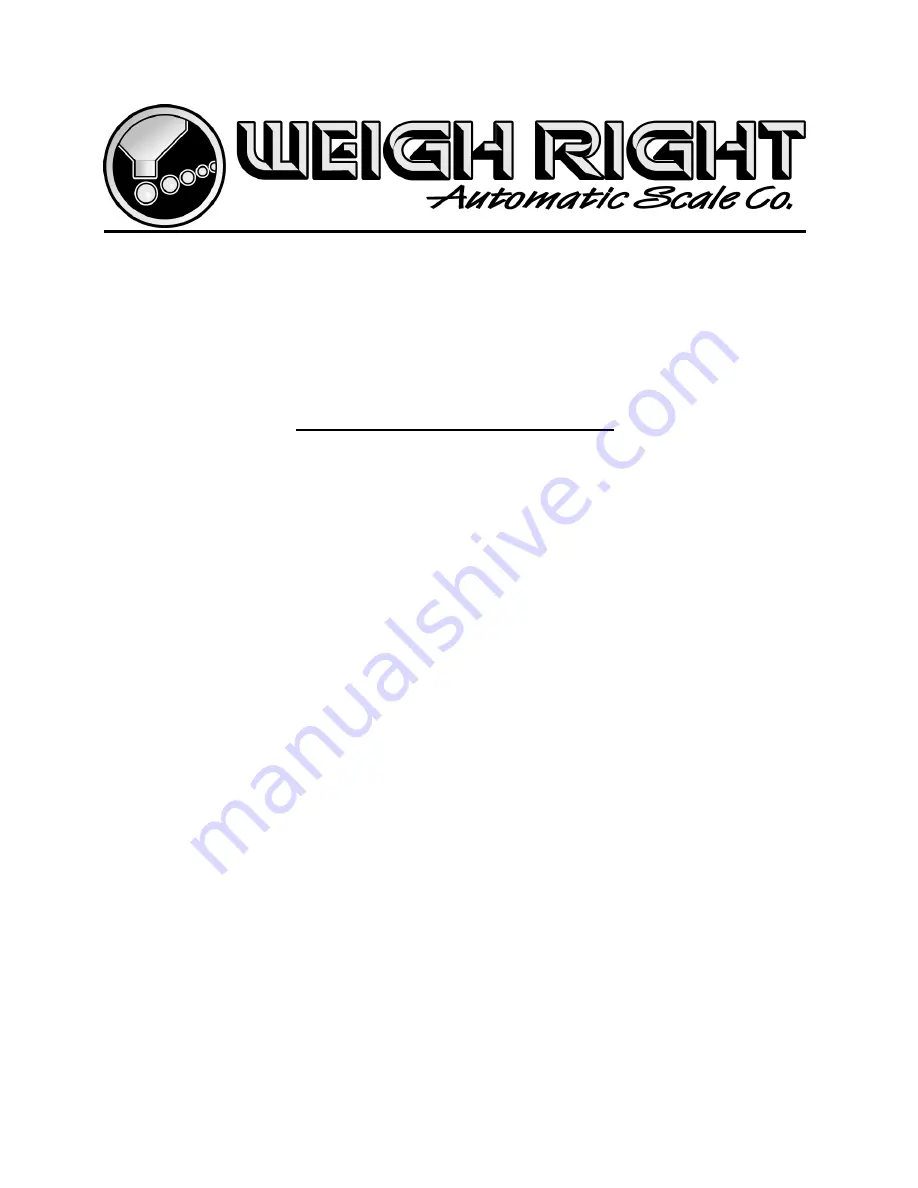
INSTRUCTION MANUAL
MODEL PMB 1 NET WEIGHER
Serial No. BDC-3601
PROTEIN TECHNOLOGIES
Manufacturer WEIGH RIGHT AUTOMATIC SCALE CO.
612A Mills Rd.
Joliet, IL 60433
Phone - 815/726-4626
Fax - 815/726-7638
www.weighrightasc.com
This manual serves as a guideline for operation, maintenance, trouble shooting and parts
replacement.
Содержание PMB 1
Страница 23: ......