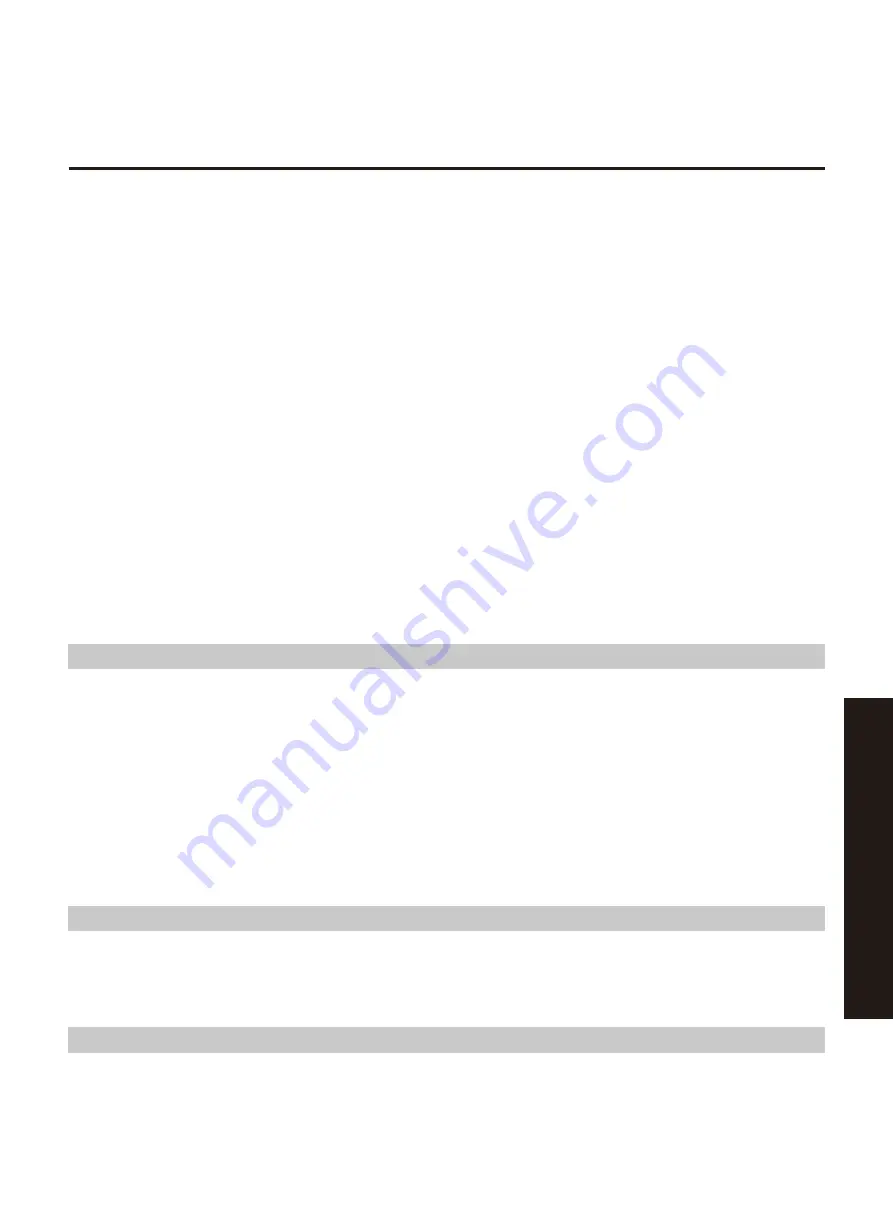
MAINTENANCE AND CHECK TROUBLE
1 Maintenance
Dust should be removed with dry and clean compressed air regularly. If the welder is used in a heavily polluted
environment with dense smoke and polluted air, dust must be removed from the welder each month.
The pressure of compressed air should be reasonable so that damage is not done to small elements in the welder.
Regularly check the connection of electric circuit in the welder and make sure circuit be connected properly and joint is
secured (especially inserted joint or element). If the cases of rusting or loosening are found, the rust layer or oxidized film
should be removed with abrasive paper and then the joint should be connected again and tightened firmly.
Entry of water or steam into the interior of the welder should be avoided. If this condition occurs, the welder should
undergo drying treatment. Then the welder is measured for insulation by a megohm-meter (including the area between
connecting points and the areas between the connecting points and shell). Welding can go on only when evidence shows
no abnormality.
If the welder is not to be used for a long time, it should be replaced in the original package and kept in a dry environment.
1
2
3
4
5
2 Check Fault
Phenomena enumerated here may have something to do with the parts, gas, environmental factors and power supply you use
and efforts should be made in improving the environment to avoid occurrence of such cases.
A Black welding spot:
——This shows the welding spot is oxidized without being protected effectively and you can make the following
inspection
:
BE SURE YOUR GAS IS 100% ARGON AND NOT A MIX.
1.
Make sure that the valve of argon cylinder has been opened with sufficient pressure. As a rule, if the pressure
within the cylinder is lower than 0.5MPa, then it is necessary to refill the cylinder.
2.
Check if the argon flow-meter is turned on with sufficient flow. You can select different flow rates in light of
varying welding current, but too small flow may lead to inadequate gas stiffness and thus failure to cover all the
welded spots. We suggest argon flow should never be lower than 3l/min no matter how weak the current will be.
3.
The easiest way to check gas delivery is to touch the nozzle of welding torch to see whether the gas passage of the
welding torch is blocked.
4.
Poor sealing of gas passage or lower gas purity will also give rise to welding quality trouble.
5.
Strong air flow in the environment may also lead to deterioration of welding quality.
B Difficulty in arc starting with easy arc breaking:
1.
Make sure that the tungsten electrode in use is of good quality as discharge ability of inferior tungsten electrode
may fail the requirement
;
2.
Tungsten electrode without sharpening treatment is also unable to start arc and leads to unstable arc. Improper
gas will also cause unstable High Frequency arc Initiation.
C Output current can’t reach the rated value:
Deviation of power voltage from the rated value will lead to unconformity of output current value with the set value.
When power voltage is lower than the rated value, maximum output current of the welder may also be lower than the
rated value.
MAINTENANCE AND CHECK TROUBLE
33
Содержание TIGACDC250GD
Страница 1: ...TIGACDC250GD ...
Страница 2: ...1 Technical support 651 329 2686 www weldpro com Tel 651 342 1459 ...
Страница 3: ...2 STOP ...
Страница 6: ...Weldpro Safety 5 Weldpro Safety ...
Страница 32: ...e Picture 19 31 ...
Страница 37: ......
Страница 38: ......