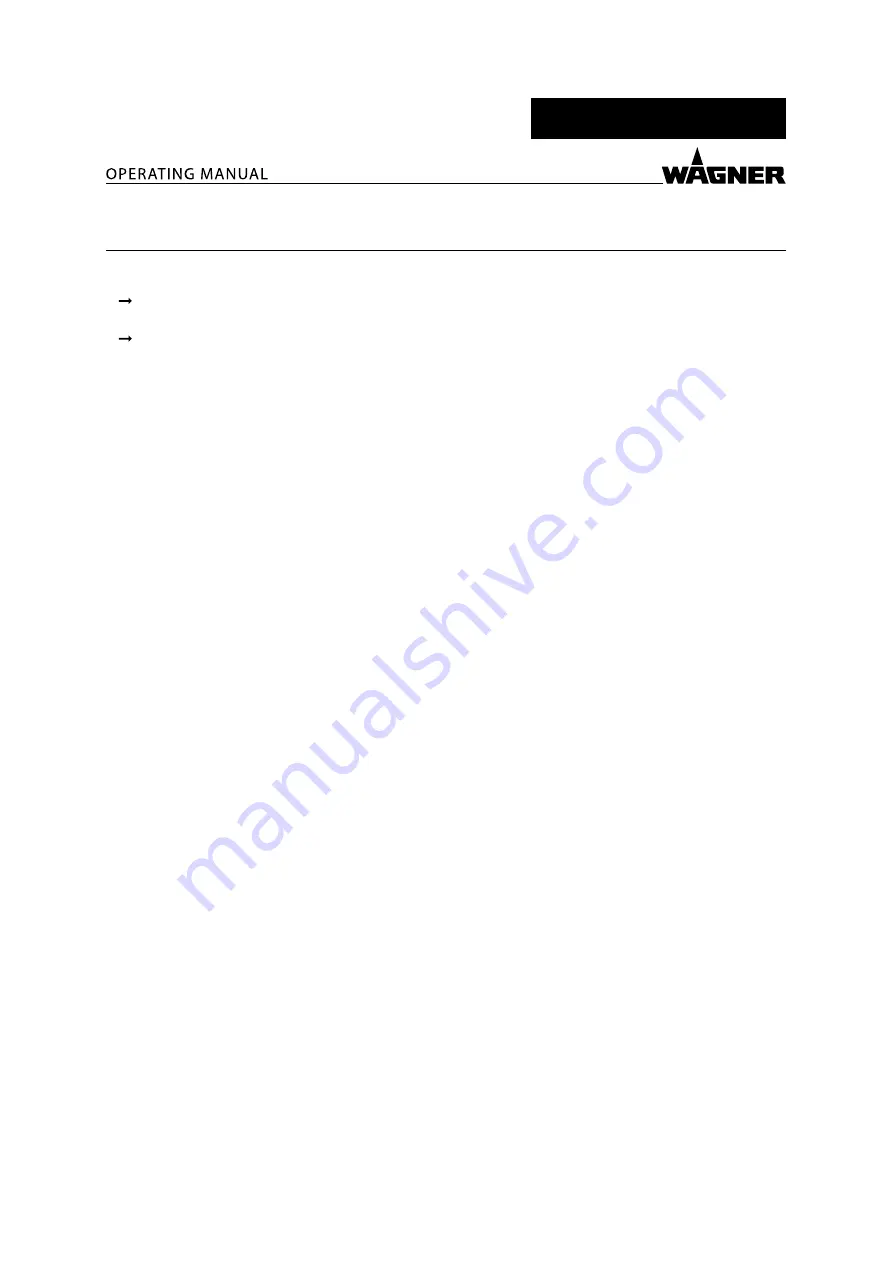
19
VERSION 02/2019
ORDER NUMBER DOC 2397374
TOPFINISH GM 1030P
6
ASSEMBLY AND COMMISSIONING
6.1
TRAINING OF ASSEMBLY/COMMISSIONING PERSONNEL
The assembly and commissioning personnel must have the technical skills to safely
commission the device.
When assembling, commissioning and carrying out all work, read and follow the
operating manuals and safety regulations for the additionally required system
components.
A skilled person must check to ensure that the device is in a reliable state after it is
assembled and commissioned.
6.2
STORAGE CONDITIONS
Until the point of assembly, the device must be stored in a dry location, free from vibrations
and with a minimum of dust. The device must be stored in closed rooms.
The air temperature at the storage location must be between -20 °C and 60 °C (-4 °F and
140 °F)
.
The relative air humidity at the storage location must be between 10 and 95% (without
condensation).
Содержание TOPFINISH GM 1030P
Страница 1: ...B_06965 TOPFINISH GM 1030P Airspray manual gun for flat and round jet nozzles Version 02 2019...
Страница 2: ......
Страница 26: ......
Страница 51: ......