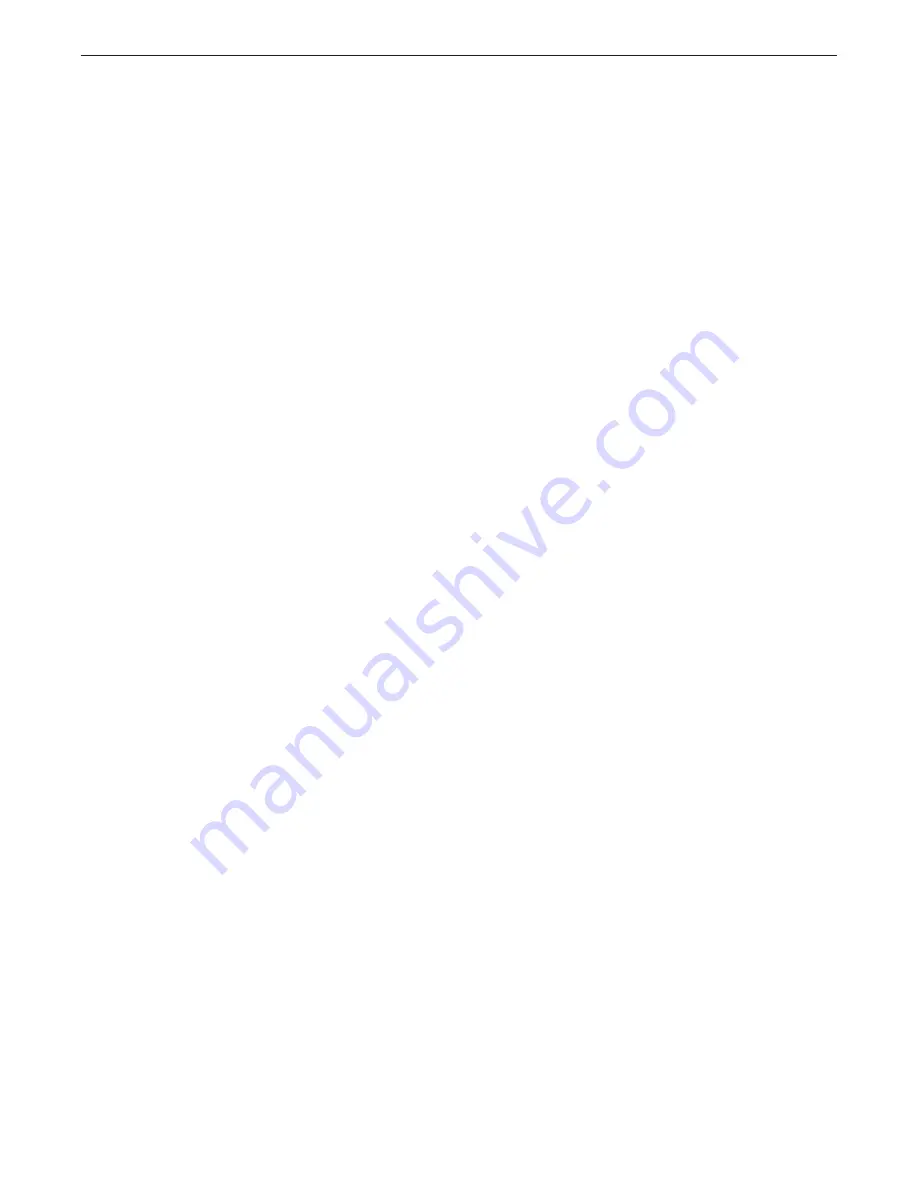
21
ProPress SP
Furnace Operations Manual
loaded suddenly. Once the press rod is in contact with the
mold plunger the other 40% is applied, bringing the initial
pressure up to the ceramic manufacturers rated pressure.
There is also a unique feature to salvage molds which have
hairline cracks in the top or side coming out of the burnout
oven. At the time the mold is inserted into the SP Press,
the furnace will ask the question, “Split Mold, reduced
pressure? No.” The default answer is “No,” for (Use full
regulator pressure), but if the mold already has cracks in it
you can turn the knob until the screen says “Yes,” and the
unit will automatically use 62% of the regulator pressure.
