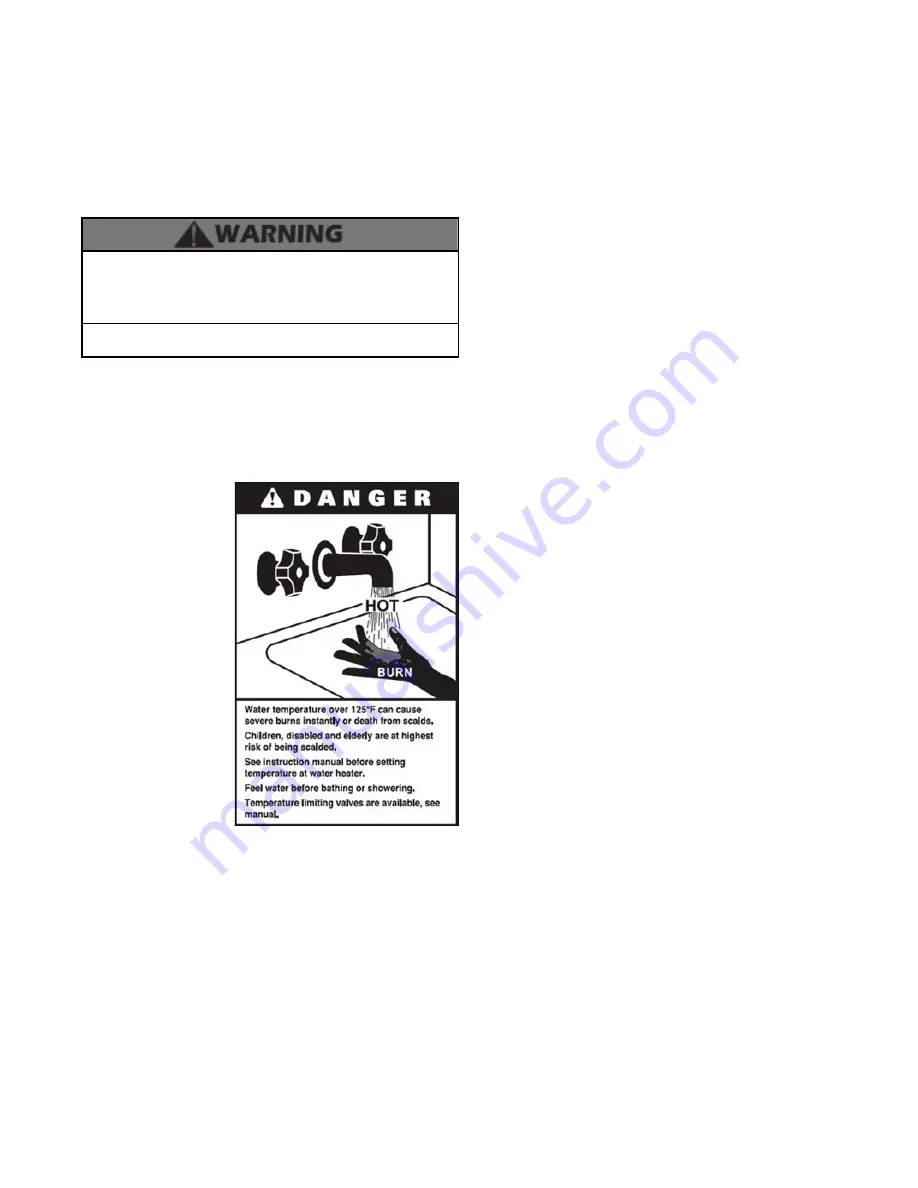
WHL-033 Rev. 1.29.16
33
tank sensor is used, the control will automatically detect its
presence and a demand for heat from the indirect water heater
will be generated when the tank temperature falls below the
user selected set point by more than the user selected offset.
The demand will continue until the sensor measures that the
indirect water heater temperature is above the set point.
2. Connect the indirect tank sensor (7250P-325) to the
terminals marked DHW SENSOR (shown in Figure 23) in the
electrical junction box.
Failure to use the correct sensor may result in tank
temperature being either above or below set point, and
could result in decreased performance, substantial property
damage, or heightened risk of injury or death due to scalds.
Caution should be used to ensure neither of these terminals
becomes connected to ground.
NOTE:
If sensor wires are located in an area with sources of
potential electromagnetic interference (EMI), the sensor
wires should be shielded, or the wires routed in a grounded
metal conduit. If using shielded cable, the shielding should be
connected to the common ground of the boiler.
J. Optional 0-10 Volt Building Control Signal
1. A signal from a
building management
system may be
connected to the boiler
to
enable
remote
control. This signal
should be a 0-10 volt
positive-going
DC
signal.
