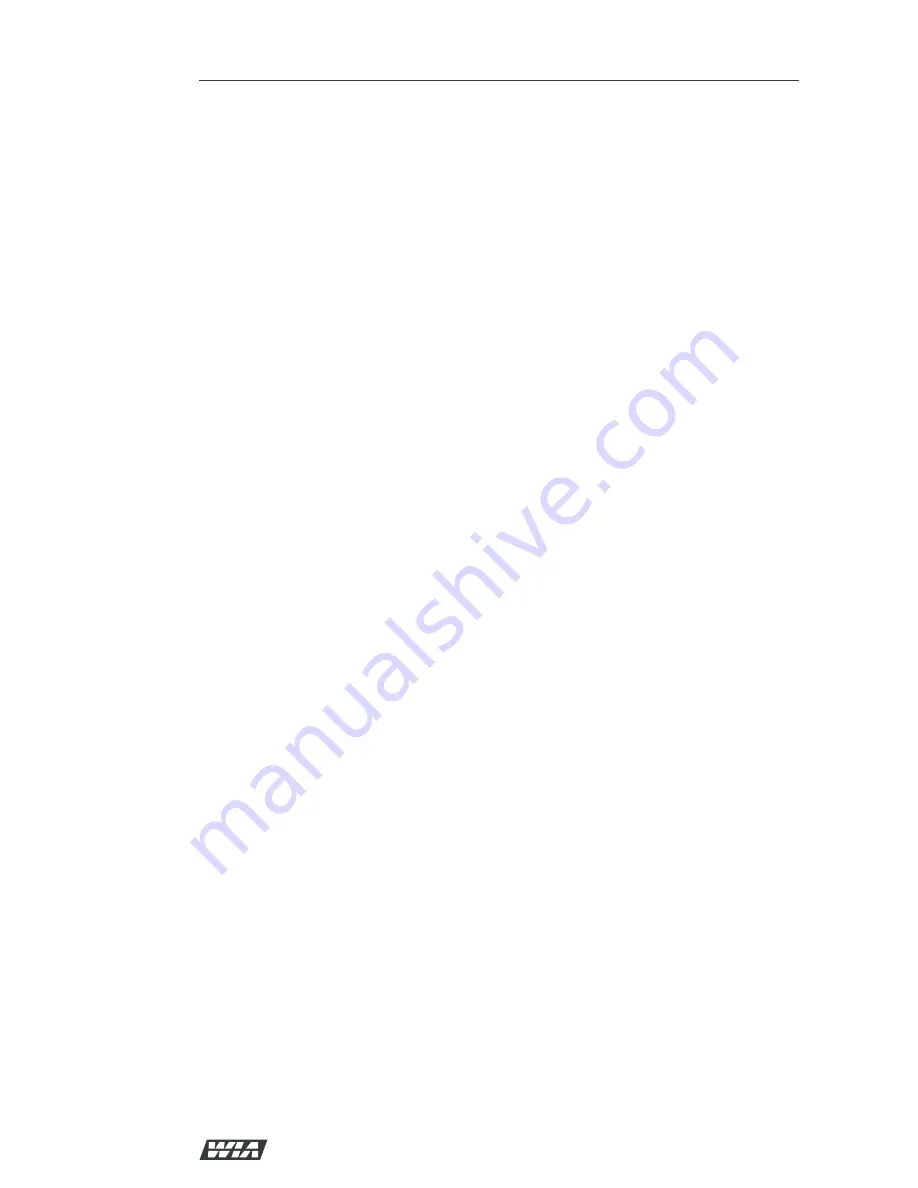
Weldmatic Fabricator
Operators Manual
Model No. CP117-2, Iss C 05/07
5
Quality, Reliability, Performance
Toxic Fumes
Adequate ventilation with air is essential.
Severe discomfort, illness or death can result
from fumes, vapours, heat, or oxygen depletion
that welding or cutting may produce. NEVER
ventilate with oxygen.
Lead, cadmium, zinc, mercury, and beryllium
bearing and similar materials when welded or
cut may produce harmful concentrations of
toxic fumes. Adequate local exhaust ventilation
must be used, or each person in the area as
well as the operator must wear an air-supplied
respirator. For beryllium, both must be used.
Metals coated with or containing materials
that emit fumes should not be heated unless
coating is removed from the work surface, the
area is well ventilated, or the operator wears
an air-supplied respirator.
Work in a confined space only while it is being
ventilated and, if necessary, while wearing air-
supplied respirator.
Vapours from chlorinated solvents can be
decomposed by the heat of the arc (or flame)
to form phosgene, a highly toxic gas, and lung
and eye irritating products. The ultra-violet
(radiant) energy of the arc can also decompose
trichlorethylene and perchlorethylene
vapours to form phosgene. Do not weld or
cut where solvent vapours can be drawn
into the welding or cutting atmosphere or
where the radiant energy can penetrate to
atmospheres containing even minute amounts
of trichlorethylene or percholorethylene.
Fire and Explosion Prevention
Be aware that flying sparks or falling slag can
pass through cracks, along pipes, through
windows or doors, and through wall or floor
openings, out of sight of the operator. Sparks
and slag can travel up to 10 metres from the arc.
Keep equipment clean and operable, free of
oil, grease, and (in electrical parts) of metallic
particles that can cause short circuits.
If combustibles are present in the work area, do
NOT weld or cut. Move the work if practicable,
to an area free of combustibles. Avoid
paint spray rooms, dip tanks, storage areas,
ventilators. If the work can not be moved,
move combustibles at least 10 metres away out
of reach of sparks and heat; or protect against
ignition with suitable and snug-fitting fire-
resistant covers or shields.
Walls touching combustibles on opposite sides
should not be welded on or cut. Walls, ceilings,
and floor near work should be protected by
heat-resistant covers or shields.
A person acting as Fire Watcher must be
standing by with suitable fire extinguishing
equipment during and for some time after
welding or cutting if;
• Combustibles (including building
construction) are within 10 metres.
• Combustibles are further than 10 metres but
can be ignited by sparks.
• Openings (concealed or visible) in floors
or walls within 10 metres may expose
combustibles to sparks.
• Combustibles adjacent to walls, ceilings,
roofs, or metal partitions can be ignited by
radiant or conducted heat.
After work is done, check that area is free of
sparks, glowing embers, and flames.
A tank or drum which has contained
combustibles can produce flammable vapours
when heated. Such a container must never
be welded on or cut, unless it has first been
cleaned as described in AS.1674-2. This includes
a thorough steam or caustic cleaning (or a
solvent or water washing, depending on the
combustible’s solubility), followed by purging and
inerting with nitrogen or carbon dioxide, and
using protective equipment as recommended
in AS.1674-2. Water-filling just below working
level may substitute for inerting.
Hollow castings or containers must be vented
before welding or cutting. They can explode.
Never weld or cut where the air may contain
flammable dust, gas, or liquid vapours.
Shock Prevention
Exposed conductors or other bare metal in the
welding circuit, or ungrounded electrically alive
equipment can fatally shock a person whose
body becomes a conductor. Ensure that the
equipment is correctly connected and earthed.
If unsure have the equipment installed by a
qualified electrician. On mobile or portable
equipment, regularly inspect condition of
trailing power leads and connecting plugs.
Repair or replace damaged leads.
Fully insulated electrode holders should be
used. Do not use holders with protruding
screws. Fully insulated lock-type connectors
should be used to join welding cable lengths.
Terminals and other exposed parts of electrical
units should have insulated knobs or covers
secured before operation.