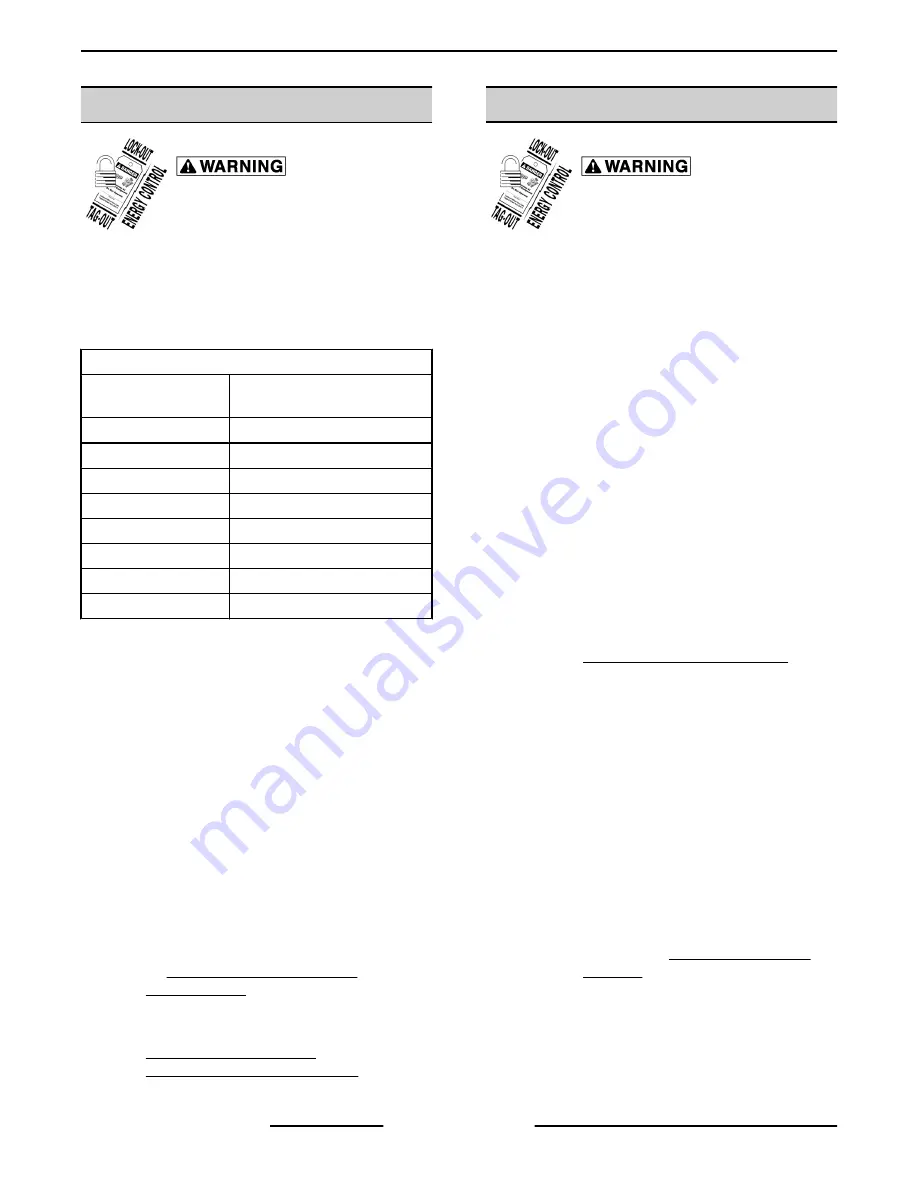
TEMPERATURE PROBE TEST
Certain procedures in
this section require electrical test or
measurements while power is applied
to the machine. Exercise extreme
caution at all times and follow Arc Flash
procedures. If test points are not easily
accessible, disconnect power and
follow Lockout/Tagout procedures,
attach test equipment and reapply
power to test.
Temperature to Resistance Chart
Degrees
(Fahrenheit)
Resistance
77°
90k - 100k
200°
8354
250°
3794
300°
1903
250°
1032
400°
609
450°
374
500°
241
1.
Place a shielded thermocouple in center of oven
cavity.
2.
Turn oven on and set to 350° Fahrenheit.
3.
Remove temperature control knob.
4.
Hold down "-" (minus) button for 3 seconds to
enter diagnostic mode.
NOTE:
Display should now show oven temperature
reported by probe.
5.
Allow temperature to stabilize (typically 3 cycles).
•
If thermocouple temperature is within 5°
Fahrenheit of display temperature, probe is
functioning properly.
•
If temperature difference between
thermocouple and display is greater than 5
degrees but less than 20° Fahrenheit, refer
to: TEMPERATURE CONTROL
CALIBRATION to calibrate.
•
If temperature difference is greater than 20°
Fahrenheit turn off oven, replace
TEMPERATURE PROBE, then repeat
TEMPERATURE PROBE TEST.
HEATING ELEMENT TEST
Certain procedures in
this section require electrical test or
measurements while power is applied
to the machine. Exercise extreme
caution at all times and follow Arc Flash
procedures. If test points are not easily
accessible, disconnect power and
follow Lockout/Tagout procedures,
attach test equipment and reapply
power to test.
1.
Turn the power switch ON and set the oven
temperature control to the highest setting.
2.
Measure the voltage at the heating element
terminals and verify it against the data plate
voltage.
A.
If voltage is incorrect, find the source of the
problem.
B.
If voltage is correct, check current draw
(amps) through the heating element lead
wires.
NOTE:
This method is preferred over a resistance
check when a clamp on type amp meter is available.
1)
If current draw is correct then heating
element is functioning properly. See
HEATING ELEMENT VALUES table.
2)
If current draw is not correct, turn the
power switch OFF and disconnect the
electrical supply to the oven.
a.
Replace heating element, then
proceed to step 3.
C.
If unable to check current draw, a resistance
check may indicate a malfunctioning
element.
1)
Turn the power switch OFF and
disconnect the electrical supply to the
oven.
2)
Remove the lead wires from the
heating element and check resistance
(ohms). See HEATING ELEMENT
VALUES table.
3.
Check for proper operation.
VC5ED FULL SIZE ELECTRIC CONVECTION OVEN - SERVICE PROCEDURES AND ADJUSTMENTS
F45652 (0217)
Page 16 of 31