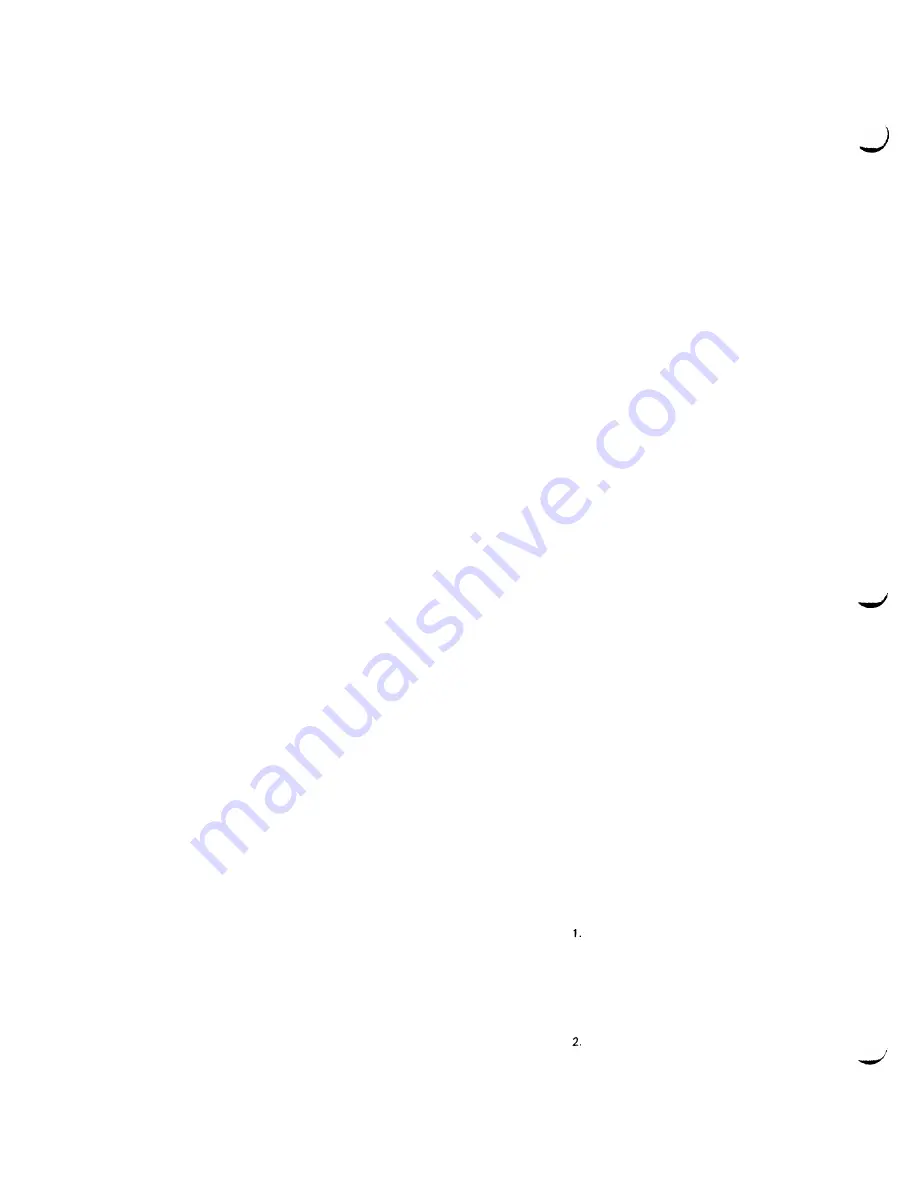
Page 2
Inspection And Handling
When unit is received, it should be checked for
visible or concealed damage. If damage has oc-
curred it should be reported to the carrier im-
mediately and claim filed.
Units are factory mounted on two permanent
angle beam, carbon steel skids. Four 2-7/8” lif-
ting eyes are provided in the skids to allow rig-
ging. Spreader bars must be used between rig-
ging lines to prevent damage to the unit.
Rollers may be used under the skids to
facilitate moving the unit a short distance.
Physical damage to the unit, after accep-
tance, is not the responsibility of
Westinghouse.
Location And Mounting
Westinghouse Model PD060 135 Air Cooled
Packaged Water Chillers are designed for out-
door application and may be mounted on roof
or at ground level. Air flow through the con-
denser is vertical and the unit may be located
adjacent to outside of building or on roof
without regard for prevailing wind direction.
Since these units are air cooled, the flow of air
to and from the condenser coil must not be im-
peded. There must be no obstruction above
the unit that would tend to deflect discharge
air downward where it could be recirculated
back to the inlet of the unit. The required
overhead air space should be a minimum of 8
feet. Duct work must not be applied to the fan
outlets.
