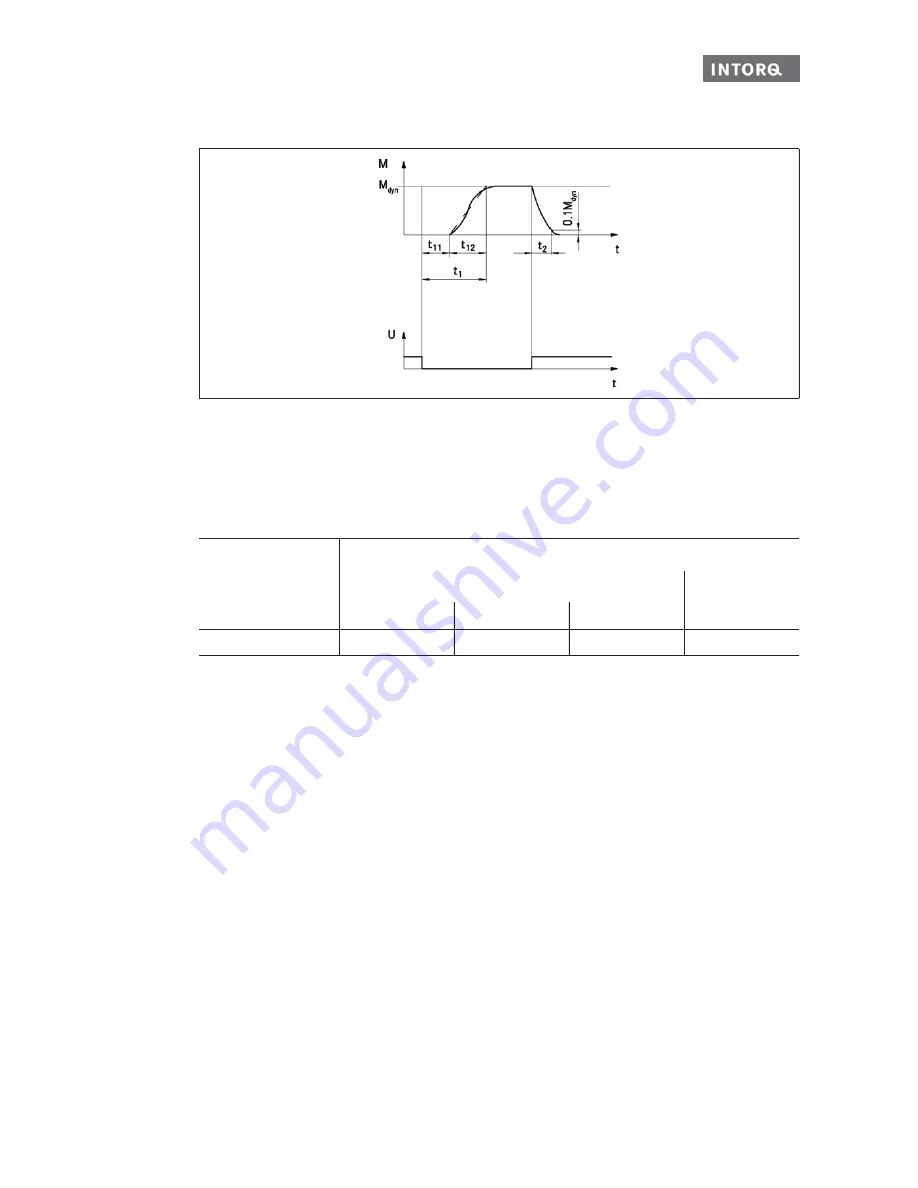
Technical specifications
INTORQ | BA 14.0201 | 04/2016
14
3.1.8
Project planning notes
❚
The brakes are dimensioned in such a way that the given rated torques are reached safely after a short
run-in process.
❚
However, as the organic friction linings used do not all have identical properties and because environ-
mental conditions can vary, deviations from the specified braking torques are possible. These must be
taken into account in the form of appropriate dimensioning tolerances. Increased breakaway torque is
common, in particular after long downtimes in humid environments where temperatures vary.
❚
Check the braking torque when the brake is being used on the customer's friction surfaces.
❚
If the brake is used as a pure holding brake without dynamic load, the friction lining must be reactivated
regularly.
3.2
Rated data
1)
Voltage for releasing/holding
2)
Coil power at 20 °C during the release/holding
Type
Friction
force
Brake disc
radius
Max.
sliding
speed
Voltage
1)
Power
2)
Coil
resistance
Max.
Current
Over-
excitation
time
F
R
[N]
R
a
[mm]
min / max
V
max.
[m/s]
U ±10%
[V] DC
P
N
[W]
R
N
±5%
[
]
I
max.
[A]
t
ue
[s]
BFK466-61
6011
300 / 600
19
90/45
522/130.5
15.52
5.8
1...2
110/55
522/130.5
23.18
4.75
205/103
550/137.5
76.41
2.68
Type
Air gap
Max.
Air gap
Fixing screws Tightening
torque
Max. perm.
Switching
energy
Transitional
switching
frequency
Weight
(without
brake disc)
s
L
[mm]
s
Lmax
[mm]
M
A
[Nm]
Q
E
[J]
S
hue
[h
-1
]
m [kg]
BFK466-61
0.4 ±0.1
0.7
2 x M16
195
250000
24
44
Technical specifications
INTORQ | BA 14.0201 | 04/2016
15
3.3
Switching times
Fig. 2
Operating/switching times of the spring-applied brakes
Disengagement time
The disengagement time is not influenced by DC or AC switching operations. The indicated disengagement
time applies to an air gap of 0.4 mm. If the air gap is larger (due to wear), the disengagement time increases.
Engagement time
For emergency braking, short engagement times for the brake are absolutely essential. The DC switching in
connection with a suitable spark suppressor must therefore be provided.
If the drive system is operated with a frequency inverter so that the brake will not be de-energized before the
motor is at standstill, AC switching is also possible (not applicable to emergency braking). In this case, the
engagement times increase approximately by a factor of 5.
t
1
Engagement time
t
11
Reaction delay of engagement
t
2
Disengagement time (up to M = 0.1 M
dyn
)
t
12
Rise time of the braking torque
M
dyn
Braking torque at a constant speed of rotation
U Voltage
Type
Switching times [ms] for s
LN
and 70 % current
Engage
Disengage
t
11
t
12
t
1
t
2
INTORQ BFK466-61
36
94
130
172
Tab. 1:
Switching energy - switching frequency - switching times
Содержание WSG-25
Страница 82: ...Notes INTORQ BA 14 0201 04 2016 36 Notes...