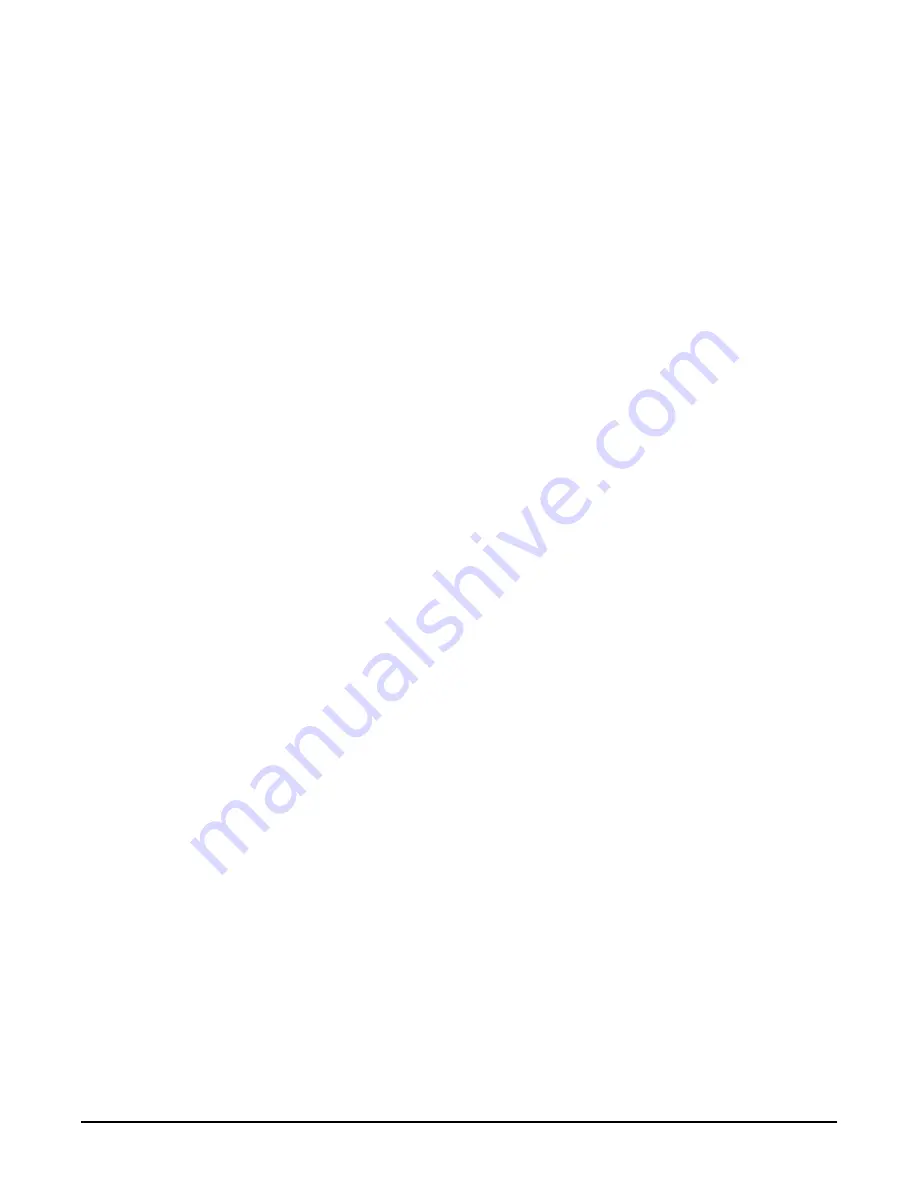
hdb3dl3sm-rev0611
Model HDB3/HDB4 Page 7
AIR EXHAUST
If a diaphragm fails, the pumped liquid or fumes can enter the air end of the pump,
and be exhausted into the atmosphere. When pumping hazardous or toxic materials,
pipe the exhaust to an appropriate area for safe disposition.
This pump can be submerged if materials of construction are compatible with the
liquid. The air exhaust must be piped above the liquid level. Piping used for the air
exhaust must not be smaller than 1" (2.54 cm). Reducing the pipe size will restrict
air flow and reduce pump performance .When the product source is at a higher level
than the pump (flooded suction), pipe the exhaust higher than the product source to
prevent siphoning spills.
Freezing or icing-up of the air exhaust can occur under certain temperature and
humidity conditions. Use of an air dryer unit should eliminate most icing problems.
BETWEEN USES
When used for materials that tend to settle out or transform to solid form, the pump
should be completely flushed after each use, to prevent damage. Product remaining
in the pump between uses could dry out or settle out. This could cause problems
with valves and diaphragms at re-start. In freezing temperatures, the pump must be
drained between uses in all cases.
CHECK VALVE SERVICING
For best priming and most efficient pumping performance, it is important to maintain
check valves and valve seats in good condition for proper sealing. Need for inspection
or service of ball valves is usually indicated by poor priming, unstable cycling, reduced
performance, or pump cycles but will not pump.
Inspection and service of check valves requires the removal of five hex nuts and
one capscrew for each set of check valves (i.e., suction & discharge), providing
access to the two ball valves and their valve seats. New ball valves are 3
5
/
8
" (9.21 cm)
in diameter and will require replacement when worn to approximately 3
3
/
8
" (8.57 cm)
diameter.
DIAPHRAGM SERVICING
Need for inspection or service of diaphragm is usually indicated when unit pumps
from one chamber only and air is discharged out pump discharge port or when liquid
being pumped is discharged through air exhaust port.
To service diaphragms remove two capscrews which secure the chamber to the
manifold assembly, and twelve hex nuts that secure the chamber to the main pump
assembly. To remove diaphragms, loosen diaphragm assembly by turning it out of the
diaphragm rod using a 1
1
/
8
" (2.857 cm) socket or wrench. Removal of opposite outer
chamber will permit removal of second diaphragm assembly and diaphragm rod as a
unit.
To remove the diaphragm from the diaphragm assembly, hold the diaphragm rod in
a clamping device, making sure to protect the rod surface of shaft so as not to scratch
or mar it in any way. With a wrench turn the diaphragm assembly out of the diaphragm
rod. To disassemble the components, turn a 5/16-18 UNC capscrew by hand into the
tapped hole in the inner diaphragm plate. This will keep the plate from turning while
the capscrew is removed. To remove the capscrew, place the assembly in a vise so
the two protruding ends of screws are loose in the vise jaws (approximately 7/8" apart).
Turn the center screw loose from the back plate and the assembly will come apart.
SANDPIPER® is a registered tradename of Warren Rupp, Inc.
Содержание HDB3
Страница 2: ......