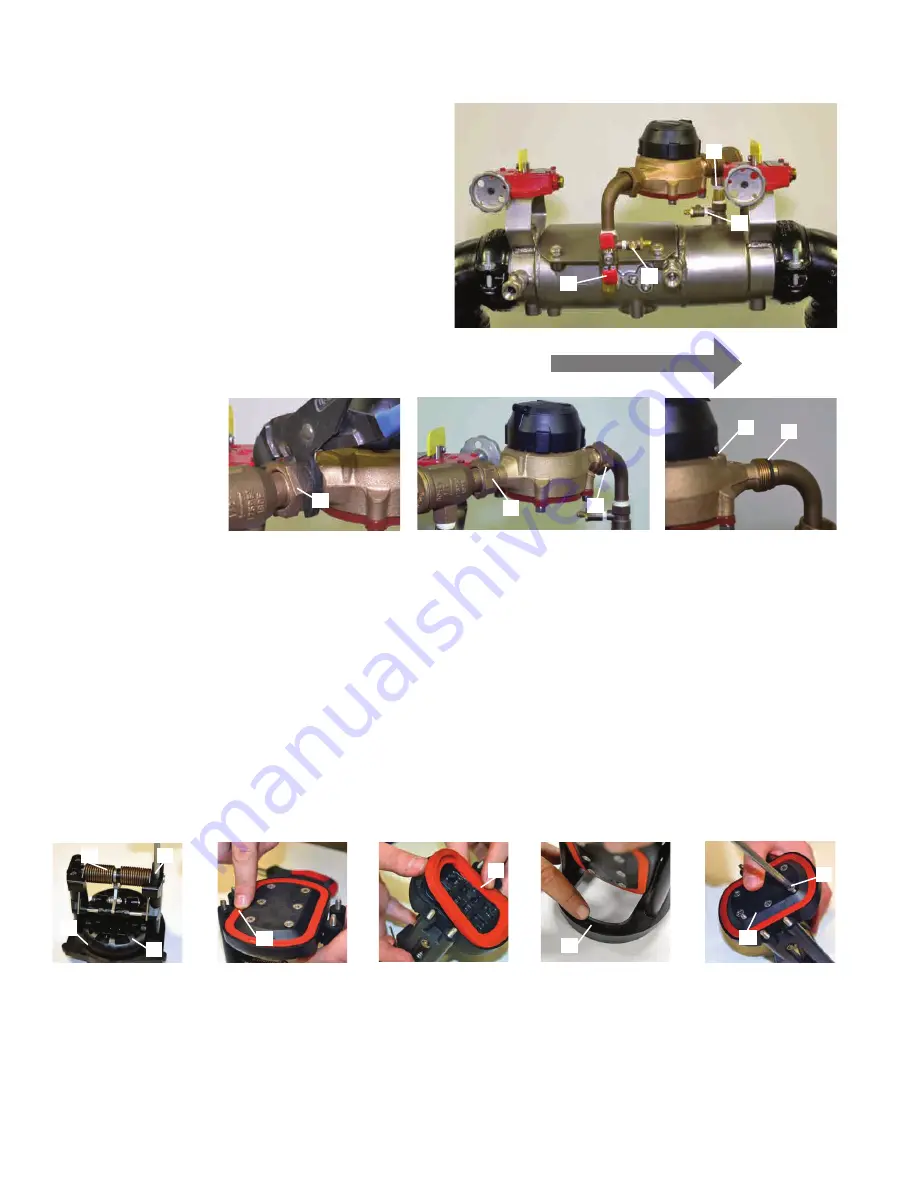
6
IOM-A-Deringer 20/30_2.5-4
2005
EDP#2916002
© 2020 Watts
Deringer 30: Removing Bypass Meter
1. Using the ball valve handles close the #2 bypass ball valve
(A) and then #1 bypass ball valve (B). (Ball valve is closed
when “T” handle is perpendicular to water flow through
ball valve).
2. Using a #2 flat head screw driver open bypass test cock
#2 (C) and then open bypass test cock #1 (D). (Test cock is
open when screw driver slot is parallel to water flow through
test cock).
3. Using large adjustable pliers or a wrench, unscrew and
retract bypass meter coupling nuts (E) . Remove the
gaskets (F) on both sides of bypass meter.
4. Gently remove bypass meter (G) from line. It is OK if the
bypass fittings move slightly during the removal process.
5. Reverse order of above instructions to reinstall bypass
meter. Remember to install gaskets (F) before threading
meter coupling nuts into place.
B
C
E
E
G
F
E
FLOW
D
A
Maintenance of First Dual-action Check Module
1. Use a #2 phillips head screwdriver to remove tower
screws (A) from the first check seat (B) the double
torsion spring is captured (C) and does not to be retained
during maintenance.
2. After removing the tower screws (A) examine the elastomer
disk (D) and check seat (E) for fouling or damage.
3. Should elastomer disk (D) need replacement unscrew disk
retainer screws (F) and remove disk retainer (G). Carefully
remove and replace elastomer disk (D). When replacing
elastomer disk (D) be certain that no air, water or debris is
trapped in the clapper (H) cavity behind the elastomer disk (D).
4. Reverse the order of the above instructions to reassemble
check.
• Elastomer disk must be flat in clapper (H) cavity before
tightening disk retainer screws (F).
• Do not cross thread disk retaining screws (F).
F
G
E
D
D
H
B
C
A