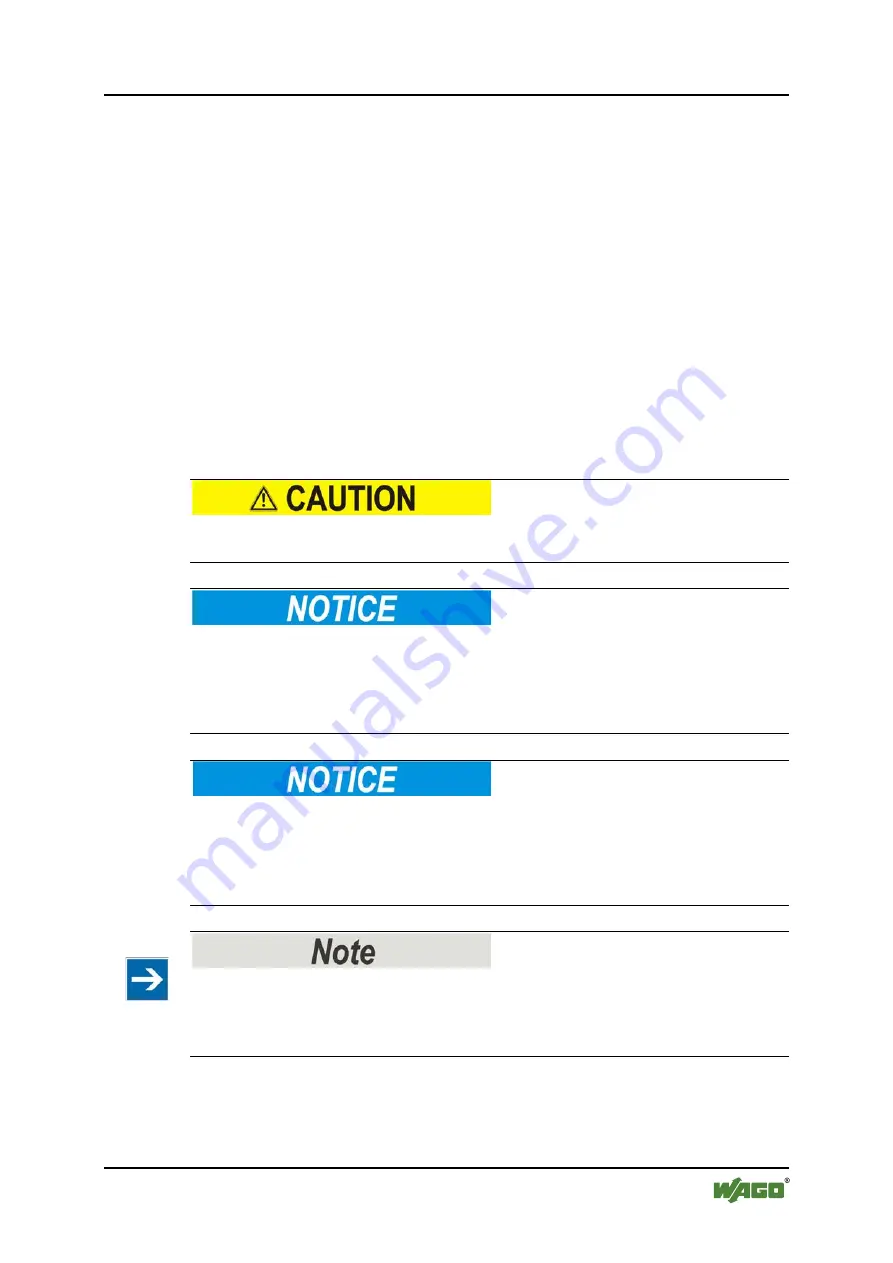
WAGO-I/O-SYSTEM 750
Mounting
25
750-1418 8DI 24V DC 0.2ms, low-side switching, 2-conductor
Manual
Version 1.1.0
4
Mounting
4.1
Mounting Sequence
All system components can be snapped directly on a carrier rail in accordance
with the European standard EN 50022 (DIN 35).
The reliable positioning and connection is made using a tongue and groove
system. Due to the automatic locking, the individual components are securely
seated on the rail after installation.
Starting with the coupler/controller, the I/O modules are mounted adjacent to each
other according to the project design. Errors in the design of the node in terms of
the potential groups (connection via the power contacts) are recognized, as the I/O
modules with power contacts (male contacts) cannot be linked to I/O modules
with fewer power contacts.
Risk of injury due to sharp-edged male contacts!
The male contacts are sharp-edged. Handle the module carefully to prevent injury.
Connect the I/O modules in the required order!
Never plug I/O modules from the direction of the end terminal. A ground wire
power contact, which is inserted into a terminal without contacts, e.g. a 4-channel
digital input module, has a decreased air and creepage distance to the neighboring
contact in the example DI4.
Assemble the I/O modules in rows only if the grooves are open!
Please take into consideration that some I/O modules have no or only a few power
jumper contacts. The design of some modules does not allow them to be
physically assembled in rows, as the grooves for the male contacts are closed at
the top.
Don't forget the end module!
Always plug an end module 750-600 onto the end of the fieldbus node! You must
always use an end module at all fieldbus nodes with the WAGO I/O System 750
fieldbus couplers/controllers to guarantee proper data transfer.