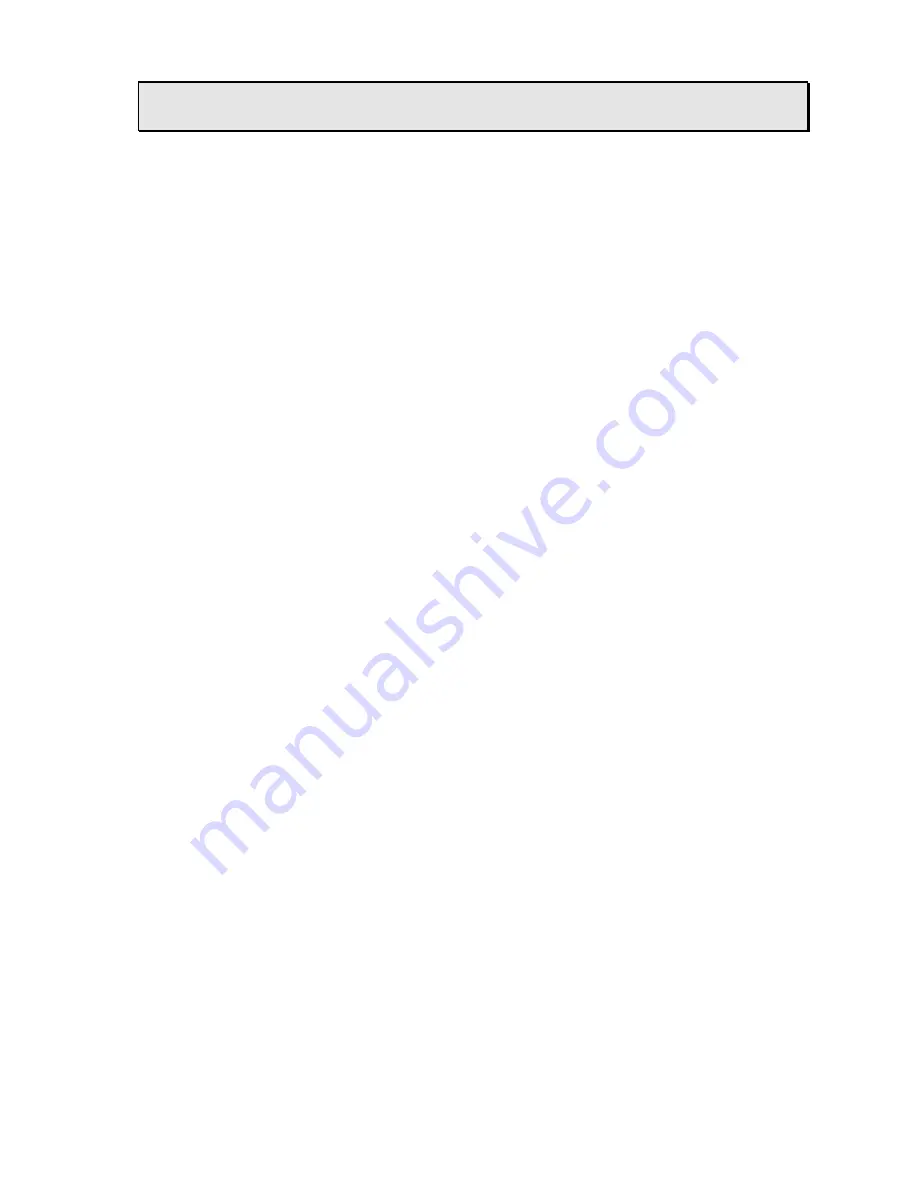
28
Repair & Maintenance
WARNING: Have a qualified electrician do the maintenance and trouble shooting work. Turn
the input power off, using the disconnect switch at the fuse box before working
inside the machine.
1. Attentions:
1
.
When problems such as abnormal cutting seam, arc-interruption, difficult arc-start
occurs, please check easy-worn-out consumables like nozzle or electrode and replace
them if they are bad consumption.
2
.
When assembly electrode ,gas diffuser, nozzle and nozzle cover, should aware of fitting
up coaxially, nozzle cover press the nozzle toughly.
3
.
While in cutting, avoid moving cutting torch too quickly in case burning out nozzle due
to arc flame rebounding from non-cut-through workpiece base as well as moving too
slow to influence cutting quality.
4
.
While in cutting, please keep air pressure in the range of 0.6 to 0.8Mpa. Let out
accumulated water in the compressed air filter timely.
5
.
The machine equipped with low-voltage protection. The machine will automatic stop
working when the input primary power is too low.
6
.
The machine equipped with overheat protection. The machine will automatic stop
working when the temperature inside the machine is very high and the protection lamp
on the front panel will light on.