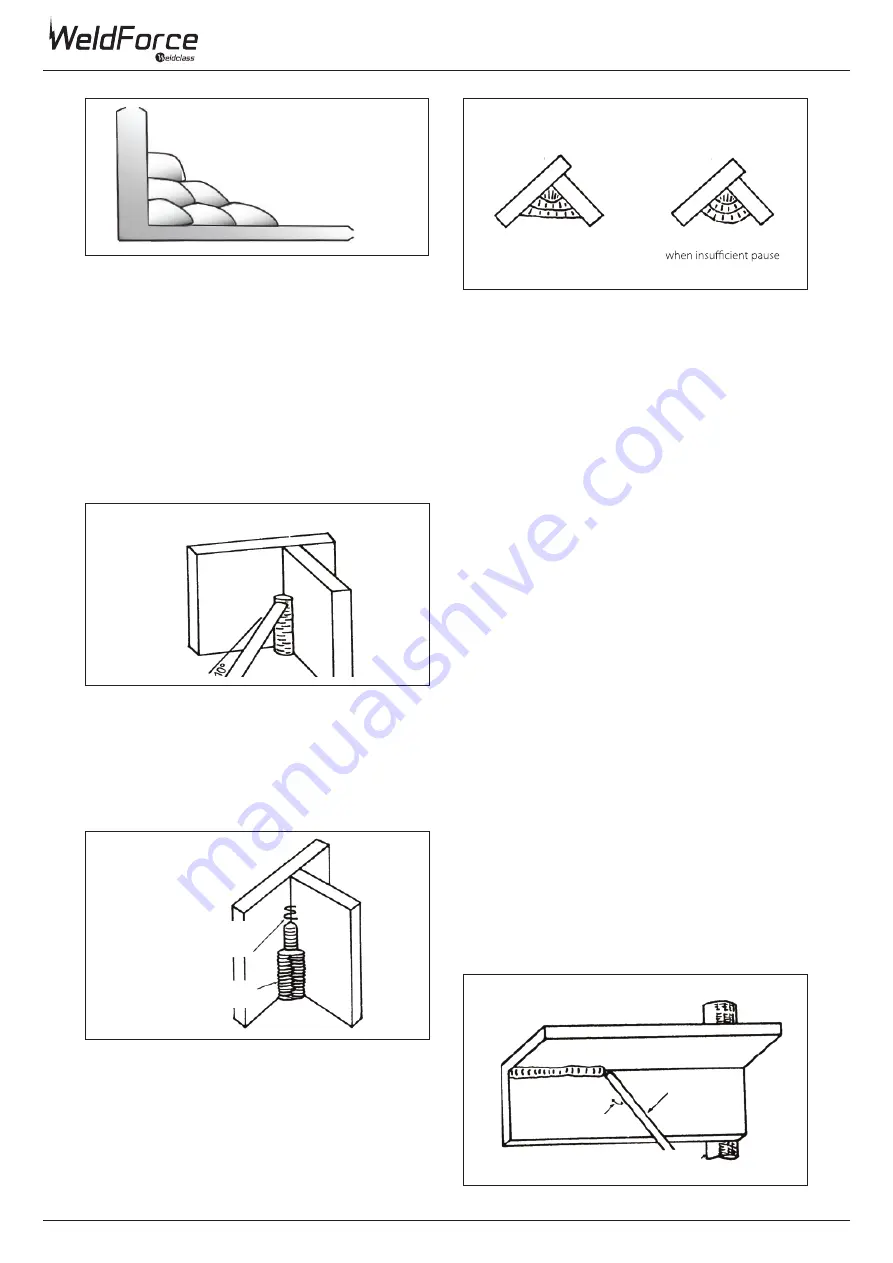
by
12
C. Vertical Welds
1. Vertical Up
Tack weld a three feet length of angle iron to your
work bench in an upright position. Use a 3.2mm
E7014 Stick electrode and set the current at 100
amps. Make yourself comfortable on a seat in front
of the job and strike the arc in the corner of the
fillet. The electrode needs to be about 10º from the
horizontal to enable a good bead to be deposited.
Refer Fig. 1-25.
Use a short arc, and do not attempt to weave on
the first run. When the first run has been completed
deslag the weld deposit and begin the second run
at the bottom. This time a slight weaving motion
is necessary to cover the first run and obtain good
fusion at the edges.
At the completion of each side motion, pause for a
moment to allow weld metal to build up at the
edges, otherwise undercut will form and too much
metal will accumulate in the centre of the weld.
Figure 1-26 illustrates multi-run technique and
Figure 1-27 shows the effects of pausing at the
edge of weave and of weaving too rapidly.
Multi-Runs in HV Fillet Weld
(Fig 1-24)
Single Run Vertical Fillet Weld
(Fig 1-25)
Weaving motion for
second and subsequent
runs
Pause at edge
of weave
Multi Run Vertical Fillet Weld
(Fig 1-26)
Examples of Vertical Fillet Welds
(Fig 1-27)
Pause at edge of weave
allows weld metal to build
up and eliminates undercut
Note: Weld contour
at edge of weave
CORRECT
INCORRECT
Tilted 10
o
in
line of travel
Overhead Fillet Weld
(Fig 1-28)
Angle tacked to pipe
45
o
to plate
2. Vertical Down
The E7014 Stick electrode makes welding in this
position particularly easy. Use a 3.2mm electrode
at 100 amps. The tip of the electrode is held in light
contact with the work and the speed of downward
travel is regulated so that the tip of the electrode
just keeps ahead of the slag. The electrode should
point upwards at an angle of about 45º.
3. Overhead Welds
Apart from the rather awkward position necessary,
overhead welding is not much more difficult
that down hand welding. Set up a specimen for
overhead welding by first tacking a length of angle
iron at right angles to another piece of waste pipe.
Then tack this to the work bench or hold in a vice
so that the specimen is positioned in the overhead
position as shown in the sketch.
The electrode is held at 45º to the horizontal and
tilted 10º in the line of travel (Figure 1-28). The tip
of the electrode may be touched lightly on the
metal, which helps to give a steady run. A weave
technique is not advisable for overhead fillet welds.
Use a 3.2mm E6013 Stick electrode at 100 amps,
and deposit the first run by simply drawing the
electrode along at a steady rate. You will notice
that the weld deposit is rather convex, due to the
effect of gravity before the metal freezes.
Содержание WeldForce WF-135s stick
Страница 13: ...13 MMA Stick Troubleshooting...
Страница 20: ...by www Weldclass com au WF 135S...