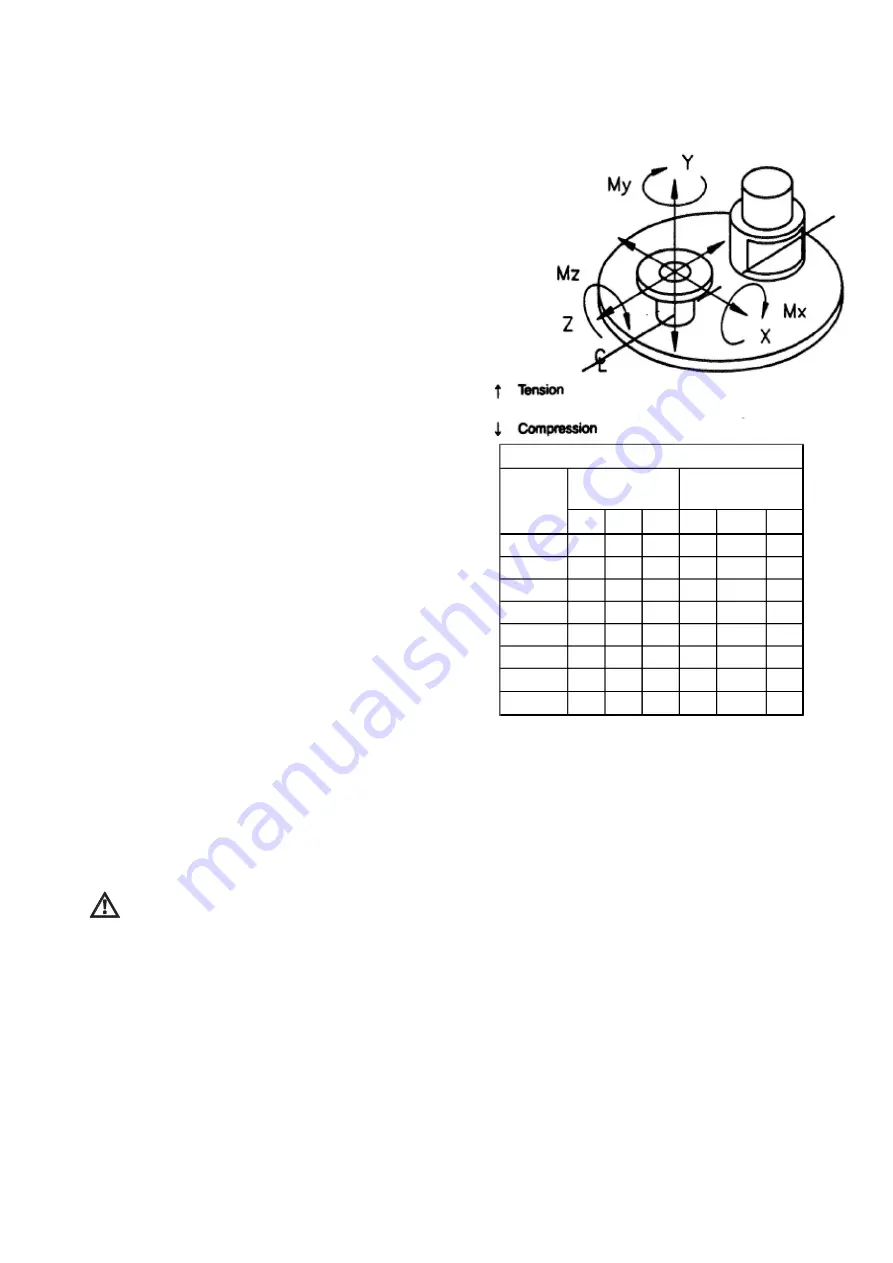
Installation and operating instructions WILO Mather and Platt
–
Sump Pumps 21
7.6 Piping
Protective covers are fitted to both the suction and discharge
flanges of the casing and must be removed prior to connecting
the pump to any pipes.
7.6.1 General piping
If the pump flange(s) have tapped holes, select flange fasteners
with thread engagement at least equal to the fastener diameter
but that do not bottom out in the tapped holes before the joint
is tight.
7.6.2 Suction piping
(Ref. fig. 10; Page No. 10)
Pumps typically only have strainers attached to the suction
flange of the pump casing. An option for an extension from the
suction flange is available and is called a Suction pipe. A suction
pipe is useful for applications where there is adequate NPSH at
the lowest sump level, but the discharge pressure is critical and
must be maintained at a maximum value compared to using a
longer column and shaft.
7.6.3 Discharge piping
Install a valve in the discharge line. This valve is required for
regulating flow and/or to isolate the pump for inspection and
maintenance. When fluid velocity in the pipe is high, for
example, 3 m/s (10 ft/sec) or higher, a rapidly closing discharge
valve can cause a damaging pressure surge. A dampening
arrangement should be provided in the piping.
All piping must be independently supported, accurately aligned
and preferably connected to the pump by a short length of
flexible piping. The pump should not have to support the
weight of the pipe. It should be possible to install discharge
bolts through mating flanges without pulling or prying either of
the flanges. All piping must be tight.
•
Use discharge piping one size larger than the pump discharge.
•
Discharge piping should be well supported and connected to
the pump such that no strain or weight of the piping is carried
by the pump.
•
Check pump shaft for freedom of rotation by hand to make
sure any discharge piping strain is not causing binding.
•
After the pump discharge, the increaser should be the first item
in the discharge line, followed by the check valve and gate
valve, respectively.
•
It is recommended that pressure indicating devices be
installed before and after the valves in the discharge line to
verify the pump is not being run dry and that the discharge
valves are not closed.
CAUTION!
The check valve is required to prevent back-flow through
the pump on shut-down. This flow can reverse rotation of
the pump, potentially damaging the pump, motor and
associated equipment.
7.6.4 Allowable nozzle loads
7.7 Final free rotation check
After connecting the piping, rotate the pump drive shaft
clockwise (viewed from motor end) by hand several
complete revolutions to be sure there is no binding and that
all parts are free. If piping caused unit to be in a bind, correct
piping to relieve strain on the pump.
7.8 Auxiliary piping
Check to see if any other connections need to be made to
pump, such as fluid injection to stuffing box for seal or
packing lubrication (when furnished) and make the required
connections.
Check to see that connections are made to the lubrication
fittings at pump manifold on mounting plate.
FX
FY
FZ
MX
MY
MZ
40
632
783
516
335
256
168
50
712
890
578
461
353
231
65
890 1134 712
692
529
441
80
1068 1334 890
949
719
475
100
1423 1779 1245 1329
1003
678
125
1957 2491 1601 1763
1356
1017
150
2491 3114 2046 2305
1763
1180
200
3781 4893 3114 3526
2576
1763
Maximum Allowable Nozzle Loads
Flange
size [mm]
Delivery Flange
Forces (N)
Moments [Nm]
Содержание 4/5 TYPE 17
Страница 24: ...Installation and operating instructions WILO Mather and Platt Sump Pumps 24 ...
Страница 39: ...Installation and operating instructions WILO Mather and Platt Sump Pumps 39 NOTES ...
Страница 40: ...Installation and operating instructions WILO Mather and Platt Sump Pumps 40 NOTES ...
Страница 41: ...Installation and operating instructions WILO Mather and Platt Sump Pumps 41 NOTES ...