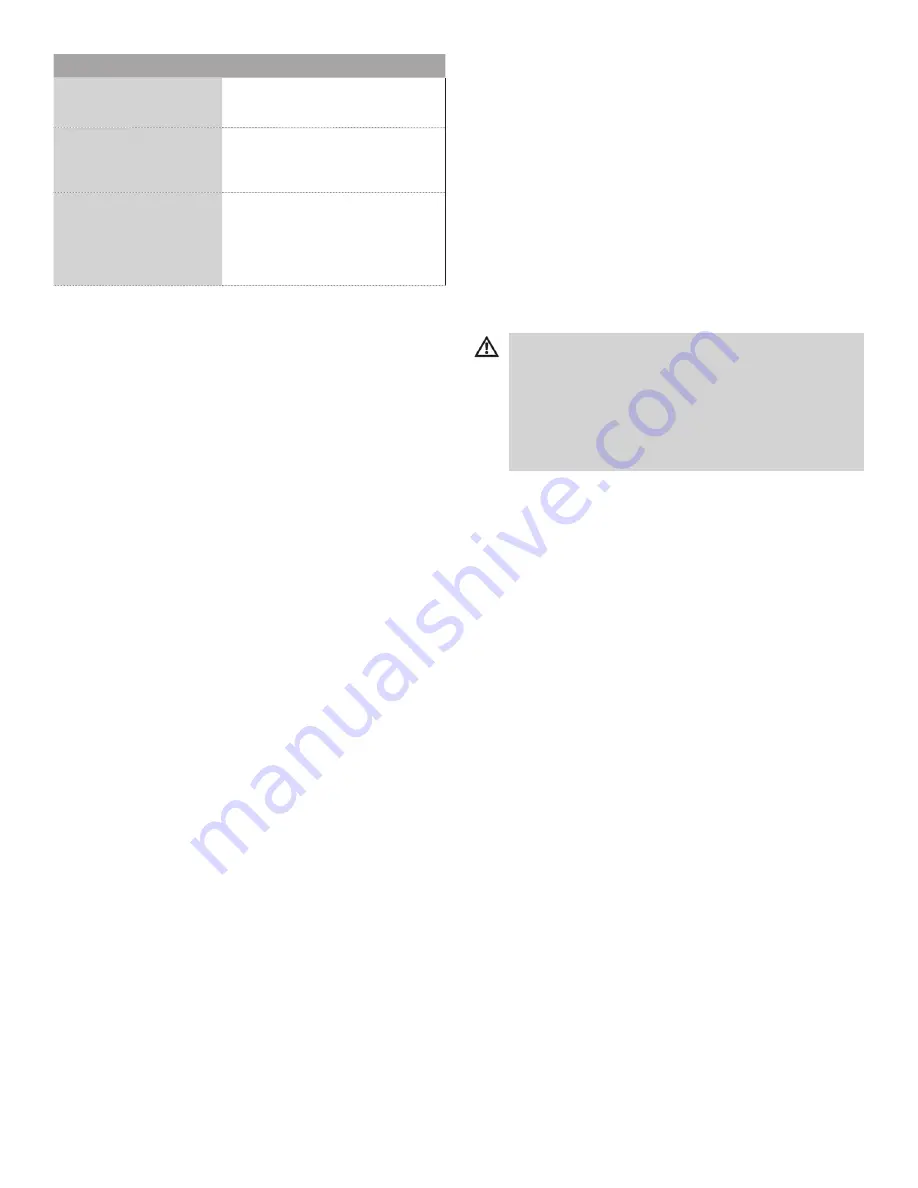
10
WILO_IOM_ICL_1219
10.3
10.3.1
1.
2.
3.
4.
5.
6.
7.
10.3.2
8.
9.
10.
10.3.3
11.
12.
13.
14.
15.
10.4
1.
2.
Disassemble Pump
Dismantle Lantern from Volute
Disconnect pump from power supply and secure
against reconnection.
Close shut-off device in front and rear of pump.
If the connection cable is too short for
disassembly, have an electrician disconnect it.
Remove all other connections (e.g. condensate
drain).
Remove bolts on lantern flange connecting the
lantern and volute.
Screw bolts into threaded extraction holes next
to drill holes on lantern flange in order to press
lantern out from pump housing.
Take out pump assembly with motor,
mechanical seal, and impeller using suitable
lifting equipment and remove from pump
housing.
Remove Impeller
Loosen impeller fastening nut counter-
clockwise.
Loosen impeller from pump shaft using an
extractor. In doing so, place extractor hook
under impeller near blade.
Remove nut, washer, and impeller from shaft.
For 6” and 8” series, also remove keys.
Remove Seal
For pumps with DI volute, loosen setscrews on
mechanical seal.
Remove mechanical seal from shaft.
Using suitable lifting equipment, secure lantern,
and then remove the screws on motor flange
Pull lantern from motor and set on flat surface
Remove O-ring from lantern.
Assemble Pump
Carefully clean seal locations. They must not be
damaged.
Check machined surfaces and clean if necessary
Check
Solution
Leakages
If the leakage rate increases (> 5 ml/h
[0.2 oz/ hr]), replace the mechanical seal
L Page 10
Motor noise and vibrations
-Check whether the pump is being
operated within the permitted
characteristic curve range (see product
catalog).
If level of noise increases due to motor
mounting or increased vibrations, replace
motor L Page 10, or replace the motor
mounting (see instructions from motor
manufacturer).
3.
4.
5.
6.
With motor on suitable lifting equipment, align
and place lantern with the motor.
Insert and tighten screws connecting lantern to
motor.
Tighten all screws on motor flange using
torquewrench. Torque L Page 11.
Press new mechanical seal onto the shaft
and into the lantern. Use a small amount of
approved polymer lubricant and press stationary
section of seal into lantern with two thumbs.
Also lubricate O-ring of rotating section of the
seal to allow for easy installation. For pumps
using CI volutes this is all that is required.
Continue to step 15. For pumps using DI
volutes, complete steps 7-14.
Caution: Damage to seal due to improper
lubrication!
Be sure not to use too much lubricant on the stationary
section of the seal as this may allow the seal to slide
back out. To ensure proper contact and extend the life
of the seal, make sure the seal faces remain clean and
free of lubricant.
7.
8.
9.
10.
11.
12.
13.
14.
15.
16.
17.
18.
19.
20.
Choose two unthreaded holes on lantern face
that are across from each other.
Rotate mechanical seal so one of the three
set screws on the seal is perpendicular to the
line that would connect the two selected
unthreaded holes.
Slide application tool with feet facing the
lantern face over the motor shaft and align
threaded holes of with unthreaded holes on
lantern face.
Make sure the flat side of the tool is
perpendicular to selected setscrew. The other
two setscrews should be visible in two notches
on opposite side of application tool.
Take two bolts meant to fasten lantern to the
volute. Insert them through back of lantern and
tighten until tool makes contact with lantern
surface. This compresses seal to working height.
Use a hex key to tighten each setscrew.
Torque L Page 11.
If tool overhangs seal, locate setscrew under the
overhang before tightening.
When setscrews are firmly tight, remove both
bolts from tool and slide off shaft.
Insert a new O-ring in lantern groove.
Place impeller onto shaft.
For 6” and 8” series, line-up impeller key slots
with shaft key slots and insert keys.
Slide on washer then screw on impeller
fastening nut.
Screw nut tightly using a torque wrench. Torque
L Page 11.
Insert current assembly carefully into pump
housing using suitable lifting equipment.
Tighten screws on lantern flange using a torque
wrench. Torque L Page 11.