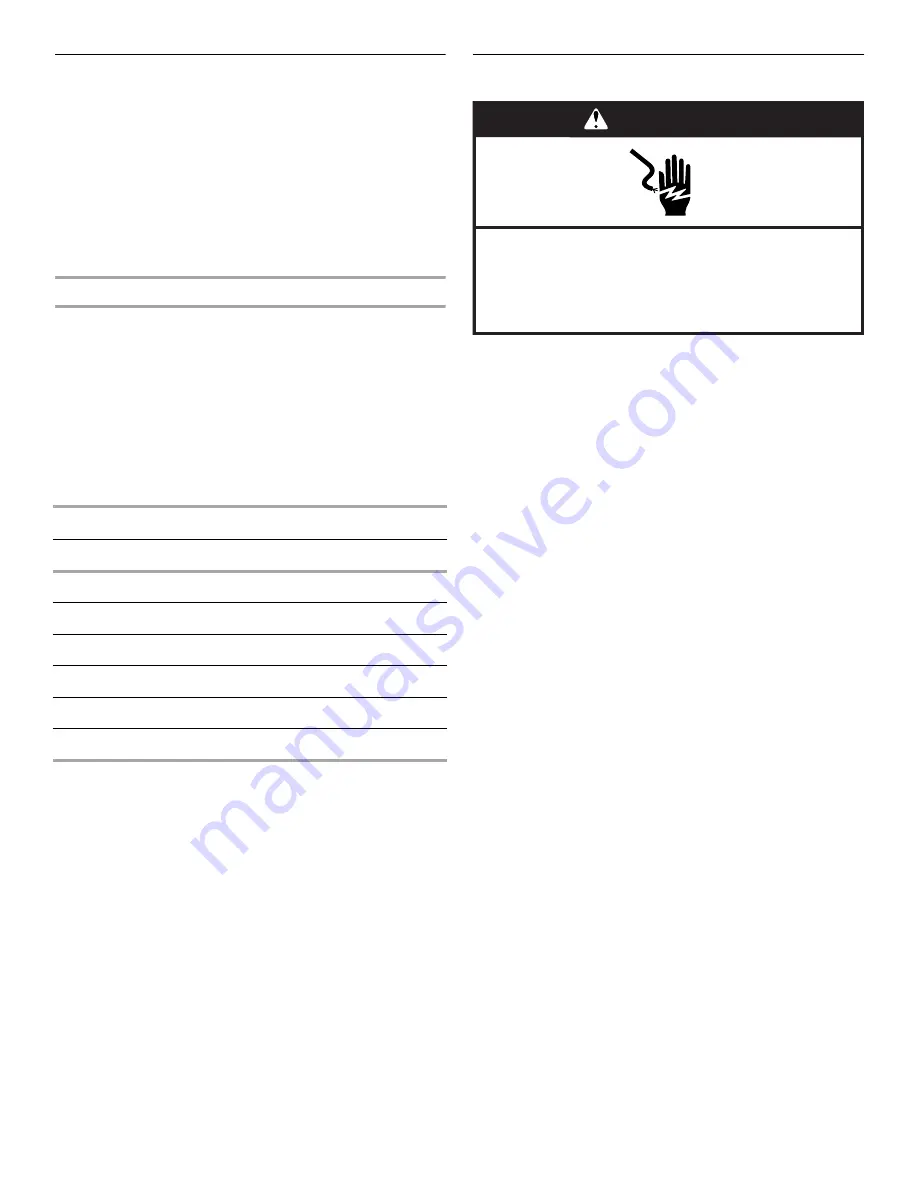
7
Install Ductwork
■
Install ductwork in accordance with NFPA 90B and any local
codes.
■
The use of flexible, noncombustible connectors between the
main trunk ducts and the supply and return air plenums is
recommended to minimize vibration transmission.
■
Plenums must be individually sealed to furnace casing with
ducts terminating inside the structure.
■
Flashing used to cover ductwork must permit removal of
access panels and top. See “Minimum Clearances” in the
“Locations Requirements” section.
Filters
Filters are not supplied with these furnaces; however, filters must
be used. It is the installer’s responsibility to install a filter rack with
the ductwork and to install properly sized filters in accordance
with the Minimum Required Surface Area for Disposable Filters
chart.
All return air must pass through a filter before entering the
furnace. An electronic air cleaner, filter rack or other accessible
filter arrangement must be installed in the return air ductwork.
Minimum recommended filter areas are listed in the Minimum
Required Surface Area for Disposable Filters chart, and are
based on a face velocity of 325 ft (99.1 m) per min. for disposable
filters and 525 ft (160 m) per min. for cleanable filters.
Make Electrical Connections
IMPORTANT:
■
Electrical wiring, disconnect means and over-current
protection are to be supplied by the installer. Refer to the
rating plate for the maximum over-current protection,
minimum circuit ampacity and operating voltage. See the
wiring connection diagrams in “Troubleshooting.”
■
Install an adequate sized branch circuit disconnect,
according to the NEC, within sight of and readily accessible
to furnace.
■
The cable or conduit and fittings connected from the
disconnect switch to the furnace wiring connections shall be
rated for outdoor use.
■
Check the furnace rating plate to determine whether the
system is rated single phase or three phase and follow the
appropriate instructions for connecting the pigtail leads.
■
Plug unused side entry holes with field-supplied plugs to
prevent moisture from entering the furnace.
■
Low voltage wiring must be separated from line voltage
wiring.
Minimum Required Surface Area for Disposable Filters
Nominal Cooling
Filter Area (sq. ft)
24,000
2.67
30,000
3.33
36,000
4.00
42,000
4.67
48,000
5.33
60,000
6.67
WARNING
Electrical Shock Hazard
Disconnect power before servicing.
Replace all parts and panels before operating.
Failure to do so can result in death or electrical shock.