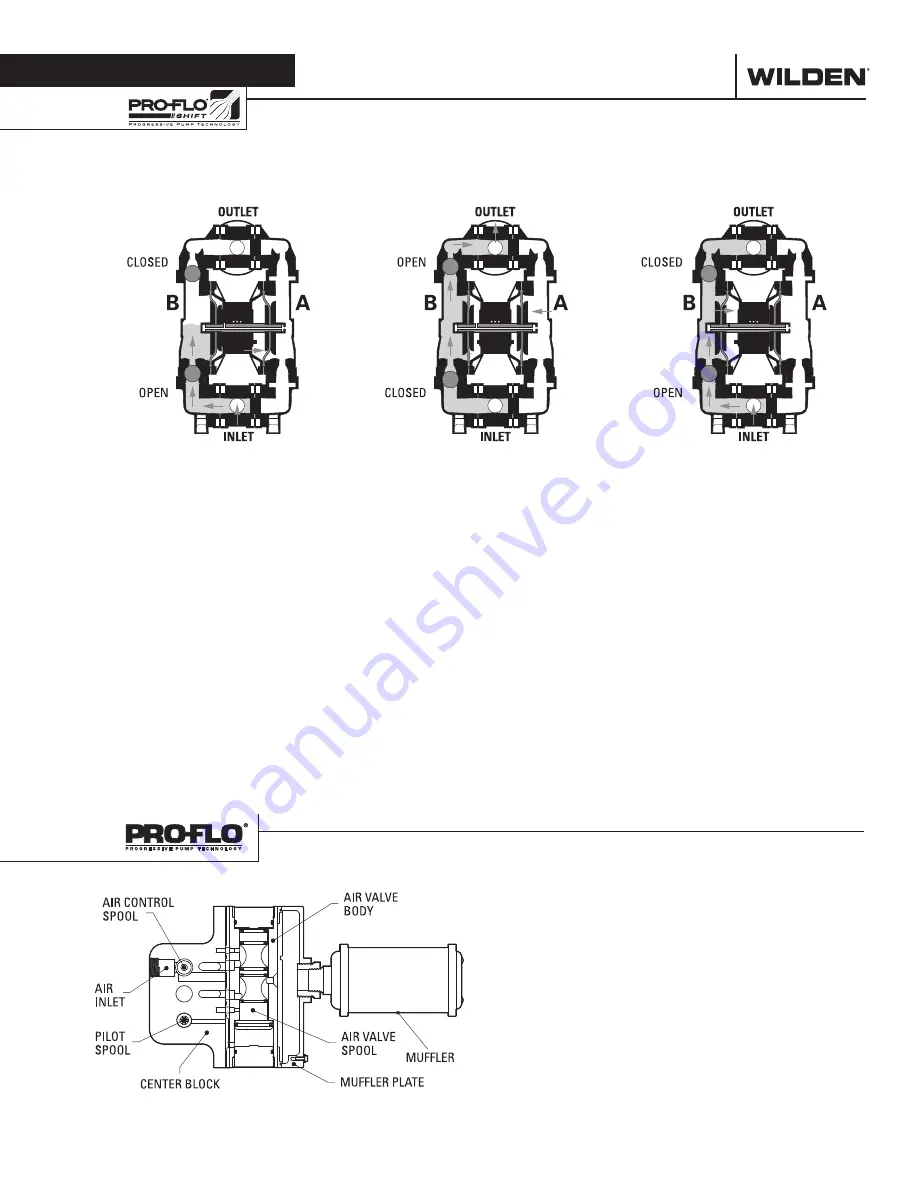
The Wilden diaphragm pump is an air-operated, positive displacement, self-priming pump. These drawings show flow pattern
through the pump upon its initial stroke. It is assumed the pump has no fluid in it prior to its initial stroke.
S e c t i o n 3
H O W I T W O R K S — P U M P
WIL-11112-E-01
3
WILDEN PUMP & ENGINEERING, LLC
H O W I T W O R K S — A I R D I S T R I B U T I O N S Y S T E M
The heart of the patented Pro-Flo
®
SHIFT Air Distribution System
(ADS) is the air valve assembly. The air valve design incorporates
an unbalanced spool with the small end of the spool being
pressurized continuously while the large end of the spool is
alternately pressurized, then exhausted to move the spool. The
air valve spool directs pressurized air to one chamber while
exhausting the other. The air forces the main shaft/diaphragm
assembly to move to one side – discharging liquid on that side
and pulling liquid in on the other side. When the shaft reaches
the end of the stroke, the inner piston actuates the pilot spool,
which controls the air to the large end of the air valve spool. The
repositioning of the air valve spool routes the air to the other air
chamber. The air control spool allows air to flow freely into the air
chamber for the majority of each pump stroke, but it significantly
restricts the flow of air into the air chamber when activated by the
inner piston near the end of the each stroke.
FIGURE 1 When air pressure is supplied
to the pump, the air valve directs pressure
to the back side of the diaphragm A. The
compressed air moves the diaphragm
away from the center section of the
pump. The opposite diaphragm is
pulled in by the shaft connected to the
pressurized diaphragm. Diaphragm
B is on its suction stroke; air behind
the diaphragm has been forced out to
the atmosphere through the exhaust
port. The movement of diaphragm B
towards the center section of the pump
creates a vacuum within the chamber B.
Atmospheric pressure forces fluid into
the inlet manifold forcing the inlet valve
ball off of its seat. Liquid is free to move
past the inlet valve ball and fill the liquid
chamber (see shaded area).
FIGURE 2 Once the shaft has reached
the end of its stroke, the air valve redirects
pressurized air to the back side of the
diaphragm B. This pressurized air is
also directed to the opposite side of the
diaphragm A through a passageway that
is routed through the common shaft and
outer piston. The pressurized air forces
diaphragm B away from the center
section while also pushing diaphragm
A to the center section. Diaphragm B is
now on its discharge stroke. Diaphragm B
forces the inlet valve ball onto its seat due
to the hydraulic forces developed in the
liquid chamber and manifold of the pump.
These same hydraulic forces lift the
discharge valve ball off of its seat, forcing
fluid to flow through the pump discharge.
The pressure on diaphragm A creates a
force on the shaft that is combined with
the pressure from diaphragm B. This total
load is transferred to the liquid creating a
liquid pressure that is two times greater
than the supplied air pressure.
FIGURE 3 At completion of the stroke,
the air valve again redirects air to the
back side of the diaphragm A, which
starts diaphragm B on its exhaust stroke.
As the pump reaches its original starting
point, each diaphragm has gone through
one exhaust and one discharge stroke.
This constitutes one complete pumping
cycle. The pump may take several cycles
to completely prime depending on the
condition of the application.