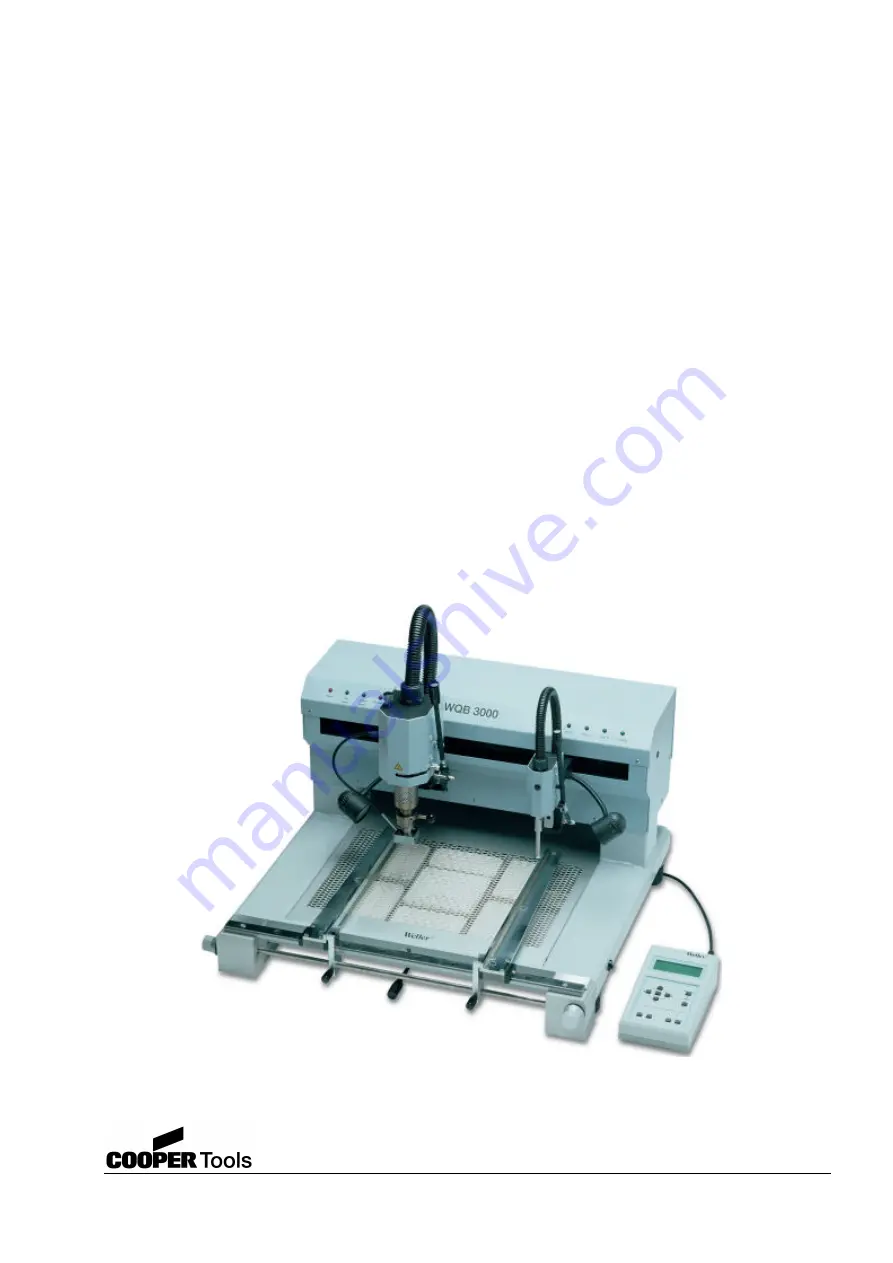
22
Cooper Tools GmbH, Carl-Benz-Str. 2, 74354 Besigheim, P.O. Box 1351
Germany, Tel: (07143) 580-0, Fax: (07143) 580108
1
Description
The WQB 3000 Repair System is designed for carrying out demanding repair work, both on BGA as well as
on FINEPITCH components. A well thought-out design concept combines reliability and maximum process
control with ease of use and technically mature detail solutions. Useful accessories increase the possible
uses of this repair workstation.
For the universal circuit board repair of SM components, it is necessary to effectively pre-heat the circuit
board from below, and from above to precisely heat the components to be repaired to the reflow
temperature, as well as to reliably control the process. On the WQB 3000 the temperature-regulated 2-zone
infrared bottom heater provides rapid warm up and homogeneous substrate temperatures. The hot gas top
heater, with digital control electronics for temperature monitoring and regulation of the air flow rate, facilitates
the finely metered supply of heat to the components. A temperature sensor placed directly in the hot gas
nozzle efficiently regulates the top heater and thus provides maximum process control.
On the digital programming unit all process steps can be programmed, saved, and, if necessary, protected
against unauthorised use as required. The most important process parameters are optionally displayed on
the LC display during operation. The programming unit assists with the determination of temperature profiles
and in this way facilitates the definition of optimal soldering process data in the easiest possible manner. The
programming of comprehensive special functions permits the adaptation of the process to a very wide range
of boundary conditions, and thus enables repairs to be made even on the most difficult assemblies.
The proven, patented mini template system from WELLER is available for the re-positioning of components
on the circuit board after desoldering and partial application of solder paste.