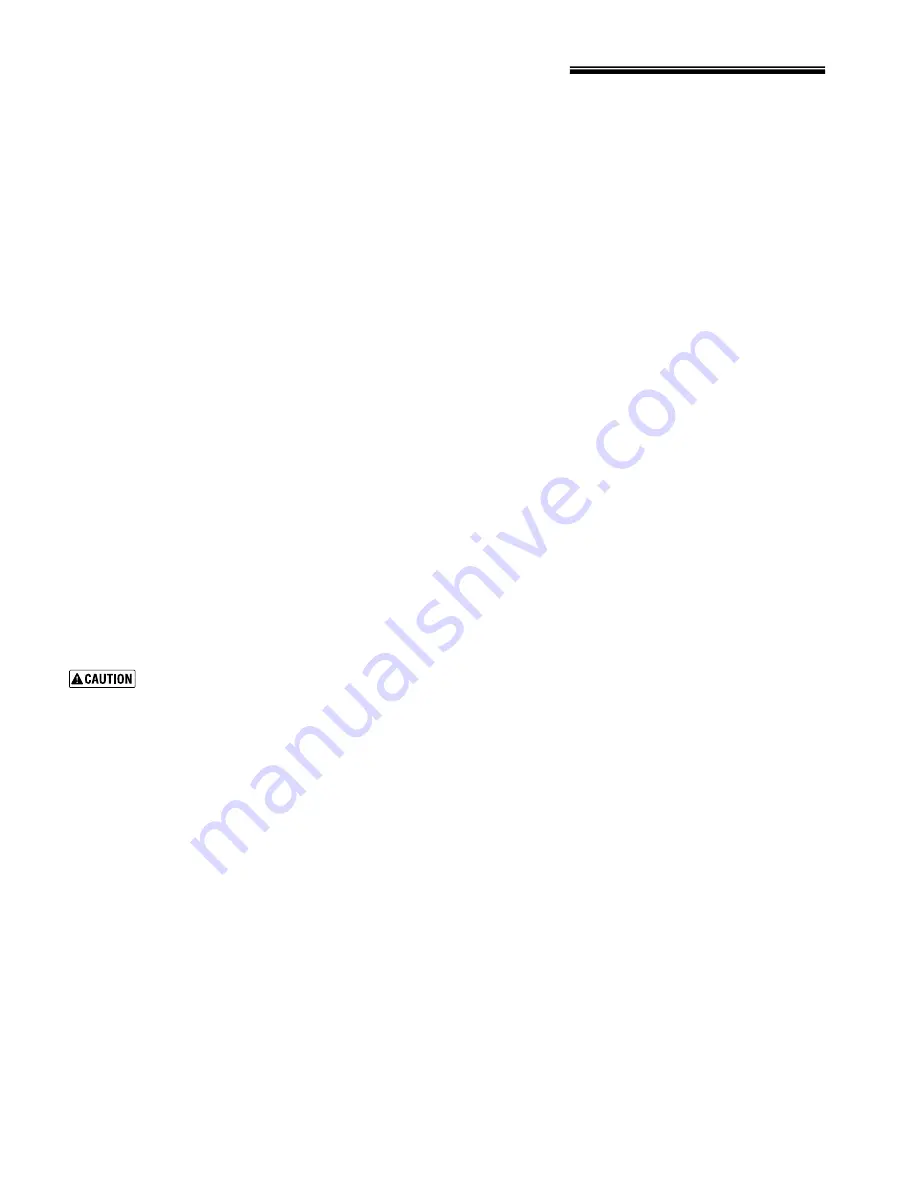
PMP-112 Multiposition
Oil Furnaces
–
Furnace Manual
14
11/13
3.1
CLEANING THE HEAT EXCHANGER
It is not generally necessary to clean the heat exchanger or flue pipe
every year, but it is advisable to have the oil burner service
technician check the unit before each heating season to determine
whether the cleaning or replacement of parts is necessary.
If a cleaning is necessary, the following steps should be performed:
1.
Turn OFF all utilities upstream from the furnace;
2.
Disconnect the flue pipe;
3.
Remove the flue collar panel located at the front of the furnace;
4.
Remove the heat exchanger baffles;
5.
Disconnect the oil line and remove the oil burner;
6. Clean the secondary tubes and the primary cylinder with a stiff
brush and a vacuum cleaner;
7. Before re-assembling the unit, the heat exchanger and
combustion chamber should be inspected to determine if
replacement is required;
8. After the cleaning replace the heat exchanger baffles, flue
collar plate and oil burner;
9.
Readjust the burner for proper operation.
3.2
CLEANING THE BLOCKED VENT SHUT-OFF
DEVICE (BVSO) (IF INSTALLED)
For continuous safe operation, the Blocked Vent Shut-off device
(BVSO) must be inspected and maintained annually by a qualified
service technician.
1.
Disconnect power to the appliance;
2. Remove the two screws holding on the BVSO assembly cover
and remove the cover;
3. Remove the two screws holding the control box to the heat
transfer tube assembly. Sliding the control box in the
appropriate direction will unlock it from the heat transfer tube
assembly;
4.
Carefully remove any build-up from the thermal switch surface;
Do not dent or scratch the surface of the thermal
switch. If the thermal switch is damaged it MUST
be replaced.
5. Clean and remove any build-up or obstruction inside the heat
transfer tube;
6. Re-mount, lock and fasten the control box with the 2 screws
removed in step 4;
7. Re-attach the assembly cover with the screws removed in step
2;
8.
Re-establish power to the unit.
3.3
CLEANING OF THE BURNER HEAD
Once annually, remove the retention head and electrodes from the
drawer assembly and remove all foreign matter, if necessary. Also
clean the extremity of the burner tube, if necessary.
3.4
CHANGING THE NOZZLE
Change the nozzle once a year with the one specified in Table 11.
3.5
CHANGING THE OIL FILTER
Tank Filter
The tank filter should be changed as required. Follow the
manufacturer’s instructions.
Secondary Filter
The 10 micron, or finer, filter cartridge should be changed annually.
Follow the manufacturer’s instructions.
3.6
CHANGING THE AIR FILTER
Dirty filters have an impact on the efficiency of the furnace and
increase fuel consumption. Air filters should be changed at least
once a year. Very dusty conditions, the presence of animal hair and
the like will require more frequent changing or cleaning.