The unit must be installed with sufficient
clearance for air entrance to the condenser coil
and for servicing access. The unit should be
located not closer than four feet from any wall
or other obstruction. Clearance must be provid-
ed at either end of the unit to permit removal
of tubes from the chiller.
Unit must be set on a solid and level founda-
tion.
On roof installations the unit should be
mounted on subbeams which span load- bear-
ing walls to prevent excessive vibration.
On ground level installations the unit should be
mounted on a substantial base that will not
settle. A one piece concrete slab with footings
extended below the frost line is recommended.
A space should be left between the slab and
the building to prevent the transmission of
sound and vibration.
Vibration mounts may be used for roof
mounted units or other locations where noise
might be objectionable.
Wiring
A unit wiring diagram showing the required
power supply characteristics and all factory
supplied wiring details is provided with unit.
Separate, field supplied, disconnects must be
installed in the power supply and should be
within the sight of the unit.
Separate 110 volt power source must be field
supplied to provide power for control and
heater circuits.
Chiller Piping
The chiller inlet water pipe should be con-
nected to the expansion valve end of the liquid
chiller barrel and the outlet water pipe con-
nected to the opposite end of the chiller barrel.
A flow switch must be installed in a straight
horizontal section of the chilled water piping.
Chiller water pressure drop data for the PD
units are shown in Table 2. Gauges should be
installed in the piping to and from the chiller to
measure the pressure drop and to insure the
proper (GPM) flow rate.
A strainer should be installed in the piping on
the inlet side of the chiller and vibration
eliminators should be employed on both the in-
let and outlet pipes. Air vents should be
located at all high points in the piping system.
Vents should be located to be accessible to
servicing. Drain connections should be provid-
ed at all low points to permit complete
drainage of chiller and piping system.
The chiller water piping should be insulated to
reduce heat pickup and to prevent condensa-
tion. If the system is for year round operation
or it it will not be drained in the winter, the
chilled water piping should be protected
against freezing by electric heating cable or
other suitable means.
Upon completion of chiller piping, start the
system water pump and purge air from the
system. Air purging should be done from the
high points in the water circuit. Purging of the
chiller barrel may be accomplished through the
vent pipe located on the top of the chiller com-
partment. Failure to purge air from the water
circuit will result in inadequate water flow and
may cause the unit to cut out on low water
flow freeze protection.
S t a r t - U p
Refer to start, test, and check list included
with this manual
Check all electrical and mechanical connections
for shipping looseness and tighten all screws
on electrical terminals.
Activate the 120 volt chiller and crankcase
heater circuit 24 hours prior to unit start-up.
Rotate each fan prior to start-up. Fans should
turn freely. On belt drive units check belt ten
sion and pulley alignment. After two weeks of
operation, readjust belt tension to ac-
commodate for belt stretching.
Check all control settings as specified in Table
1.
Check the compressor oil level through
crankcase sight glass. The oil level should be
1/3 to 2/3 of the way up on the sight glass. If
oil is low, add oil in accordance with the direc-
tions in “Maintenance” instructions below.
Caution: The compressor suction and
discharge service valves must be open or
backseated before starting the compressor.
Close the valves no more than two turns to
give the pressure taps access to the system for
pressure readings, charging, etc. All receiver
valves must also be open for sustained opera-
tion.
All compressors are solid mounted on isopads,
therefore, compressor hold down bolts must
not be loosened. Loosening these bolts will
cause excessive vibration of the compressor
and may result in refrigerant line breakage.
Prior to start- up check all compressor hold
down bolts for tightness.
To start unit, throw main disconnects into
“ON” position and place system “OFF-ON”
switch (S1) in “ON” position. (Note: If unit is
equipped with optional lock-out timer, unit will
not start until timer has completed its cycle.)
Once the main disconnect switches and system
“ON-OFF” switch (S1) have been energized
and providing chiller water flow has been
established, the unit will operate automatically
in response to the chiller water thermostat.
Maintenance
Condenser
Units equipped with direct drive fans have in-
herently protected motors and permanently
lubricated bearings, which do not require
lubrication.
Units equipped with belt drive fans have in-
herently protected motors. Fan belts, fan bear-
ings and motor bearings require periodic
maintenance as follows:
Fan Belts After two weeks operation, the
belts will have nearly reached their perma-
nent stretch, therefore, each belt should be
checked again and proper adjustments
made. To maintain good fan and motor
operation, the belt tension should be check-
ed at three month intervals.
Fan Bearings Each fan shaft is provided
with ball bearings of the relubricable type.
Each bearing is provided with grease fit-
tings, accessible through the individual
motor access panels. It is recommended the
bearings be greased by adding 4 to 5 shots