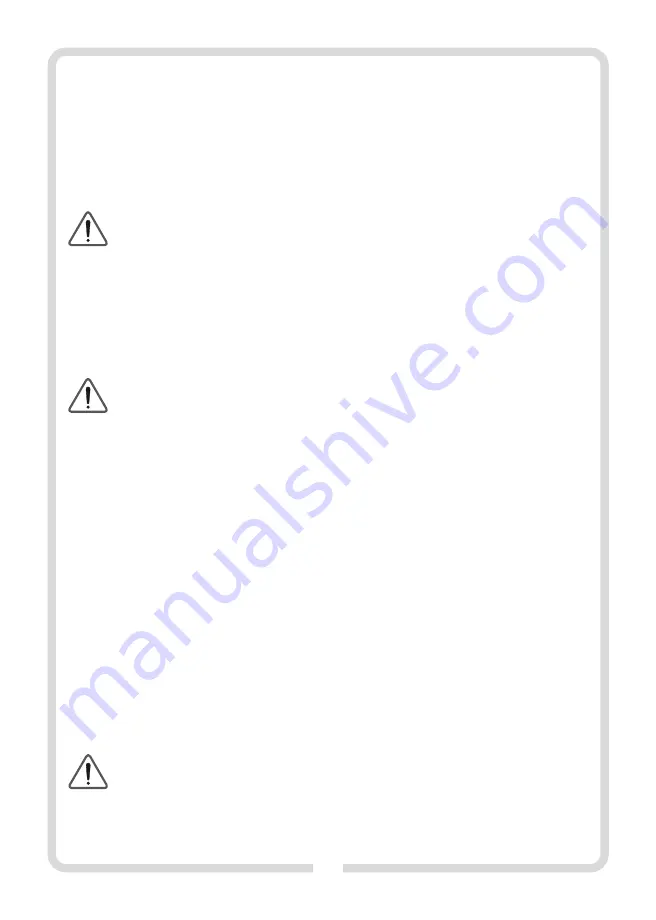
8
ź
Releasing the On/Off trigger (
4
) switches the machine off.
n
Surface machining
Set the desired cutting depth and place the front sole of the tool shoe
(
29
) onto the machined surface.
NOTE:
Hazard of powerful reaction kicks! Start planing only after the
cutting shaft reaches the maximum rotation speed.
Switch the tool on and hold it with two hands. Move the plane
r
smoothly
and uniformly down the entire surface to be machined. Both the front
and rear soles of the shoe plate must firmly rest on the machined part.
CAUTION:
The power cord should be always within a safe
distance from rotating parts of the electric tool. Remember to
keep always the power cord behind the electric tool.
To achieve high quality of finishing it is recommended to keep pushing
the plane
r
really gently, trying to equalize pressure onto the plane
r
shoe.
For machining of hard materials, e.g. hard timber grades or for planing
with the entire width of the tool it is recommended to set only low
cutting depth and reduce the tool advancing speed.
Too fast advancing is detrimental to quality of machined surfaces, may
lead to the machine overloading or to quick clogging of the chip ejector.
Final finishing of surfaces should be carried out with only small cutting
depth and the surface is to be machined with multiple passes.
NOTE:
When the planing cutting roller (
28
) gets stalled,
disconnect the tool immediately from the power source,
remove the obstacle and check condition of the cutters. Do
never use tools with damaged components.
n
Bevelling of edges
(see Fig.
F
, p.. 4)
º
Fast and easy bevelling of edges at the angle of 45 is possible owing to a
dedicated V-shaped groove (
20
) running down the front sole of the
machine shoe. Place the groove onto the machined edge and drive the
tool forward. Pay attention to smooth and uniform driving and keeping
the angle constant.
NOTE:
Only sharp cutting blades guarantee high quality of machining and
present the tool from being damaged.
n
Planing with use of a parallel guide bar
Cutting out of recessed planes is easier with use of a guide bar (
12
) or
parallel planning. The guide bar should be installed on the electric tool
with use of the angle bracket (
1
4
) according to Fig.
A
in page
2
. When
necessary the grooving depth limiter (
1
7
) can be installed as well.
To adjust the necessary width of the grooved plane
r
it is necessary to
release the nut (
1
3
), move the guiding bar perpendicularly against the
angle bracket to the desired width and then retighten the nut (
1
3
)
.
Release the bolt (
1
8
) and adjust the desired depth of grooving with use
of the depth limiter (
11
) (see Fig.
