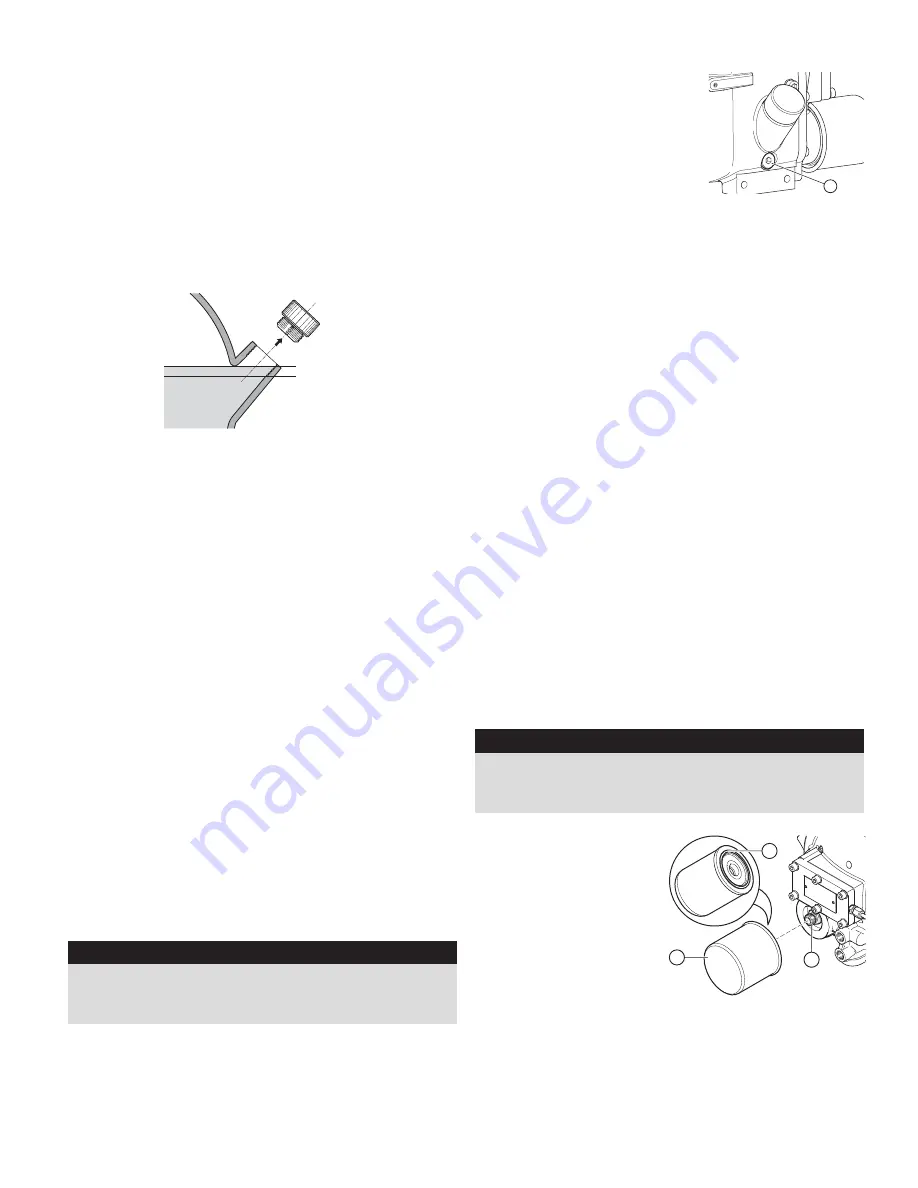
17
OPM-141/E
6. Do not conduct any welding or other heat producing
work around the oil system.
7. Ensure no tools, loose parts, or cloths are left on or on
the
system.
8. Prior to using the unit, check whether the operating
pressure, temperatures, time settings, and the oil levels
are correct. Also check that the control and switch-off
devices function properly.
CHECKING THE OIL LEVEL
Oil level can only be checked at the oil filler opening.
NOTE:
The screw cap has a safety hole on the side, oil or air
escapes if there is any residual pressure in the tank.
