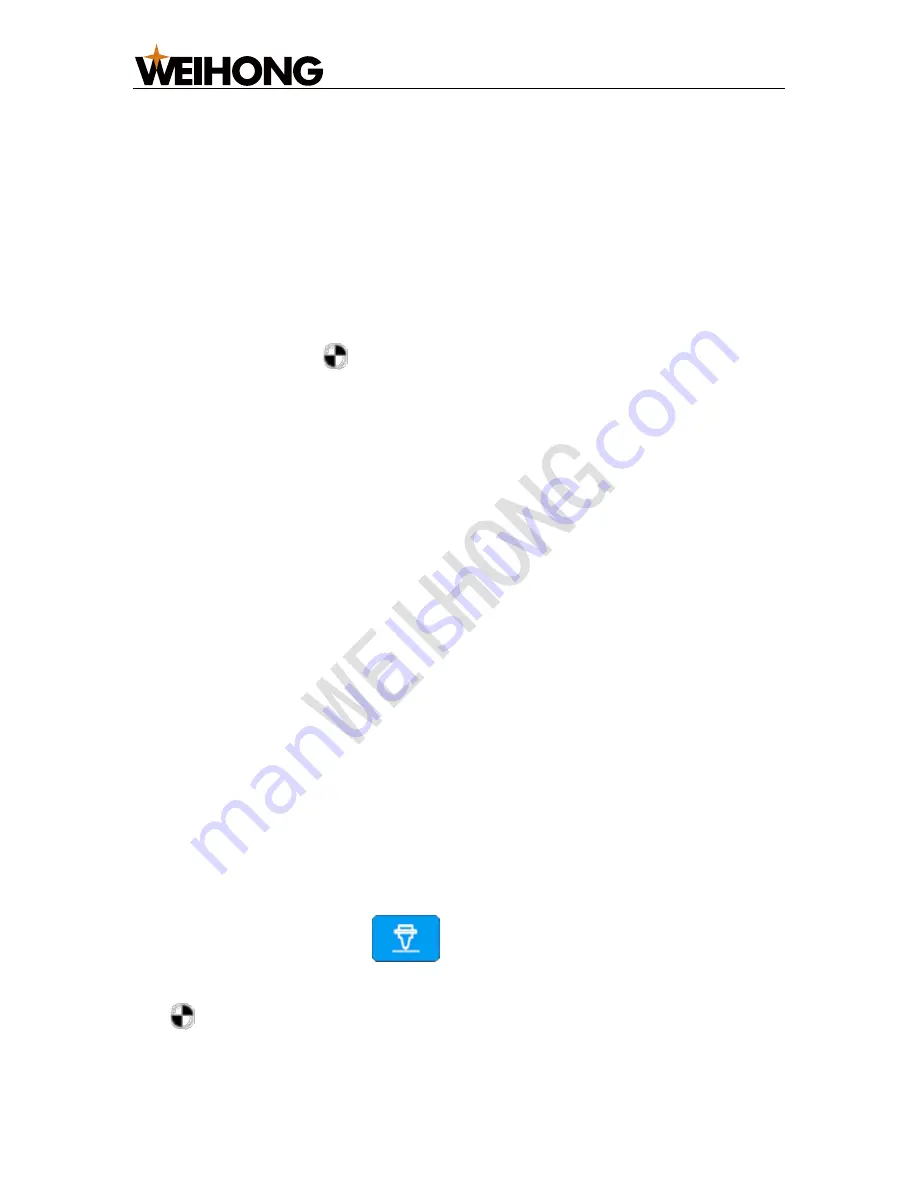
上海维宏电子科技股份有限公司
SHANGHAI WEIHONG ELECTRONIC TECHNOLOGY CO., LTD
30
/
53
2.
Press one of the following:
–
F1:
return X-axis to the machine origin.
–
F2:
return Y-axis to the machine origin.
–
F3:
return Z-axis to the machine origin.
–
F5:
return X-axis and Y-axis to the machine origin at the same time.
–
F8:
return all axes to the machine origin in order of Z-axis, X-axis and Y-
axis.
Note:
The system entitles Z-axis the highest priority in returning to the
machine origin by default. For safety, it is suggested to firstly return Z-axis.
After returning, the sign
appears in front of related axes in the coordinate
display area.
2.5.2
Set Datum with an Absolute Encoder
This operation is used to return to the machine origin with an absolute encoder by
directly setting datum at the first time to use the system.
Compared to returning to the machine origin with an incremental encoder, it owns
the following advantages:
•
No need to set returning orders for all axes in datum setting process.
•
No need to set datum again after restarting the system, and recovering from
power interruption and E-stop because the system will automatically read the
datum information.
Note:
You need to set datum again after replacing battery of the absolute encoder.
Before setting datum with an absolute encoder, do the following:
•
Check the motor nameplate and ensure the value of parameter
N11001
Encoder Type
is set to
1
.
•
Set the values of WISE drive parameter
Pr015
to
0
, and software parameter
Encoder Feedback
to
Yes
.
Taking X-axis as an example, to set datum with an absolute encoder, do the
following:
1.
Manually move X-axis to the fixed position of the machine tool.
2.
In
REF.Point
mode, press
→
1
→
F7
→
F1
.
The system reads and records X-axis machine coordinates automatically. And the
sign
appears in front of X-axis in the coordinate display area after setting datum
successfully.