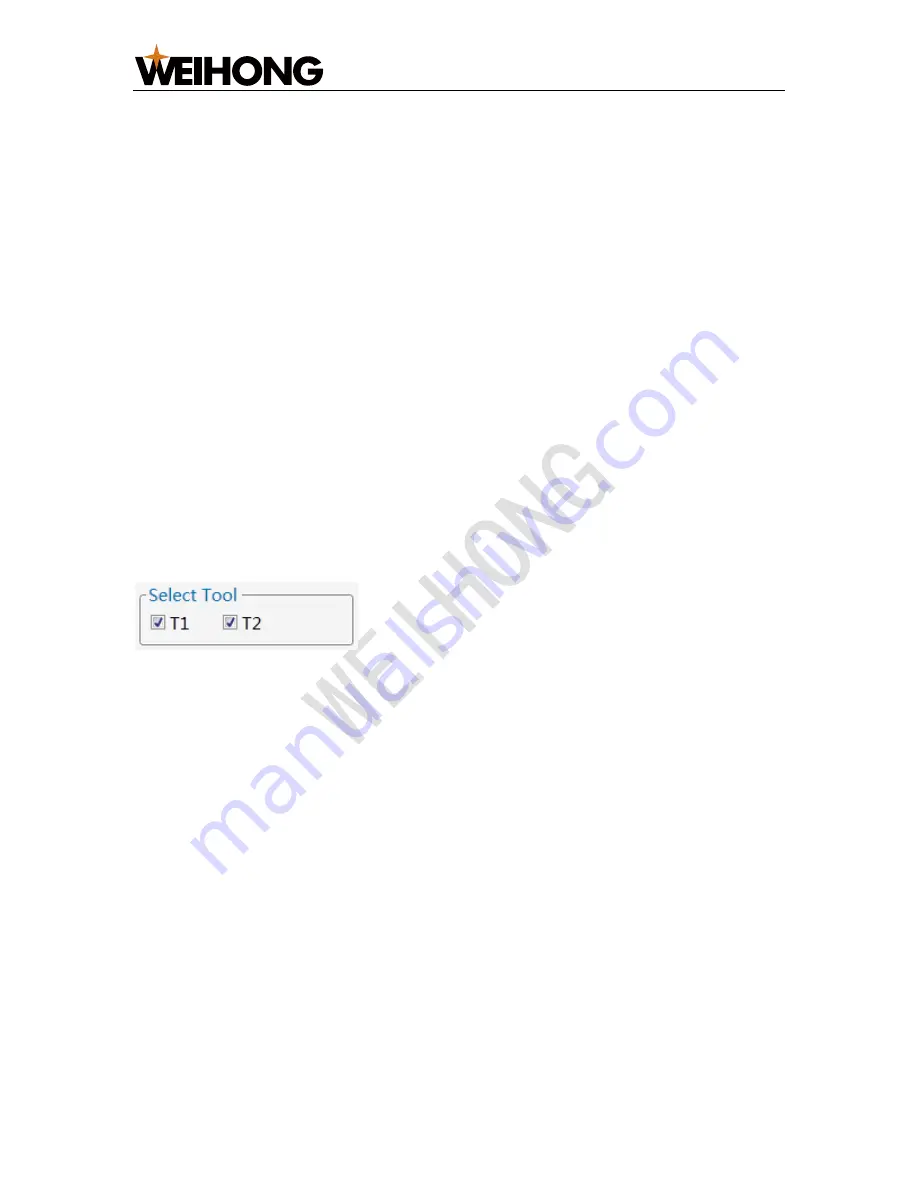
上海维宏电子科技股份有限公司
SHANGHAI WEIHONG ELECTRONIC TECHNOLOGY CO., LTD.
28
/
36
5
Special Operations
This section mainly introduces special operations in
Double-tool CNC System
.
Special operations mainly include the following:
•
•
•
•
•
5.1
Select the Tool(s)
This operation is used to choose the tool(s), which is convenient to execute
adjustment and use another tool to continue machining in case of something wrong
with one tool.
Before selecting the tool(s), set parameter
Min Distance between X1 and X2
and
Max Distance between X1 and X2
to protect tools from collision.
Select the tool(s) in tool selecting area in
Operator
interface or
Technician
interface.
Instruction
•
Select one tool
–
During manual movement, only the selected tool moves.
–
During automatic machining, the double tools move synchronously. The
unselected tool does not do cutting actions. And for safety, Z-axis does
not move.
•
Select double tools
–
During manual movement, the double tools move at the same time.
–
During automatic machining, the system synchronizes the workpiece
coordinates of the double tools and keeps synchronous cutting.