1. Switch off the compressor and disconnect the battery
to prevent the engine from starting.
2. Wait one minute at standstill.
3. Screw off plug of the filler neck by hand with the oil
level
depressurized.
4. Check the oil level. Reference the previous diagram.
5. If necessary, top off oil to the maximum level.
6. Screw on the plug firmly by hand.
7. Switch on the system.
8. Check the plug for any leaks, replace the o-ring if
necessary.
9. Carefully remove escaped, excess oil.
CHANGING THE OIL
Refer to the maintenance schedule chart for required oil
change intervals.
WINCO recommends our Rotorcomp maintenance kit,
which includes 1 gallon of IAT-RS8000 oil and filters.
WARNING: PERSONAL INJURY
Rotating, pressurized, and hot components. The oil
change can only be changed at a standstill and with the
compressor system completely discharged.
NOTE:
Dispose of the used oil according to applicable
regulations.
1. Switch off the compressor and disconnect the battery
to prevent the engine from starting.
7.2
[en] 02/2014
Installation and operating manual - NK 31
ROTORCOMP VERDICHTER
7.2 Oil level
An important factor for the operating safety of the
system is the oil level in the oil reservoir.
The oil level check must be carried out before
commissioning the screw compressor module
and then repeated every 100 operating hours..
The exact oil level check can only be carried out
via the oil
fi
ller opening.
Warning
Rotating, pressurized and hot components,
DANGER OF INJURY!
7.2.1 Oil level check via oil
fi
ller opening
Warning
– The unit parts, oil and oil
fi
ller plug
1
may be
over 80°C/176°F; danger of burns!
Wear personal safety equipment!
– With hot oil, the oil level can be approx. 10 mm
higher than with cold oil shortly after discharg-
ing.
As a result, oil may escape when the oil
fi
ller
plug is opened at the maximum oil level. In
this case, close the oil
fi
ller plug again imme-
diately and carefully remove the oil which has
escaped.
Figure 7-1
Note
The screw cap of the oil
fi
ller neck is provided
with a safety hole on the side from which oil or air
escapes if there is any residual pressure in the
separating tank. Wait brie
fl
y in this case.
• Switch off the system and secure it against
unauthorized switch-on.
• Wait for one minute at standstill.
• Screw off the screw plug
1
of the
fi
ller neck by
hand with the oil level depressurized.
• Check the oil level.
• If necessary, top up oil of the same oil type and
the same brand up to the maximum level.
MAX
MIN
1
7.3
[en] 02/2014
Installation and operating manual - NK 31
Note
The oil
fi
ller neck is positioned so that over
fi
lling
of the screw compressor system is not possible.
Excess oil runs out of the
fi
ller neck again.
• Screw on the screw plug
1
fi
rmly by hand.
• Switch on the system.
• Check the oil
fi
ller plug for leaks and replace
the O-ring if necessary.
• Carefully remove escaped, excess oil.
7.3 Oil change
Warning
Rotating, pressurized and hot components,
DANGER OF INJURY
The oil change may only be carried out at a
standstill and with the screw compressor system
completely discharged.
7.3.1 Oil change intervals
According to the speci
fi
cations of the system
manufacturer.
For the reference values for the screw compres-
sor compact module, see chapter
7.8
“Mainte-
nance intervals”.
7.3.2 Oil drain points
The system should be at operating temperature
in this case.
Figure 7-2
Note
Dispose of the used oil according to the appli-
cable regulations.
• Switch off the screw compressor and then
secure it against being switched on again by
removing the main switch.
• Completely release the pressure in the screw
compressor system.
• Slowly screw off the screw plug on the oil
fi
ller
neck.
• Carefully unscrew the oil drain screw
1
and
catch the used oil in a suitable container.
• Clean the oil drain screw
1
and screw in again.
1
2. Completely release the pressure
in the system.
3. Slowly screw off the screw plug
on the oil filler neck.
4. Unscrew the oil drain screw
(ref. 1) and drain the used
oil into an approved container.
