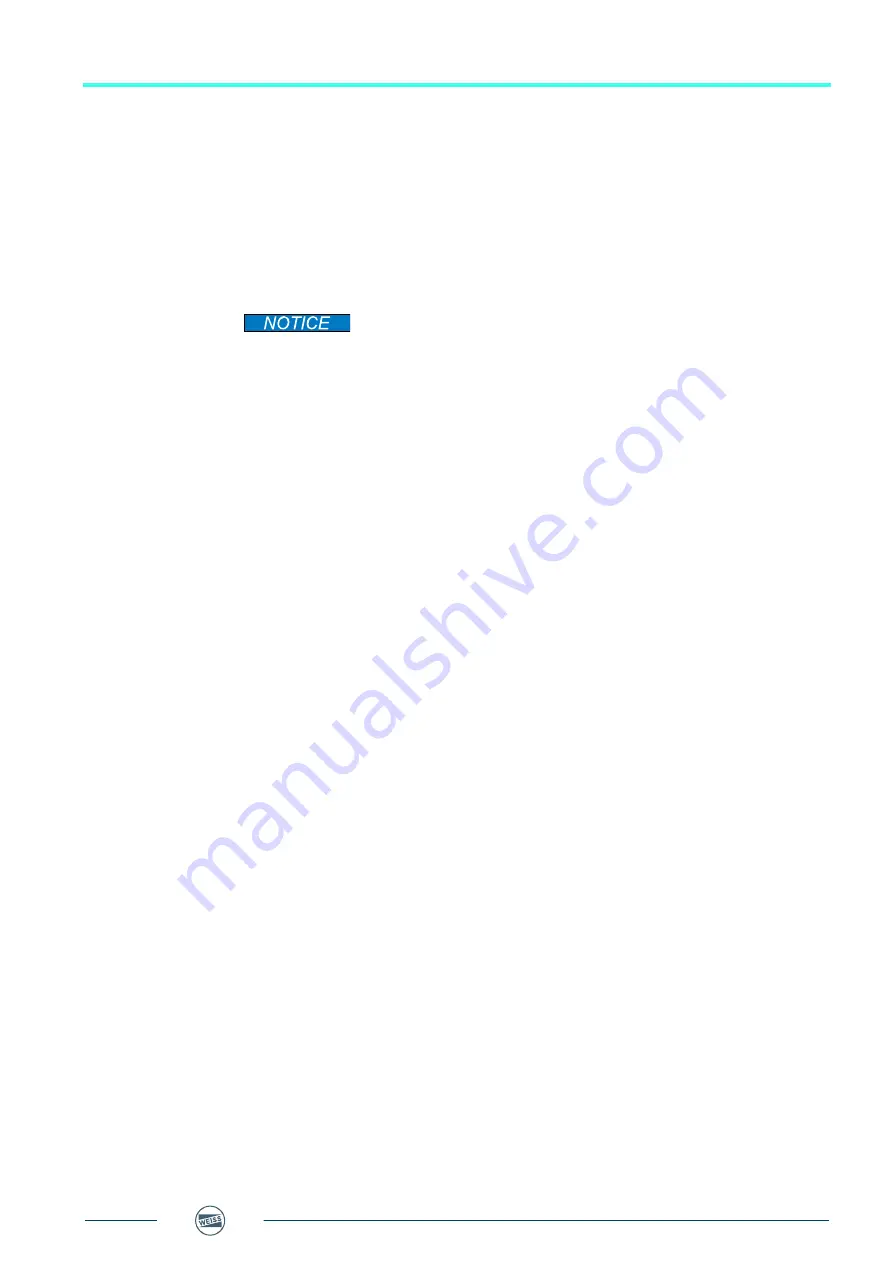
Pick-O-Mat • PM1100 / PM1500 • R02-2014
12/44
Product description
3.2 Function
3
3.2
Function
3.2.1
Complete module
The kinematics converts the rotation of a double curve driven by the central drive and
creates the horizontal and vertical movements of the handling modules.
A three-phase motor with attached closed-circuit brake (braked without voltage) drives
the double curve via a toothed belt segment and reduction gear.
The direction of rotation of the three-phase motor has to be clockwise
because the double curve is not symmetrical.
The rotating device on the PM1100 is a rotary indexing table and on the PM1500 it is a
ring rotary indexing table.
The motors of the central drive and the rotating device are synchronised electrically by a
position encoder placed on the control cam of the central drive.
The plate or the ring of the rotating device should cycle with the shortest possible switch
time (see combination indexing, moment of inertia and switch time in the brochure "Elec-
tro mechanical rotary indexing tables type TC-T" or "Ring rotary indexing tables TR").
The speed of the central drive can be adapted to the slowest part infeed.
The ratio short cycle time to long standstill time has the advantage that more time is
available for time intensive operations such as mounting, screwing or checking with the
same cycle time.
The insertion movements can be smooth and harmonic however, and ideally run without
stop.
If procedural stops due to faults become necessary, then the handling modules have to
be stopped in initial position (outside top).
3.2.2
Lift module
The lift module is intended to place a test head from above onto the part to be checked.
To avoid crash situations, this test head has to be equipped with a spring-borne follow-up
system that permits a maximum of 50 N spring force and at least 70 mm spring deflexion.
The lift module operates in parallel with the horizontal stroke of the insertion module.
The downwards movement of the lift module is done synchronously to the inward drive of
the insertion module.
This function mode is independent of the frame size.
The maximum mass to be moved is 1.5 kg.
Stroke dependencies, see chapter 3.5.6 „Strokes“ on page 15
3.2.3
Press module
The press module is intended to place a press head from above onto the part to be pres-
sed. To avoid crash situations, this press head has to be equipped with a spring-borne
follow-up system that permits a maximum of 300 N spring force and at least 51 mm
spring deflexion.
The press module operates in parallel with the horizontal stroke of the insertion module.
The downwards movement of the press module is done synchronously to the insertion
module.
This function mode is independent of the frame size.
The maximum pressing force is 200 N.
Stroke dependencies, see chapter 3.5.6 „Strokes“ on page 15