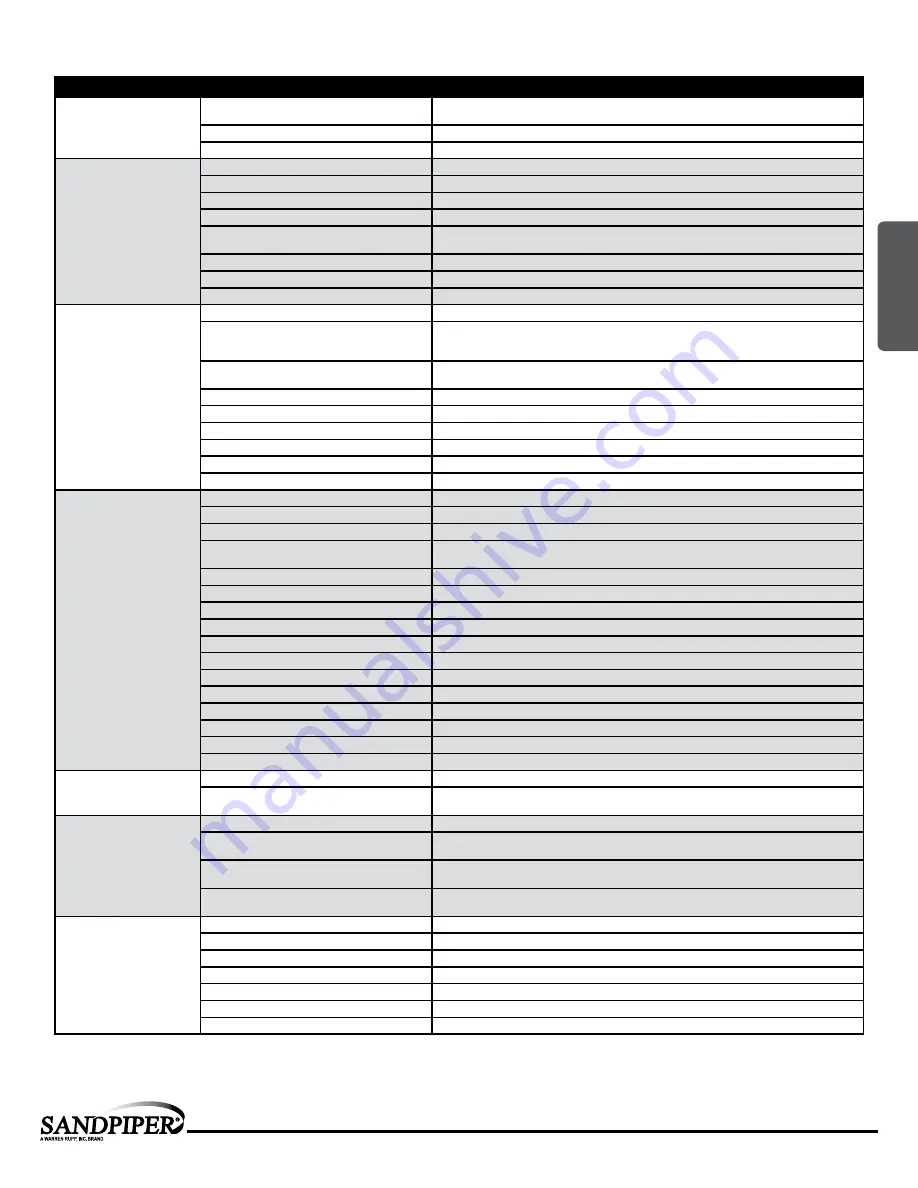
f15mdl1sm-rev0219
sandpiperpump
.
com
Model F15 Metallic •
11
Recommended Installation Guide
Troubleshooting Guide
For additional troubleshooting tips contact After Sales Support at [email protected] or 419-524-8388
Symptom:
Potential Cause(s):
Recommendation(s):
Pump Cycles Once
Deadhead (system pressure meets or exceeds air
supply pressure) .
Increase the inlet air pressure to the pump. Pump is designed for 1:1 pressure ratio at zero flow.
(Does not apply to high pressure 2:1 units) .
Air valve or intermediate gaskets installed incorrectly . Install gaskets with holes properly aligned .
Bent or missing actuator plunger .
Remove pilot valve and inspect actuator plungers .
Pump Will Not Operate
/ Cycle
Pump is over lubricated .
Set lubricator on lowest possible setting or remove . Units are designed for lube free operation .
Lack of air (line size, PSI, CFM) .
Check the air line size and length, compressor capacity (HP vs . CFM required) .
Check air distribution system .
Disassemble and inspect main air distribution valve, pilot valve and pilot valve actuators .
Discharge line is blocked or clogged manifolds .
Check for inadvertently closed discharge line valves . Clean discharge manifolds/piping .
Deadhead (system pressure meets or exceeds air
supply pressure) .
Increase the inlet air pressure to the pump. Pump is designed for 1:1 pressure ratio at zero flow.
(Does not apply to high pressure 2:1 units) .
Blocked air exhaust muffler.
Remove muffler screen, clean or de-ice, and re-install.
Pumped fluid in air exhaust muffler.
