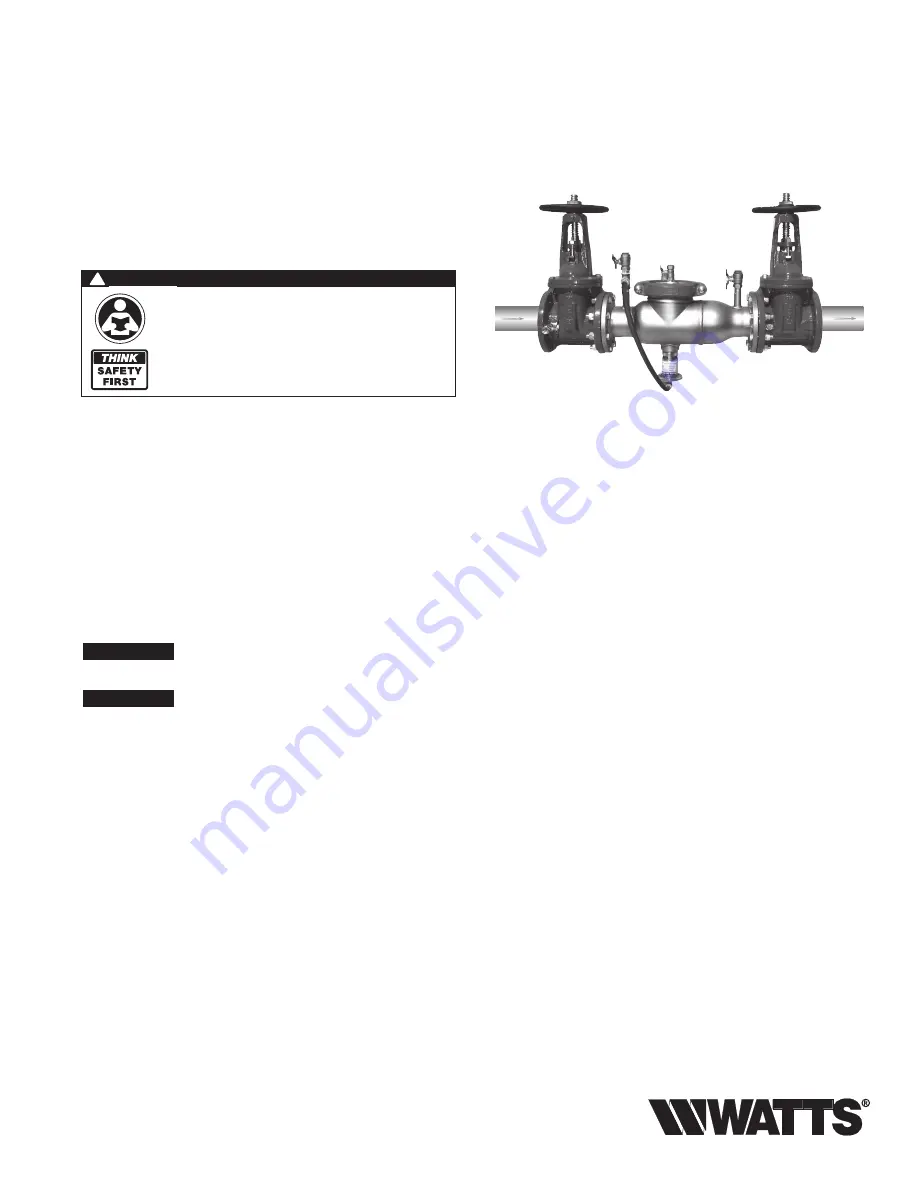
RP/IS-994/994RPDA
NOTICE
Inquire with governing authorities for local installation requirements
NOTICE
For Australia and New Zealand: Pipeline strainers should be installed
between the upstream shutoff valve and the inlet of the backflow
preventer.
994
Installation, Maintenance, & Repair
Series 994/994RPDA
Reduced Pressure Zone Assemblies
Reduced Pressure Detector Assemblies
Sizes: 2
1
⁄
2
" – 10" (65 – 250mm)
Local building or plumbing codes may require modifications to the
information provided. You are required to consult the local building and
plumbing codes prior to installation. If this information is not consistent
with local building or plumbing codes, the local codes should be fol-
lowed.
Need for Periodic Inspection/Maintenance:
This product must be
tested periodically in compliance with local codes, but at least once per
year or more as service conditions warrant. Corrosive water conditions,
and/or unauthorized adjustments or repair could render the product
ineffective for the service intended. Regular checking and cleaning of the
product’s internal components helps assure maximum life and proper
product function.
WARNING
!
Read this Manual BEFORE using this equipment.
Failure to read and follow all safety and use information
can result in death, serious personal injury, property
damage, or damage to the equipment.
Keep this Manual for future reference.
Testing
For field testing procedure, refer to Watts installation sheets
IS-TK-DP/DL, IS-TK-9A, IS-TK-99E and IS-TK-99D found on
www.watts.com.
For troubleshooting guide, refer to literature S-TSG.
For other repair kits and service parts, refer to our Backflow Preven-
tion Products Repair Kits & Service Parts price list PL-RP-BPD
found on
www.watts.com.
For technical assistance, contact your local Watts representative.