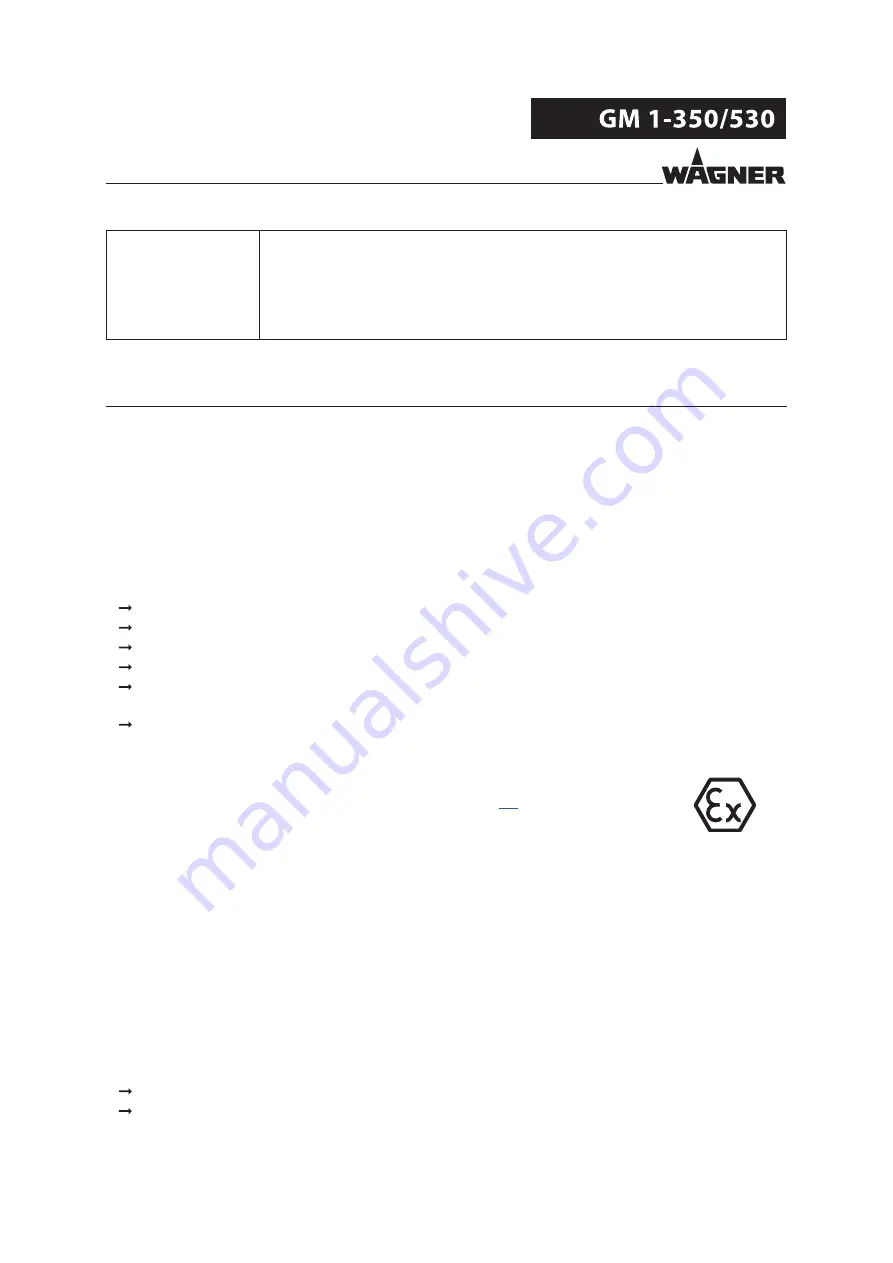
5
OPERATING MANUAL
VERSION 07/2017
ORDER NUMBER DOC 2349369
Skilled person in
accordance with TRBS
1203
(2010/Revision 2012)
A person, who, based on his/her technical training, experience and recent vocational
experience, has sufficient technical knowledge in the areas of explosion protection,
protection from pressure hazards and electric hazards (if applicable) and is familiar
with the relevant and generally accepted rules of technology so that he/she can
inspect and assess the status of devices and coating systems based on workplace
safety.
2
CORRECT USE
2.1
DEVICE TYPE
Airless manual gun for manually coating work pieces.
2.2
TYPE OF USE
The spray gun is intended for atomizing liquid coating products under pressure (airless
process).
WAGNER explicitly prohibits any other use!
The device may only be operated under the following conditions:
Use the device only to work with the products recommended by WAGNER.
Only operate the device as a whole.
Do not deactivate safety fixtures.
Use only WAGNER original spare parts and accessories.
The operating personnel must be trained on the basis of this operating manual.
Follow the instructions in the operating manual.
2.3
FOR USE IN POTENTIALLY EXPLOSIVE AREAS
The device is suitable for use in potentially explosive areas as defined in Directive
2014/34/EU (ATEX), (see Explosion protection marking Chapter
2.4
PROCESSIBLE WORKING MATERIALS
Top-coat lacquers, primer paints, corrosion protection, textured lacquers, lyes, staining
solvents, clear lacquers, separating agents, etc. with a solvent or water base. If you want
to spray working materials other than the aforementioned, please contact a WAGNER
representative.
Note:
Contact your local WAGNER dealer and the lacquer manufacturer if you encounter
application problems.
2.5
MISUSE
Misuse can lead to physical injury and/or property damage!
Special attention must be paid that:
No dry coating products, e.g. powder are processed;
Do not process food, medicine or cosmetics.