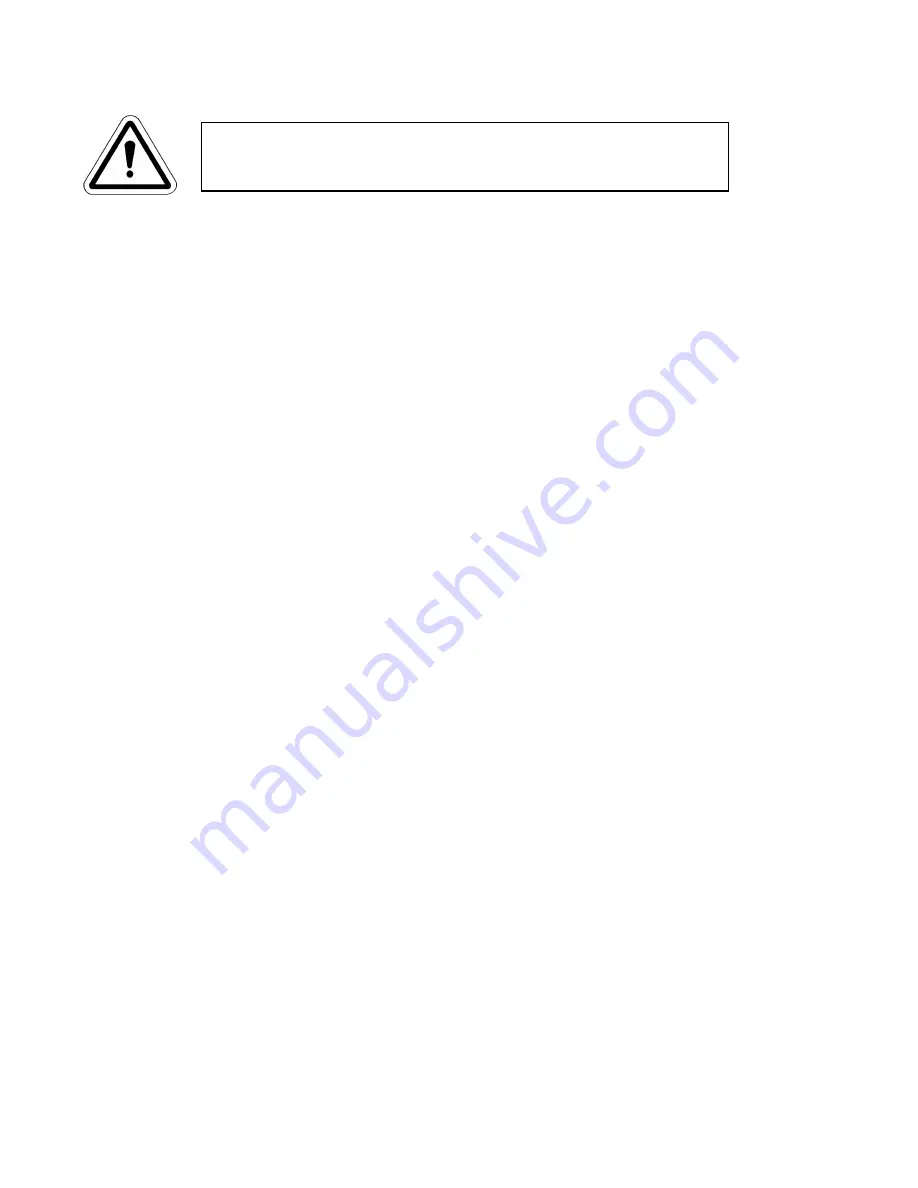
7
1.9 Vacuum Pump Oil
CAUTION
The vacuum pump is shipped without oil inside to prevent
possible spillage during shipment. Oil must be added prior to use.
Remove the fill plug located on the top of the oil case and add the oil supplied in a bottle packaged with each
pump. Both the fill and drain plugs have knurled edge and a center slot for easy turning either by hand or with a
screwdriver.
Be sure the pump is filled with oil to the level indicated on the oil fill window. When additional oil is required, use
only DIRECTORR® Premium Vacuum Pump Oil; pump performance is not guaranteed with other brands of oil.
Do not overfill the pump, and be sure to replace the oil fill plug.
After the pump has been running for at least 15 minutes, check the oil level again. The oil level should be
maintained between the “add” mark and the “full” mark on the oil level window while the pumpis operating. Do
not overfill; excess oil tends to be splashed out the pump exhaust. The ideal level is four “ribs” down from the
top of the oil case, or about ½ in. below the “full” mark.
1.10 Pumping Condensable Vapors
Liquids can collect in a vacuum pump by either being ingested or sucked directly into the pump, or by its vapors
condensing in the pump.
If the application requires pumping directly on a liquid, or on samples whose surface contain large amounts of
liquid, the initial pumping may draw some of this liquid directly into the pump. The use of a liquid trap is
recommended. A plastic flask of sufficient size is often adequate. Please it nearest the source of the liquid being
pumped. Inlet and outlet connections should be make at or near the to prevent any of the trapped liquid from
being drawn out by the pump.
To prevent condensable vapors from condensing in the vacuum pump, several measures should be taken. These
include:
A. Control of the pressure in the vacuum system. Not all vacuum systems need to, or should be, operated at the
lowest pressure possible for the pump. Rotary evaporators, for example, depend on a pressure setpoint high
enough to prevent the distillate collected from revaporiazing. If revaporized, it can easily recondense in the
pump.
Use of a bleed valve and pressure gauge is recommended.
Use the Cat. No. 1423 Vacuum Manifold Valve/Gauge Kit.
B. Trap condensable vapors in a cold trap. If the pressure of the system must be set at or near the ultimate
pressure of the pump, or if the vapor load is high, use a cold trap is recommended. It should be placed away
from sources of heat, such as the pump, for maximum efficiency.
Several types of cold traps are available. They include:
1)
Dry Ice/Alcohol Slurry Traps which maintain a temperature of about –75 C.
2)
Liquid Nitrogen Traps which maintain a temperature of about –100 C.
3)
Refrigerated Traps which typically maintain temperatures between about – 25 to –80 C.
See Section 9 – Accessories for a selection of these traps. Consult a handbook for the melting temperatures
of the liquids being pumped. Some very heavy vapor loads may require these of two traps in series. Once the
trap is installed and charged, wait for it to reach its minimum temperature before turning on the vacuum pump.
The condensed vapor must be removed from the trap on a frequent basis to prevent revaporization via
sublimation, and to allow the trap to work at its peak efficiency.
Содержание 8890
Страница 19: ...19 TROUBLESHOOTING 6 4 Trouble Shooting Guide ...