When
this
input is enabled using
the installer menu,
a
building
control
system can be used to
control the set point
temperature of the
boiler. The control
interprets the 0-10 volt
signal as follows; when
the signal is between 0
and 1.5 volts, the boiler
will be in standby mode,
not firing. When the signal rises above 1.5 volts, the boiler will
ignite. As the signal continues to rise towards its maximum of
10 volts, the boiler will increase in set point temperature. See
Part 10 for details on the setting of function 16.
2. Connect a building management system or other auxiliary
control signal to the terminals marked 16, 0-10 VOLT + and
17, 0-10 VOLT – in the electrical junction box (shown in Figure
23). Caution should be used to ensure that the 0-10 VOLT +
connection does not become connected to ground.
K. Optional High Gas Pressure Switch
1. If an optional high gas pressure switch is used, it should be
installed on the outlet side of the gas valve. This is normally
closed and will open if the pressure goes above 1.5” w.c. on
the outlet side.
2. Locate the two pigtails hanging from the electrical box
L. Optional Low Gas Pressure Switch
1. If an optional low gas pressure switch is used, it should be
installed on the inlet side of the gas valve. This is normally closed
and will open if the pressure goes below 1” w.c. on the inlet side.
2. Locate the two pigtails hanging from the electrical box inside
of the boiler cabinet. Remove and discard the jumper plug from
one of the unused pigtails.
3. Connect the low gas pressure switch to the pigtail that you
removed the jumper plug from.
M. Optional Flow Switch
NOTE:
Follow the more detailed instructions included with the
flow switch kit for proper installation steps.
1. Attach the correct flow paddle to the flow switch.
2. Thread brass tee onto outlet nipple using pipe dope.
Make
certain the branch points up on horizontal runs.
3. Thread flow switch into tee using pipe dope.
Make certain the
FLOW arrow points in the correct direction.
4. Disconnect red wire on the low water cut off probe and
connect it to the red wire from the wire harness (included in kit).
5. Feed green ground wire into boiler through the wire access.
6. From the front of the boiler, feed the ground wire up into the
control box.
7. Once into the control box, attach the green ground to the
ground bus connection.
8. Connect red wire from flow switch to boiler wire harness.
9. When installation is complete, power up the boiler and use
the control to access installer parameter #20 and change the
default value to 2 (see Part 11 in this manual). When done, create
a demand and observe boiler function to verify the installation is
working properly.
NOTE:
Installing the optional flow switch will disable the built-
in low water cutoff. If a flow switch and a low water cutoff are
necessary for the installation, purchase and install the optional
UL353 LWCO (available from Westinghouse, Part # 7350P-601).
In this installation, it is recommended to install the flow switch
kit first.
inside of the boiler cabinet. Remove and discard the jumper plug
from one of the unused pigtails.
3. Connect the high gas pressure switch to the pigtail that you
removed the jumper plug from.
N. Optional UL353 Low Water Cut-Off Interface Kit
1. If an optional UL353 low water cut-off (LWCO) interface kit is
used, the control box of the kit should be mounted to the left
side of the boiler cabinet near the low water cut-off probe, which
is located on the outlet nipple of the boiler.
2. If the optional flow switch is present on the boiler, then the
orange wire from the LWCO control box is left unconnected.
If the optional flow switch is not installed on or connected to
the boiler, remove the wire connected to the low water cut-off
probe on the boiler and connect it to the orange wire from the
newly mounted LWCO control box.
3. Connect the single red wire from the control box to the low
water cut-off probe on the boiler.
4. Route the rest of the wires through the hole provided in the
cabinet and down by the main electrical enclosure.
5. Locate the two pigtails hanging from the main electrical
enclosure. Select the pigtail which has a white, red, and brown
wire in it. If the pigtail is connected to a gas pressure switch, skip
to step 7. If this pigtail is not connected to a gas pressure switch,
Содержание WBMC**500
Страница 36: ...WHL 033 Rev 1 29 16 36 Figure 27 Internal Connection Diagram ...
Страница 59: ...WHL 033 Rev 1 29 16 59 Figure 32 500 Combustion System Replacement Parts Model ...
Страница 60: ...WHL 033 Rev 1 29 16 60 Figure 33 850 Combustion System Replacement Parts Model ...
Страница 61: ...WHL 033 Rev 1 29 16 61 Figure 34 Water Side Replacement Parts All Models ...
Страница 62: ...WHL 033 Rev 1 29 16 62 Figure 35 Cabinet Replacement Parts All Models ...
Страница 69: ...WHL 033 Rev 1 29 16 69 Maintenance Notes ...