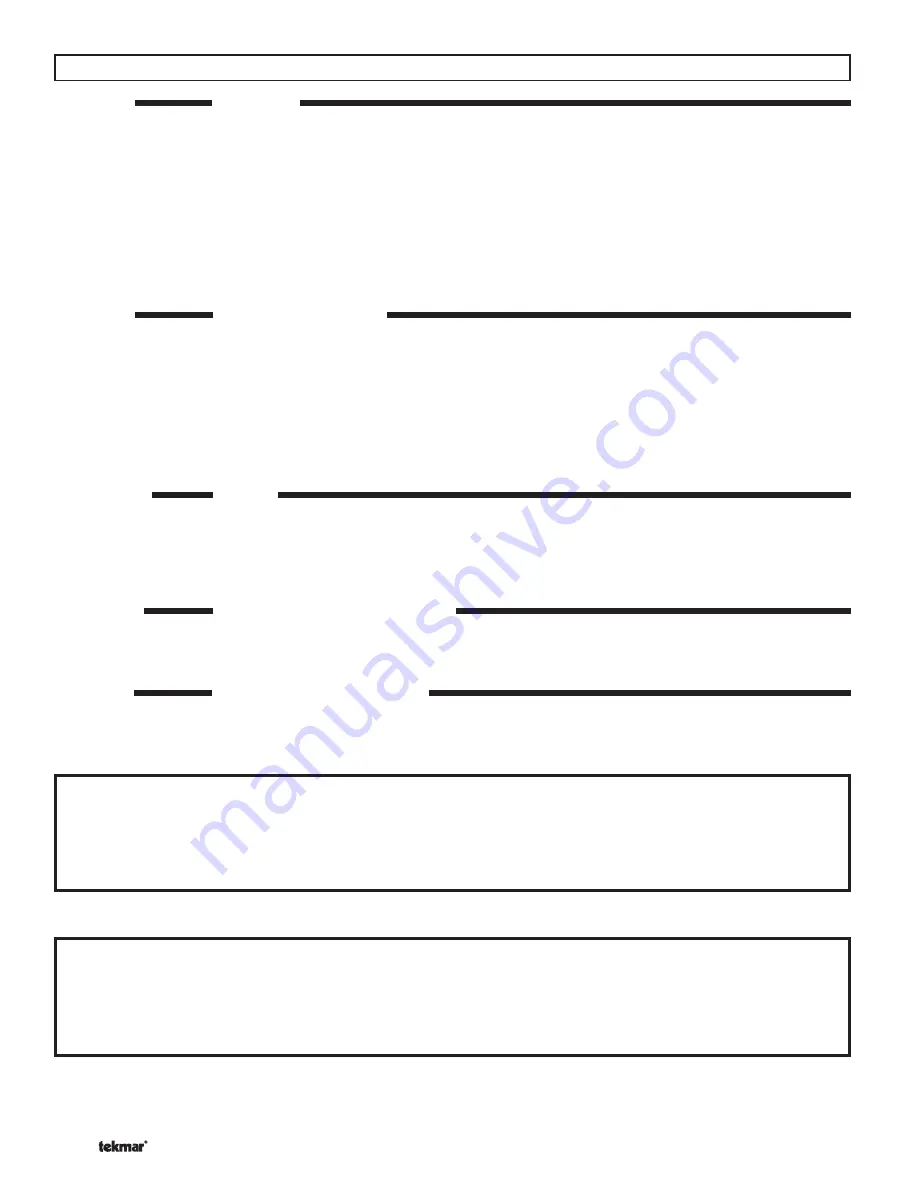
©
2005 D
704
-
04/05
4
of
16
STEP ONE
MOUNTING
1. Mounting position – The Mixing Station 704 must be mounted in the vertical position with the automatic air vent located at the top
of the Mixing Station 704.
2. To mount the Mixing Station 704 begin by removing the Radiant Mixing Control from the front of the Mixing Station 704. Remove
the screw and pull the Radiant Mixing Control straight forward. Ensure that the Radiant Mixing Control is stored in a safe place until
it is ready to be remounted.
3. Remove the three screws holding the blue plastic cover to the Mixing Station 704.
4. Select a suitable location to mount the Mixing Station 704 that allows suffi cient space for easy pipe connections.
5. Attach the sheet metal base to the wall with screws (not included) through the small mounting holes. See technical data for hole
location and spacing.
6. Using four suitable screws (not included), fasten the Mixing Station 704 to the selected location. Ensure that at least two of the
mounting screws are attached to a wall stud or similar surface.
STEP TWO
PIPING CONNECTIONS
1. Using proper piping practices, connect the supply to the radiant heating system to the Radiant Supply (bottom right hand connec-
tion) as indicated on the plastic cover of the Mixing Station 704. Ensure that a proper isolation valve is installed.
2. Using proper piping practices, connect the return from the radiant heating system to the Radiant Return (top right hand connection)
as indicated on the plastic cover of the Mixing Station 704. Ensure that a proper isolation valve is installed.
3. Using proper piping practices, connect the supply from the boiler loop to the Boiler Supply (top left hand connection) as indicated
on the plastic cover of the Mixing Station 704. Ensure that a proper isolation valve is installed.
4. Using proper piping practices, connect the return to the boiler loop to the Boiler Return (bottom left hand connection) as indicated
on the plastic cover of the Mixing Station 704. Ensure that a proper isolation valve is installed.
5. Connect the Boiler Supply and Boiler Return lines to the boiler loop using standard Primary Secondary piping practices.
STEP THREE
FILLING
1. Fill system with tap water – The system must be fi lled before operating the circulator. The bearings are water lubricated and should
not be allowed to operate dry. Filling the system will result in immediate lubrication of the bearings. It is always good practice to fl ush
a new system of foreign matter before starting the circulator.
2. Circulator operation – Operate the circulators for 5 minutes immediately after fi lling system to purge remaining air from the bearing
chamber. This is especially important when installing the circulator during the off-season.
STEP FOUR
REPLACING THE FRONT COVER
1. Place the blue plastic cover over the Mixing Station 704.
2. Using the original three screws, fasten the blue plastic cover to the Mixing Station 704.
3. Reinstall the Radiant Mixing Control and fasten it in place with the remaining original screw. RMC wiring starts on page 9.
STEP FIVE
ELECTRICAL CONNECTIONS
1. Electrical connections – Observe all applicable codes when connecting to power supply. The motors are impedance protected, and
do not require overload protection. The pumps cannot run backwards.
CAUTION:
1. The addition of petroleum based fl uids or certain chemical additives to systems utilizing TACO equipment voids the
warranty.
2. Use supply wires suitable for 194°F (90°C) – ATTENTION: Employer des fi ls d´alimentation adequats pour 194°F (90°C).
WARNING:
To avoid electrical shock, disconnect the power supply to the circulator and the main electrical unit.
WARNING:
Do not use in swimming pool or spa areas; pump has not been investigated for this application.
WARNING:
In the event the retaining screws have been pulled out of the housing, DO NOT replace them. Use of any other screw
may short out the stator windings, creating a risk of electrical shock.
Installation of the Mixing Station 704