E
p.. 4).
Use smaller depth values and repeat the grooving operation several
times until the desired offset of surfaces is achieved. The plane
r
should be
driven with a moderate lateral pushing force (see Fig.
C
p.. 3).
REPLACEMENT OF CUTTING BLADES:
NOTE!
Prior to commence any maintenance or repair jobs
make sure that the device is disconnected from the electric
power network.
The plane
r
is provided with two rotating cutters that are made of hard
alloy. The cutters have two blades so that they can be used for two-sided
machining. Owing to the guiding groove of cutters they can be reliably
set at the same height.
NOTE:
Never attempt to sharpen cutters made of hard alloys! Worn, blunt
or damaged cutters must be replaced with new ones. Use only
Centrolock
HM
cutting blades with dimensions of 6 x 1 x 82 mm.
CAUTION:
To replace the cutting blade put on protective gloves and be
careful to avoid injures. Do never touch the cutter blades. There is a risk of
injuries with sharp cutting blades.
n
Disassembly of a cutter
(see Fig.
B
, p..3)
To replace or swap the cutter (
2
2
) proceed in the following way:
- rotate the cutting shaft (
28
) to provide access to fixing bolts (
24
) of
the cutter holder;
- clean the cutter holder (
27
);
- loose three fixing bolts of the cutter holder (
24
) on the cutting shaft
(
28
) with useM8 flat wrench (
1
5
);
- use a wooden follower to push the cutter away from the shaft.
n
Installation of a cutter
Prior to installation of a new cutter clean carefully all the mating parts.
Slide a new cutter in between the holder (
27
) and the backup plate (
25
).
NOTE:
The backup plate is provided with recesses meant to align the cutter
with regard to its holder. Check carefully whether both the cutter and the
backup plate are precisely in contact with the cutter holder and the blade
line is perfectly parallel to the shaft surface. When the cutter is installed
correctly the blade edge should perfectly match the rear sole of the base
shoe (
2
3
)
(see Fig.
G
, p..4
)
.
When necessary, adjust the setting with use of
a hexagonal socket wrench (
16
) to rotate the bolts until the desired
elevation of the cutting blade (
2
1
) is reached.
Make sure that position of the cutter is correct with respect to the both
ends of the cutting shaft and firmly tighten the three fixing bolts
(
24
)
.
NOTE:
Always replace a pair of cutters to have the cutting set with identical
parameters. It guarantees perfect balancing of the rotating shaft.
Prior to starting the machine again check whether the bolts (
24
) are
correctly tightened. Rotate the cutting shaft (
28
) with hand and check
for possible rubbing between the bolts and the cutter.
n
Replacement of a transmission belt
To replace the transmission belt (
31
) proceed in following way:
- use a cross-tip screwdriver to unscrew
three
fixing bolts of the
transmission belt cover (
30
) and remove the cover (
8
) (see Fig.
H
,
p.4
);
- disassemble the damaged transmission belt (
31
) (see Fig.
I
,
p.4
);
- clean the belt pulleys with use of a soft brush;
- place the new V-belt on the groove of the smaller pulley and then
rotate the big one to drive the V-belt into its groove;
- reinstall the transmission belt cover and fix it with bolts.
STORAGE AND MAINTENANCE:
Generally, this power tool does not require any special maintenance.
Store the machine in a place away from children, keep it clean and
protect from humidity and dust. Storage conditions should exclude any
mechanical damage and weathering.
After each use it is recommended to clean the tool from chips and
shavings. Ventilation openings should be blown with compressed air. It
prevents from premature wear of bearing and removes all dust that
disables access of cooling air to the machine motor.
Wipe the device body with a wet cloth with small amount of soap. Do
never use any aggressive cleaning agents or solvents as they may
Содержание VMG601
Страница 2: ...2 A 1 11 12 10 8 16 15 19 3 5 14 6 7 2 1 4 13 17 18 9...
Страница 3: ...3 1 C B 23 22 24 27 28 29 15 20 21 25 26...
Страница 16: ...RCD 16 VMG601...
Страница 17: ...17 a a...
Страница 18: ...a n 1 1 1 1 1 1 1 1 1 M8 1 1 1 1 n 2 4 A 1 18...
Страница 21: ...24 28 n 31 30 8 H 4 c 31 I 4 34 03 228 21 PROFIX...
Страница 47: ...47...
Страница 48: ...www profix com pl...