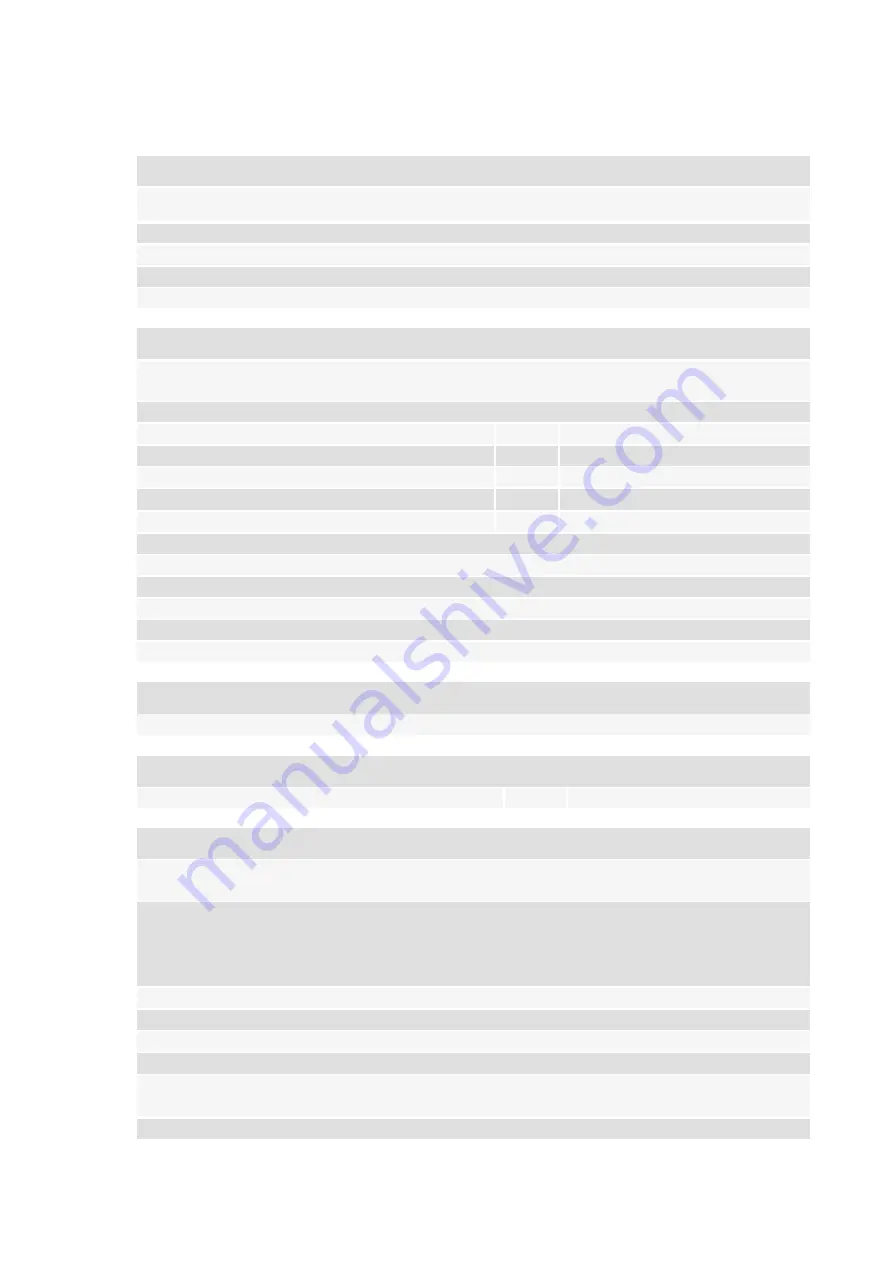
Page
5
of
61
Item – Rev(s):
8009641121– 101
TECHNICAL DATA
ENGINE
Brand and model
Kubota
V1505T
Calibration Power at 2800 rpm
HP/Kw
41/30
Cylinders
Nº
4
Displacement
cm
3
1498
Cooling
water
HYDRAULIC SYSTEM:
Hydrostatic drive with double axial piston pump and variable cylinders connected to two two-
speed geared motors, one for each track roller.
Negative braking system on the geared motors
Main variable-cylinder axial piston pump
Lt/min 57.4 x 2
Auxiliary gear pump
Lt/min 39 x 1
Total capacity
Lt/min 153.8
Useful capacity for power take off (PTO)
Lt/min 39 a 180 bar
Max. operating pressure
bar
180
Hydraulic servo-controls with joy sticks for traversing and manoeuvre of arms and bucket.
Floating electrovalve to adjust the bucket to the ground
Safety electrovalve to block arm descent
Electro-valve for 2
nd
speed control
Heat exchanger for the cooling of the hydraulic oil.
Hydrostatic steering
FRAME:
Chassis in box-type sheet steel and shaped
RUBBER TRACKS:
Width
mm
250
PERFORMANCE:
Weight when fully eupped (including
operator)
Kg
2220
Bucket capacity (SAE capacity m³ 0.245)
- 35% T.L. (*) ISO 14397/1-2
Kg
400
- 50% T.L. (*) ISO 14397/1-2
Kg
520
(*)T.L.=Tipping Load = Maxloadpermittedby the machine withmaximum workingradiusat tippinglimit.
Tear strength at tooth
daN
930
Lifting force at floor level
daN
1030
Transfer speed I/II
Km/h
4.5÷10
Possible gradient
%
more than100
Specific ground pressure:
- when empty Kg/cm
2
0.33
- when loaded
Kg/cm
2
0.40
Autonomy
About hours
8
Содержание ST11
Страница 1: ...OPERATION MAINTENANCE MANUAL Compact Track Loader ST11 Item 8009641121 Revision Date 101 March 2022...
Страница 16: ...CONTROL AND AUXILIARY INSTRUMENTS CONTROL PANEL Fig 1 17 Page 16 of 61 Item Rev s 8009641121 101...
Страница 60: ...MAINTENANCE NOTES HOURS WORKED DATE WORK DONE PARTS CONCERNED Page 60 of 61 Item Rev s 8009641121 101...
Страница 61: ...MAINTENANCE NOTES HOURS WORKED DATE WORK DONE PARTS CONCERNED Page 61 of 61 Item Rev s 8009641121 101...