The pressing time will go up by about 1/3, but the reduced
pressure is more likely to avoid splitting the mold, finning,
etc. It still beats having to toss the split mold and start over.
Similarities & Differences
Mechanical Differences
The SP Pressing furnace uses a special actuator cylinder
with an inflatable piston seal and a return spring to bring
the press rod back to the top position when not pressing.
The reason you should care about this is that the system
was designed to work
only with an applied pressure of
70 PSI/4.8 BAR. In actuality, only a maximum of 60 PSI
ever reaches the investment mold because the return
spring counteracts 10 PSI of air pressure.
The Split
Mold reduced pressure applies only 46 PSI air pressure,
but again, this is reduced by the return spring to a 37
PSI equivalency.
DO NOT REDUCE THE APPLIED AIR
PRESSURE EITHER BELOW 70 PSI/4.9 BAR OR ABOVE
72 PSI/5.0 BAR or unreliable operation will result.
The
furnace software will prompt you to adjust the pressure
inside this range if it is not already.
Pressing Parameters
There are no new parameters with the SP Pressing
Furnace. One parameter, however, is used in a slightly
different way. The Press Time parameter is still the ceramic
manufacturer’s specified time under pressure, but it should
only come into play rarely if ever. The pressure sensing
technology in the SP Pressing Furnace determines the
actual termination of the pressing cycle. This can be as
much as 60% less time than the manufacturers specified
Press Time.
The Press Time program parameter merely
serves as a “backup timer” or time not to exceed.
The
worst that can happen is that the Press Time will run to
the manufacturer’s rated press time.
Fusing Adjust Parameter
The Fusing Adjust parameter is the next to last parameter
when entering a program. It’s default value is zero
degrees. If you desire to modify the Hold Temperature,
but don’t want to disturb standardized program values,
you can enter a negative offset if the furnace is currently
“overfiring” or a positive value if the furnace is currently
“underfiring”. This offset will be subtracted from or added
to the Hold Temperature parameter. If no compensation
is needed, just ignore the parameter and the default zero
compensation will be used.
Process Differences
The conventional pressing process can still be used if
desired. The SP Pressing Furnace can operate just like the
Pro Press 200, meaning that the air pressure is applied at
a constant level throughout the press cycle and the Press
Time parameter controls the termination of the cycle when
the timer expires. This does not take advantage of the SP
Pressing Furnace’s advanced pressing technology.
During the running of a Conventional program the vacuum
pump will come on during the Rate Rise cycle, and turn
off when the vacuum level reaches 71 cm (or other value
if you change the default 71cm) of mercury inside the
muffle. If the Furnace is set up to use intermittent vacuum
the pump may intermittently cycle on and off as needed to
stay above 68 cm of mercury.
The same applies to the SP Pressing mode of pressing
with one notable addition. A few seconds before the
Hold Time expires, the vacuum pump will come on and
remain on until the pressing cycle finishes (typically 1 to
2 minutes). This serves two purposes; (1) it insures the
best possible vacuum when the ceramic is in a molten
state, (2) it reduces the electronic noise of the electrical
pump surge current which can disturb the ultra-sensitive
pressure digitization signal. The pump will turn off
automatically when the SP Pressing electronic pressure
signal determines the mold is fully filled, as well as set the
muffle temperature back to the idle value. There will be
some delay between the time the pump turns off and the
table lowering. This is due to the time it takes for air to re-
enter the muffle. The table cannot be lowered any quicker
because the vacuum inside the muffle is holding the table
closed until the incoming air relieves the vacuum.
Conventional and SP Pressing programs can exist side by
side in the Furnace’s program list. Conventional
program
names do not have the “%”
character as the first letter of
the Program Name,
SP Pressing programs do have the
“%” as the first letter of the Program Name.
This special
character in the program name is how the SP Press “knows”
to use the SP Press technology on a given program.