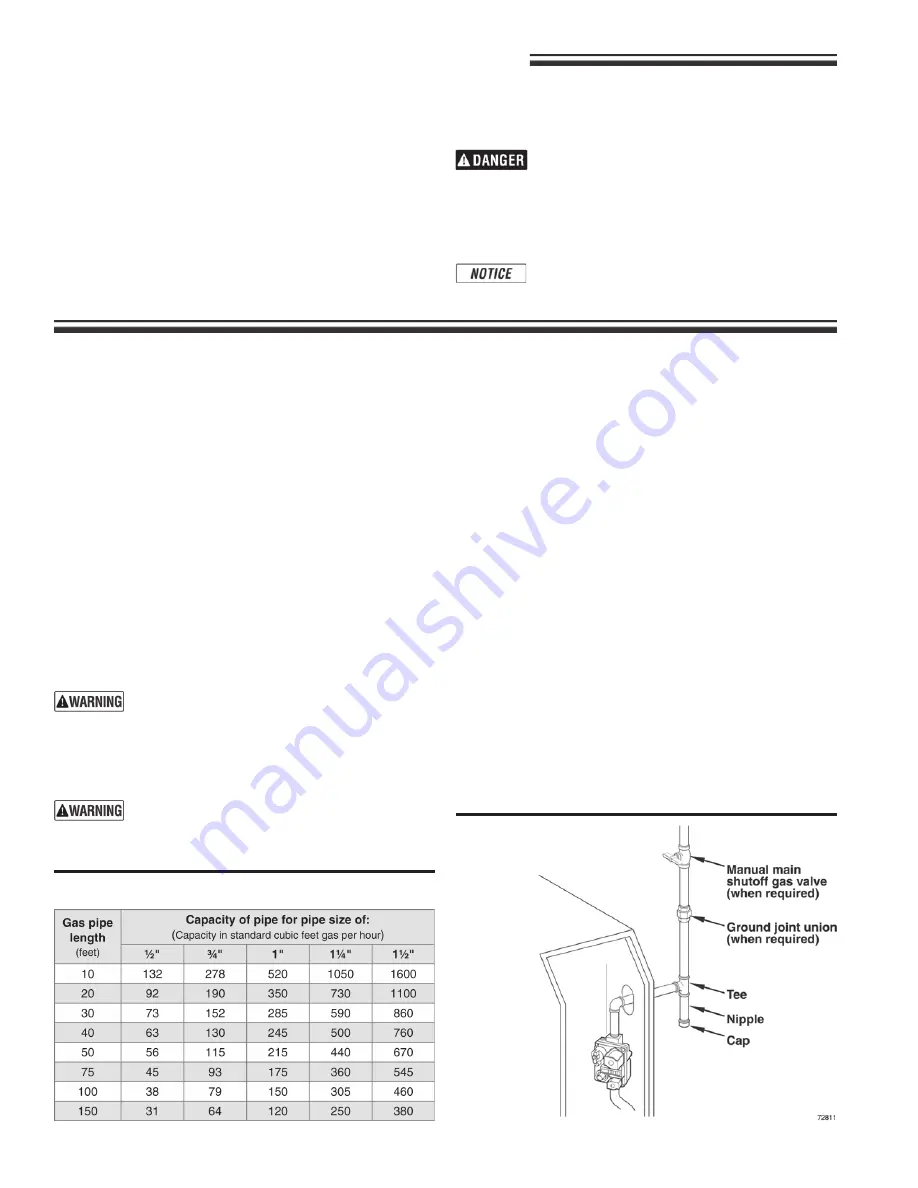
GWS-090E
Gas-Fired Water Boiler –
Boiler Manual
12
Part Number 550-110-737/1108
Figure 8
Gas supply piping
Table 6
Pipe capacity for 0.60 specific gravity natural gas
1. Remove jacket front panel and see Figure 8 to pipe gas to
boiler.
a. Install drip leg at inlet of gas connection to boiler. Where local
utility requires drip leg to be extended to the floor, use appropriate
length of nipple between cap and tee.
b. Install ground joint union for servicing, when required.
c. Install manual shutoff valve in gas supply piping outside boiler
jacket when required by local codes or utility requirements.
d. In Canada — When using manual main shutoff valve, it must be
identified by the installer.
2. Support piping with hangers, not by boiler or its accesso-
ries.
3. Purge all air from gas supply piping.
4. Before placing boiler in operation, check boiler and its gas
connection for leaks.
a. Close manual main shutoff valve during any pressure testing at
less than 13” w.c.
b. Disconnect boiler and gas valve from gas supply piping during
any pressure testing greater than 13” w.c.
Do not check for gas leaks with an open flame — Use
bubble test. Failure to use bubble test or check for
gas leaks can cause severe personal injury, death
or substantial property damage.
5. Use pipe dope compatible with propane gases. Apply sparingly
only to male threads of pipe joints so that pipe dope does not
block gas flow.
Failure to apply pipe dope as described in this
manual can result in severe personal injury, death
or substantial property damage.
Natural Gas:
1. See Table 6 for pipe length and diameter. Base on rated boiler
input (divide by 1,000 to obtain cubic feet per hour). Table 6
is only for gas with specific gravity 0.60, with a pressure drop
through the gas piping of 0.30” w.c. For additional gas pipe
sizing information, see ANSI Z223.1 (B149.1 or B149.2 for
Canadian installations).
2. Inlet pressure required at gas valve inlet:
•
Maximum: 13” w.c.
•
Minimum: 5” w.c.
•
Manifold gas pressure: 3.5” w.c. at high fire (0.90” w.c. at low fire
while in low fire at start-up)
3. Install 100% lockup gas pressure regulator in supply line if
inlet pressure exceeds 13” w.c. Adjust for 13” w.c. maximum.
Propane Gas:
1. Contact gas supplier to size pipes, tanks and 100% lockup
gas pressure regulator.
2. Adjust propane supply regulator provided by gas supplier for
13” w.c. maximum pressure.
3. Inlet pressure required at gas valve inlet:
•
Maximum: 13” w.c.
•
Minimum: 11” w.c.
•
Manifold gas pressure: 10” w.c. at high fire (3.5” w.c. at low fire
while in low fire at start-up)
4 Venting and combustion air
Install vent piping and air piping (if used) per appropriate instruc-
tions in the GWS Venting Manual, included in boiler envelope
assembly.
Refer to GWS Venting Manual and to Boiler Manual Section 1,
page 4, regarding requirements for:
• vent system
• combustion air openings
• combustion air quality
The GWS-090E boiler must be direct vented only
(combustion air ducted to boiler) and supplied with
combustion and ventilation air as described in GWS
Venting Manual, packed in envelope assembly
with boiler, and Section 1 of this manual, page 4.
Failure to do so will cause severe personal injury or
death.
Read and follow the special instructions for the Com-
monwealth of Massachusetts, located on page
40
of this manual.
5 Gas piping