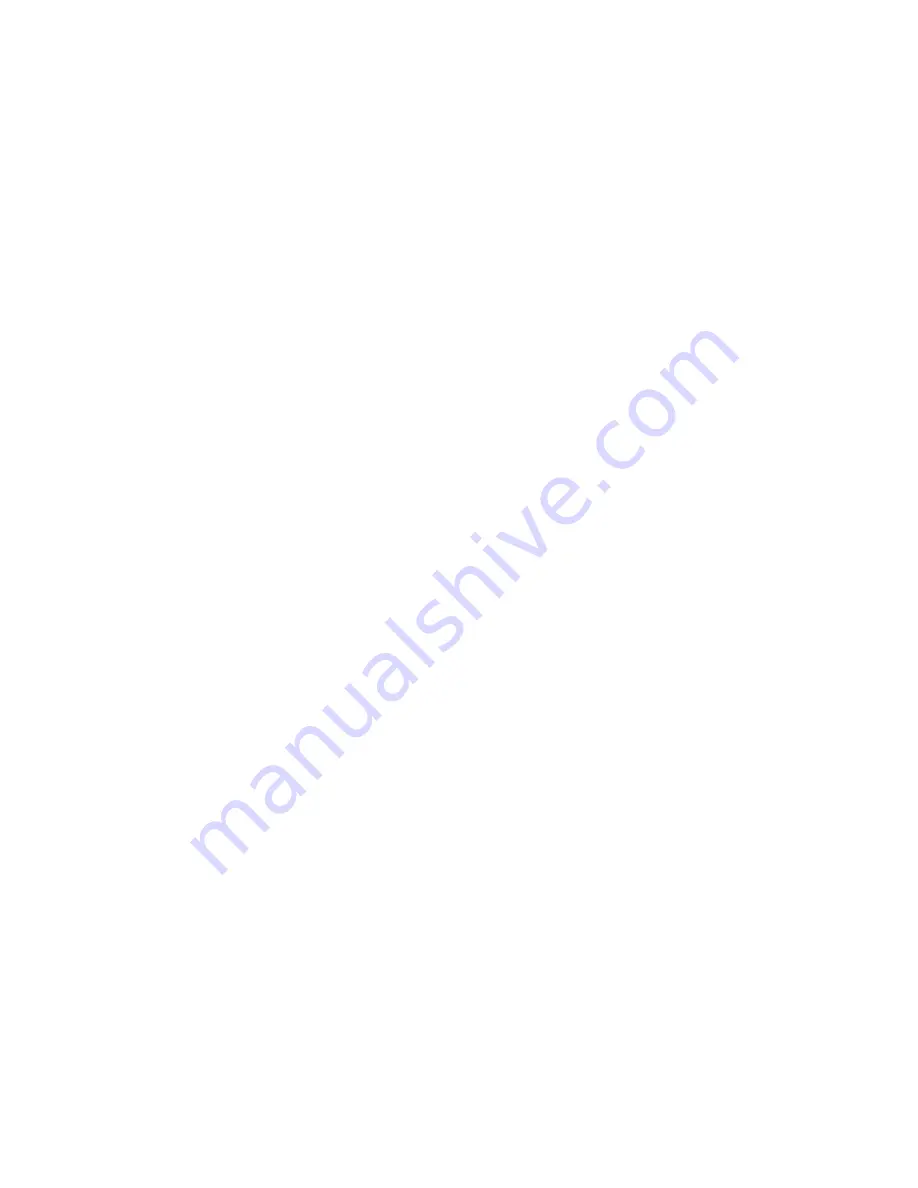
5
General and Commercial
Installation Checklist
1 . Place the softener tanks where you want to install the unit .
NOTE: Be sure the tanks are level and on a firm base.
2 . During cold weather it is recommended that the installer warm
the valve to room temperature before operating .
3 . Perform all plumbing according to local plumbing codes .
— Use a 1/2" minimum pipe size for the drain .
— Use a 3/4" drain line for backwash flow rates that exceed 7
gpm or length that exceeds 20' (6 m) .
4 . Both tanks must be the same height and diameter and filled with
equal amounts of media .*
5 . The distributor tube must be flush with the top of each tank . Cut
if necessary . Use only non-aerosol silicone lubricant .*
6 . Lubricate the distributor O-ring seal and tank O-ring seal . Place
the main control valve on one tank and the tank adapter on the
second tank .*
NOTE: If required, solder copper tubing for tank intercon-
nection before assembling on the main control valve and
tank adapter. Maintain a minimum of 1" distance between
tanks on final assembly.
7 . Solder joints near the drain must be done before connecting
the Drain Line Flow Control fitting (DLFC) . Leave at least 6" (152
mm) between the DLFC and solder joints when soldering pipes
that are connected on the DLFC . Failure to do this could cause
interior damage to DLFC .
8 . Use only Teflon
®
tape on the drain fitting .
9 . Be sure the floor under the salt storage tank is clean, level, and
strong enough to support the system . .
10 . Place approximately 1" (25 mm) of water above the grid plate . If
a grid is not utilized, fill to the top of the air check in the salt tank .
Do not add salt to the brine tank at this time .
11 . Place the system in Bypass .
— Turn on the main water supply .
— Open a cold soft water tap nearby and let water run a few
minutes or until the system is free of foreign material (usually
solder) resulting from the installation .
12 . Place the bypass In Service position and let water flow into the
mineral tank .
Electrical
13 . Make all electrical connections according to codes . Plug the
valve into an approved power source . Do not insert meter cable
into the meter yet .
14 . Tank one has control valve and tank two has adapter . See Figure
1, page 4 .
15 . Look on the right side of the control valve, it has indicators
showing which position the control valve is in during Regenera-
tion and which tank is In Service .
— Figure 3, page 6 shows the valve In Service position with tank
one supplying conditioned water and tank two on standby .
NOTE: Make sure the meter cable is not inserted in the me-
ter dome. Swing the timer out to expose the program wheel.
To swing timer out, grab onto the lower right corner of timer
face and pull outward. See Figure 5, page 7.
* Tanks 12" in diameter and smaller are factory loaded with me-
dia. Checking media amounts, distributor tube length, lubricat-
ing the distributor pilot O-rings, and lubricating the tank seal
O-rings on these sized systems is not necessary.
Teflon
®
is a registered trademark of E .I . Dupont de Nemours & Company .
Содержание PWSYS-WH-SOFT-TA series
Страница 13: ...13 Model 9000 9100 9500 24 9000 9100 9500 Power Head Figure 22 9100 Electro Power Head...
Страница 15: ...15 Model 9000 9100 9500 9100 Control Valve Assembly Figure 24 9100 Control Valve Assembly...
Страница 18: ...18 Figure 31 9000 9100 9500 Meter Assemblies 9100 Meter Assembly...
Страница 23: ...23 Model 9000 9100 9500 41 Backwash Brine Draw Figure 40 Backwash Position Figure 41 Brine Draw...
Страница 24: ...24 Model 9000 9100 9500 42 Slow Rinse Rapid Rinse Figure 42 Slow Rinse Figure 43 Rapid Rinse...
Страница 29: ...29 Model 9000 9100 9500 50 9100 Control Dimensions Figure 50...
Страница 30: ...30 Model 9000 9100 9500 53 9100 9500 Figure 53 9100 Meter Flow Data Figure 54 9500 Meter Flow Data...