Disassemble pump chambers . Inspect for diaphragm rupture or loose diaphragm plate assembly .
Pump chamber is blocked .
Disassemble and inspect wetted chambers. Remove or flush any obstructions.
Pump Cycles and Will
Not Prime or No Flow
Cavitation on suction side .
Check suction condition (move pump closer to product) .
Check valve obstructed . Valve ball(s) not seating
properly or sticking .
Disassemble the wet end of the pump and manually dislodge obstruction in the check valve pocket .
Clean out around valve ball cage and valve seat area . Replace valve ball or valve seat if damaged .
Use heavier valve ball material .
Valve ball(s) missing (pushed into chamber or
manifold) .
Worn valve ball or valve seat. Worn fingers in valve ball cage (replace part). Check Chemical
Resistance Guide for compatibility .
Valve ball(s) / seat(s) damaged or attacked by product . Check Chemical Resistance Guide for compatibility .
Check valve and/or seat is worn or needs adjusting .
Inspect check valves and seats for wear and proper setting . Replace if necessary .
Suction line is blocked .
Remove or flush obstruction. Check and clear all suction screens or strainers.
Excessive suction lift .
For lifts exceeding 20’ of liquid, filling the chambers with liquid will prime the pump in most cases.
Suction side air leakage or air in product .
Visually inspect all suction-side gaskets and pipe connections .
Pumped fluid in air exhaust muffler.
Disassemble pump chambers . Inspect for diaphragm rupture or loose diaphragm plate assembly .
Pump Cycles Running
Sluggish / Stalling,
Flow Unsatisfactory
Over lubrication .
Set lubricator on lowest possible setting or remove . Units are designed for lube free operation .
Icing .
Remove muffler screen, de-ice, and re-install. Install a point of use air drier.
Clogged manifolds .
Clean manifolds to allow proper air flow.
Deadhead (system pressure meets or exceeds air
supply pressure) .
Increase the inlet air pressure to the pump. Pump is designed for 1:1 pressure ratio at zero flow.
(Does not apply to high pressure 2:1 units) .
Cavitation on suction side .
Check suction (move pump closer to product) .
Lack of air (line size, PSI, CFM) .
Check the air line size, length, compressor capacity .
Excessive suction lift .
For lifts exceeding 20’ of liquid, filling the chambers with liquid will prime the pump in most cases.
Air supply pressure or volume exceeds system hd .
Decrease inlet air (press. and vol.) to the pump. Pump is cavitating the fluid by fast cycling.
Undersized suction line .
Meet or exceed pump connections .
Restrictive or undersized air line .
Install a larger air line and connection .
Suction side air leakage or air in product .
Visually inspect all suction-side gaskets and pipe connections .
Suction line is blocked .
Remove or flush obstruction. Check and clear all suction screens or strainers.
Pumped fluid in air exhaust muffler.
Disassemble pump chambers . Inspect for diaphragm rupture or loose diaphragm plate assembly .
Check valve obstructed .
Disassemble the wet end of the pump and manually dislodge obstruction in the check valve pocket .
Check valve and/or seat is worn or needs adjusting .
Inspect check valves and seats for wear and proper setting . Replace if necessary .
Entrained air or vapor lock in chamber(s) .
Purge chambers through tapped chamber vent plugs . Purging the chambers of air can be dangerous .
Product Leaking
Through Exhaust
Diaphragm failure, or diaphragm plates loose .
Replace diaphragms, check for damage and ensure diaphragm plates are tight .
Diaphragm stretched around center hole or bolt holes . Check for excessive inlet pressure or air pressure . Consult Chemical Resistance Chart for compatibility
with products, cleaners, temperature limitations and lubrication .
Premature Diaphragm
Failure
Cavitation .
Enlarge pipe diameter on suction side of pump .
Excessive flooded suction pressure.
Move pump closer to product . Raise pump/place pump on top of tank to reduce inlet pressure .
Install Back pressure device (Tech bulletin 41r) . Add accumulation tank or pulsation dampener .
Misapplication (chemical/physical incompatibility) .
Consult Chemical Resistance Chart for compatibility with products, cleaners, temperature limitations
and lubrication .
Incorrect diaphragm plates or plates on backwards,
installed incorrectly or worn .
Check Operating Manual to check for correct part and installation . Ensure outer plates have not been
worn to a sharp edge .
Unbalanced Cycling
Excessive suction lift .
For lifts exceeding 20’ of liquid, filling the chambers with liquid will prime the pump in most cases.
Undersized suction line .
Meet or exceed pump connections .
Pumped fluid in air exhaust muffler.
Disassemble pump chambers . Inspect for diaphragm rupture or loose diaphragm plate assembly .
Suction side air leakage or air in product .
Visually inspect all suction-side gaskets and pipe connections .
Check valve obstructed .
Disassemble the wet end of the pump and manually dislodge obstruction in the check valve pocket .
Check valve and/or seat is worn or needs adjusting .
Inspect check valves and seats for wear and proper setting . Replace if necessary .
Entrained air or vapor lock in chamber(s) .
Purge chambers through tapped chamber vent plugs .
2: INST
AL
& OP