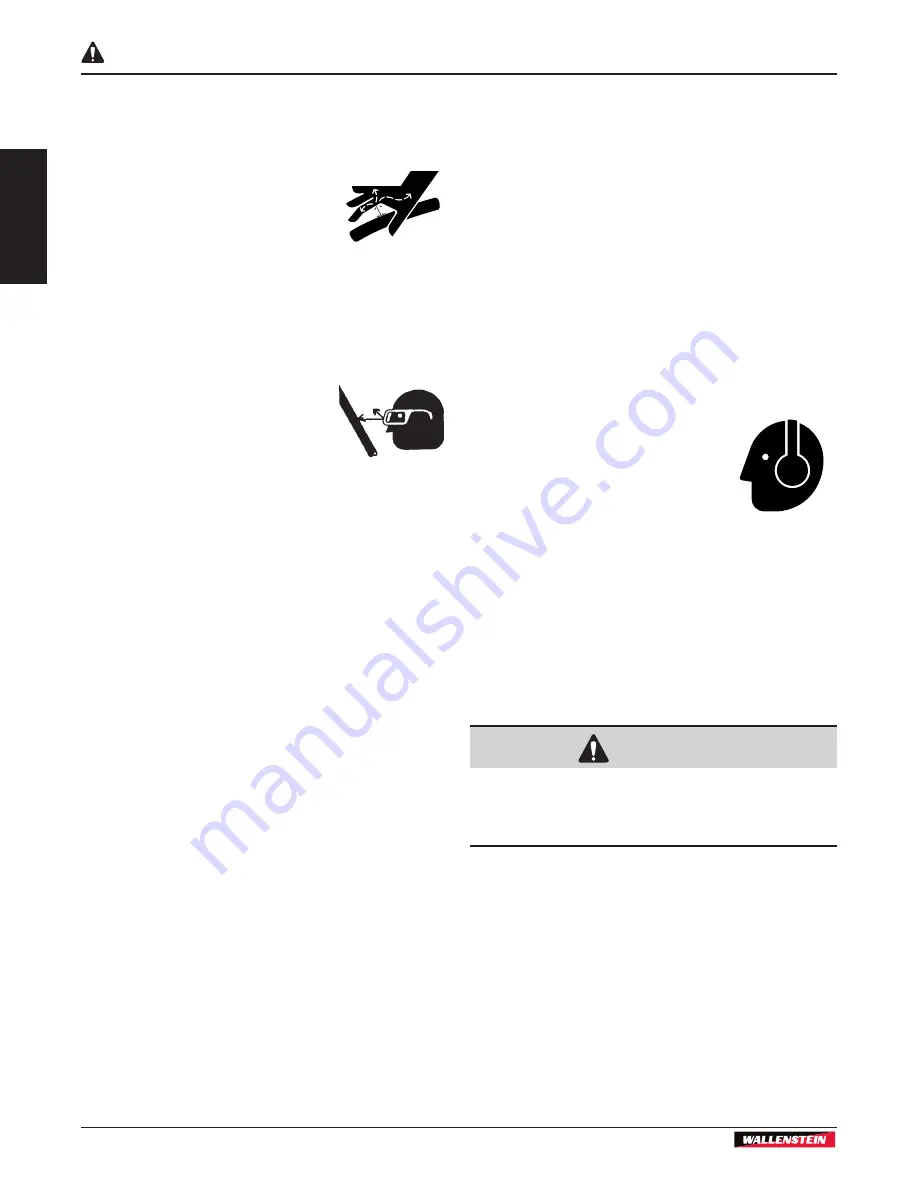
2.8 Hydraulic System Safety
1.
Make sure that all the components in the hydraulic
system are kept in good condition and are clean.
2.
Before applying pressure to the
system, make sure all components
are tight, and that lines, hoses and
couplings are not damaged.
3.
Do not attempt any makeshift repairs to the
hydraulic lines, fittings or hoses by using tapes,
clamps or cements. The hydraulic system operates
under extremely high pressure. Such repairs will
fail suddenly and create a hazardous and unsafe
condition.
4.
Wear proper hand and eye
protection when searching for a
high pressure hydraulic leak. Use
a piece of wood or cardboard as
a backstop instead of hands to
isolate and identify a leak.
5.
If injured by a concentrated high-pressure
stream of hydraulic fluid, seek medical attention
immediately. Serious infection or toxic reaction
can develop from hydraulic fluid piercing the skin
surface.
6.
Relieve pressure on hydraulic system before
maintaining or working on system.
2.9 Preparation
1.
Never use the machine until the operators have
been adequately trained in the safe operation
of the machine and have read and completely
understand:
-
safety, operation and feature sections of this
manual
- each of the safety messages found on the
safety signs on the machine.
- engine operator's manual
2.
PPE is recommended during assembly, installation,
operation, adjustment, maintaining, repairing,
removal, cleaning, or moving the trailer. Do not
allow long hair, loose fitting clothing or jewelry
around equipment.
3. Prolonged exposure to loud
noise may cause permanent
hearing loss!
Power equipment
with or without equipment
attached can often be noisy
enough to cause permanent,
partial hearing loss. We
recommend that you wear hearing
protection on a full-time basis
if the noise in the Operator's
position exceeds 80 dB. Noise
over 85 dB on a long-term basis
can cause severe hearing loss.
Noise over 90 dB adjacent to
the Operator over a long-term
basis may cause permanent, total
hearing loss.
WARNING!
Hearing loss from loud noise (from engines,
chainsaws, radios, and other such sources close
to the ear) is cumulative over a lifetime, without
hope of natural recovery.
4.
When there are two or more operators, review and
understand a system of hand signals.
5.
Keep bystanders away at a safe distance at least
20 ft (6 m) from stacking zone. Mark the zone with
safety cones.
6.
Determine where chips will be piled and ensure
it does not interfere with safe operation of the
machine
Safety
WP240-WP270
3-Point Hitch Firewood Processor
Safety
12
Содержание WP240
Страница 1: ...OPERATOR S MANUAL 3 PointHitchFirewoodProcessor WP240 WP270 Part Number Z97115_OM W Rev Sep 2019...
Страница 19: ...WP240 WP270 3 Point Hitch Firewood Processor Safety Safety 19...
Страница 57: ......
Страница 58: ......
Страница 59: ......
Страница 60: ...www wallensteinequipment com...