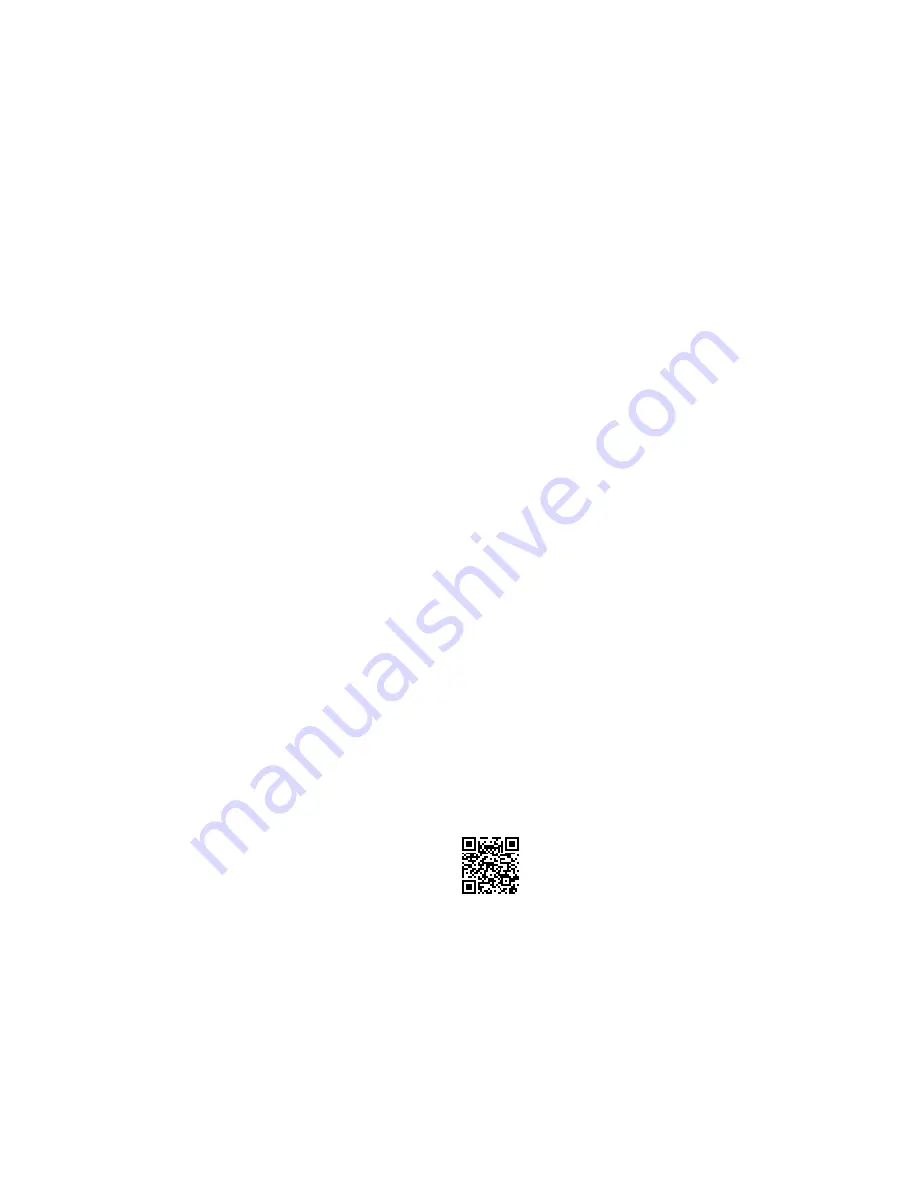
10
Warner Electric • 800-825-9050
P-273-5-WE • 819-0529
The following procedure describes how to set the
adjustable power supply to the optimum release
point of the brake . A volt-meter is required to perform
the procedure .
No power is applied to motor during this
procedure. Power normally supplied by motor
to brake control should be supplied by alternate
method.
1 . With power off, connect the positive (red) lead
of the power supply to the positive (black) lead
of the brake and the negative lead of the power
supply to the negative lead of the brake .
2 . Connect a volt-meter to measure the voltage
applied across the brake .
3 . Adjust the power supply to its lowest possible
output, and then energize the power supply to
apply power to the brake only .
4 . Starting from the low voltage point, slowly
increase the applied voltage while visually
watching the brake armature through one of
the vent slots and fan slot on either side of the
module until the brake armature disengages from
the brake magnet . Note and record this voltage
reading .
5 . Add twenty (20) volts for a 90 volt brake and five
(5) volts for a 24 volt brake to this reading and
set the supply to this level . This will be the proper
release voltage for your setup .
6 . With the brake energized, spin the output shaft
by hand to insure that it turns freely . If a scraping
sound is noted when the output shaft is spun,
it means an armature is dragging slightly . This
needs to be corrected by readjusting the airgap
per Section C and/or repeating brake release
adjustment steps 1-5 above .
Note:
If you have a clutch/FB brake, the clutch
armature airgap should be adjusted at this time per
section C . The brake must be energized/released
during the clutch airgap adjustment so the output
shaft can be rotated by hand .
Section K: Burnishing
Intimate metal to metal contact is essential between
the armature and the metal rings (poles) of the
magnet or rotor . Warner Electric clutches and brakes
leave the factory with the friction material slightly
undercut to assure good initial contact .
Normally, the desired wearing-in process occurs
naturally as the surfaces slip upon engagement . The
time for wear-in, which is necessary to obtain the
ultimate torque of the unit, will vary depending on
speed, load, and duty cycle .
If maximum torque is required immediately after
installation, the unit should be burnished by slipping
the friction surfaces together at reduced voltage . It is
recommended that the burnishing be done right on
the application, if at all possible .
Burnishing at high speed will result in a smoother
wear-in pattern and reduce the time for burnishing .
The voltage should be set at approximately 30% or
40% of the rated value .
The unit should be cycled on and off to allow
sufficient time between slip cycles to prevent
overheating .
When a Warner Electric brake or clutch is properly
assembled and installed, no further servicing,
lubrication, or maintenance should be required
throughout the life of the unit .
Troubleshooting - Electrical
Scan to Watch Clutch & Brake
Electrical Troubleshooting Video
https://p.widencdn.net/byvbde
A module that is not functioning properly may be
caused by other problems . It is best to check for
these problems before replacing it .
A standard Electro-Module clutch or brake requires
DC power to function . If power is not reaching the
clutch or brake, they will not disengage .