5. Clean the oil drain screw and screw back in.
6. Replace the oil filter if necessary. See Changing Oil
Filter of the Air Compressor section of this manual.
7. Refill with new oil at the filler neck to the maximum
level.
NOTE:
The compressor must be operated with an oil
suitable for special requirements. This oil must be approved
by the manufacturer for screw compressors. It must even
be suitable under unfavorable operating conditions, such
as soiling of the intake air with gases, solvent vapors and
exhaust gases and at high ambient temperatures. Suitable
oil types and oil manufacturers can be specified for screw
compressor on request.
Refined oils (mineral oils) synthetic oils and bio oils
(biodegradable) can be used as screw compressor oil. The
materials and gaskets used in the screw compressor system
must be taken into account when selecting the oil type.
Corrosion and other material damage may not occur. It is
not permissible to mix different oils.
This compressor requires 101.4 ounces (3.17 quarts) of oil if
it is completely drained. Use caution when refilling.
8. Turn on the compressor and allow to run for 3 minutes.
9. Check oil level. Top off to the maximum level if needed.
CHANGING THE OIL FILTER
WARNING: PERSONAL INJURY
Rotating, pressurized, and hot components. The oil
change can only be changed at a standstill and with the
compressor system completely discharged.
1. Switch off the
compressor
and
disconnect the battery
to prevent the engine
from
starting.
2. Remove the oil filter
cartridge (Ref. 1) with
a suitable tool, i.e. oil
filter strap wrench.
3. Oil the gasket (Ref. 2.) on the new filter cartridge with
the same oil type in use with the compressor.
4.Screw the new oil filter cartridge on (Ref. 3) and tighten
by
hand.
5. Switch on the compressor.
7.4
[en] 02/2014
Installation and operating manual - NK 31
ROTORCOMP VERDICHTER
7.3.3 Filling with oil
Attention
Observe the oil recommendation, see “Lubricants
and Operating Materials”. Add oil of the same oil
type from the same manufacturer.
Switching over to another oil type can require the
compressor module to be
fl
ushed.
ROTORCOMP recommends also replacing the
oil
fi
lter during an oil change.
• Replace the oil
fi
lter if necessary
• Pour oil into the
fi
ller neck on the separator
tank up to the maximum level and screw the
screw plug
1
onto the
fi
ller neck by hand
(see Figure
7-2
).
• Switch on the screw compressor and allow it to
run for approx. three minutes.
• Oil level check:
Top up the missing oil quantity again up to the
maximum level.
• Check sheet entry (see chapter
7.7
“Mainte-
nance check sheet”).
7.4 Oil
fi
lter
Warning
Rotating, pressurized and hot components,
DANGER OF INJURY
– The unit parts, oil and oil
fi
ller plug may be
over 80°C/176°F; danger of burns!
– Wear personal safety equipment!
The oil
fi
lter replacement may only be carried
out at a standstill and with the screw compressor
system completely discharged.
7.4.1 Oil
fi
lter replacement intervals
According to the speci
fi
cations of the system
manufacturer.
For the reference values for the screw compres-
sor compact module, see chapter
7.8
“Mainte-
nance intervals”.
7.4.2 Oil
fi
lter replacement
Figure 7-3
• Switch off the system and completely release
the pressure in the system.
• Remove the oil
fi
lter cartridge
1
with a suitable
tool, e.g. oil
fi
lter strap wrench.
• Oil the gasket
2
on the new oil
fi
lter cartridge
1
with oil of the same oil type as in the compres-
sor module.
Note
Dispose of the old oil
fi
lter cartridge according to
the applicable regulations.
• Screw the new oil
fi
lter cartridge onto the con-
nection nipple
3
and tighten by hand. No tool is
required.
• Switch on the screw compressor.
• The oil
fi
lter must then be checked for leaks
with the system running.
• Oil level check:
Top up the missing oil quantity again up to the
maximum level.
• Check sheet entry (see chapter
7.7
“Mainte-
nance check sheet”).
1
2
3
Содержание DE4040F4
Страница 31: ...31 OPM 141 E ENGINE HARNESS ...