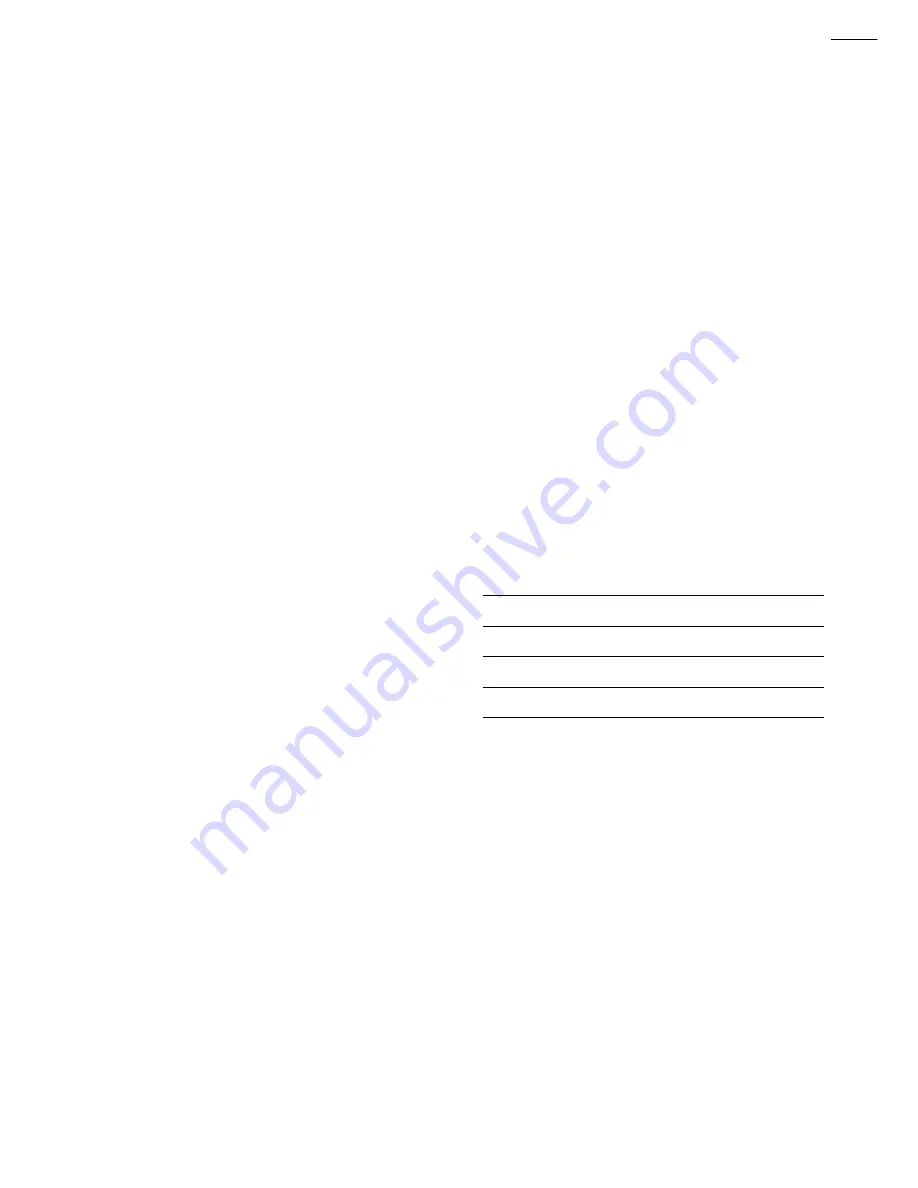
Weldmatic 350i + Weldmatic 500i
Model No CP139, CP140
15
Stick Welding (MMAW)
Connection for Stick Welding
It is important to select the electrode polarity
in accordance with the manufacturers
recommendations for that electrode. Most
common electrodes, including cellulose
types, are operated with the electrode at
positive polarity.
Stick Welding Operation
Be certain that you are wearing suitable
protective clothing, gloves etc and that you
are working in a non-hazardous area. If
necessary, refer again to
Section 1
-
Safe
Practices
in this manual.
Connect the work clamp to the work piece.
Place the desired electrode in the electrode
holder (electrode holder optional extra).
Turn on the power switch located on the rear
panel. Wait approximately 5 seconds as the
unit goes through its initiation sequence.
Press the Weld Mode button until the Stick
Mode light is on.
Select an appropriate welding current for
the electrode diameter by setting the knob
on the machine front panel. WIA AUSTARC
electrodes will give the best results.
To strike the arc, drag the end of the
electrode along the work piece as if striking
a match. As the arc initiates, lift the electrode
slightly away, aiming to establish an arc
length of approximately 3 mm.
As the electrode end is consumed, feed the
electrode into the arc in order to maintain
arc length. As a general rule, the arc should
be held as short as possible while still giving
stable burn off and good weld appearance.
An arc which is too long cause an unwieldy
flow of metal with a rough weld appearance
and reduced penetration.
An arc too short leads to a narrow weld
deposit and “stuttery” arc characteristics, and
the electrode is liable to freeze onto the work
piece.
As the solidified weld deposit forms, move
the end of the electrode slowly along
the weld path, aiming to maintain a pool
of moulten weld metal behind the arc.
Decreasing this rate of travel will result in a
wider weld deposit, and similarly increasing it
will narrow the weld deposit.
Always fill the crater which tends to form
at the end of a weld deposit, by pausing
momentarily before withdrawing the electrode
to break the arc. Unfilled craters are a point
of weakness, and can lead to weld cracking.
Current Range for General Purpose
Electrodes
Diameter (mm)
Current (Amps)
2.0
40 -60
2.5
60 - 85
3.2
90 - 130
4.0
130 - 180
Stick Remote Mode
When in stick remote Mode, the output can
be turned on and off with a remote switch
connected to the remote plug.