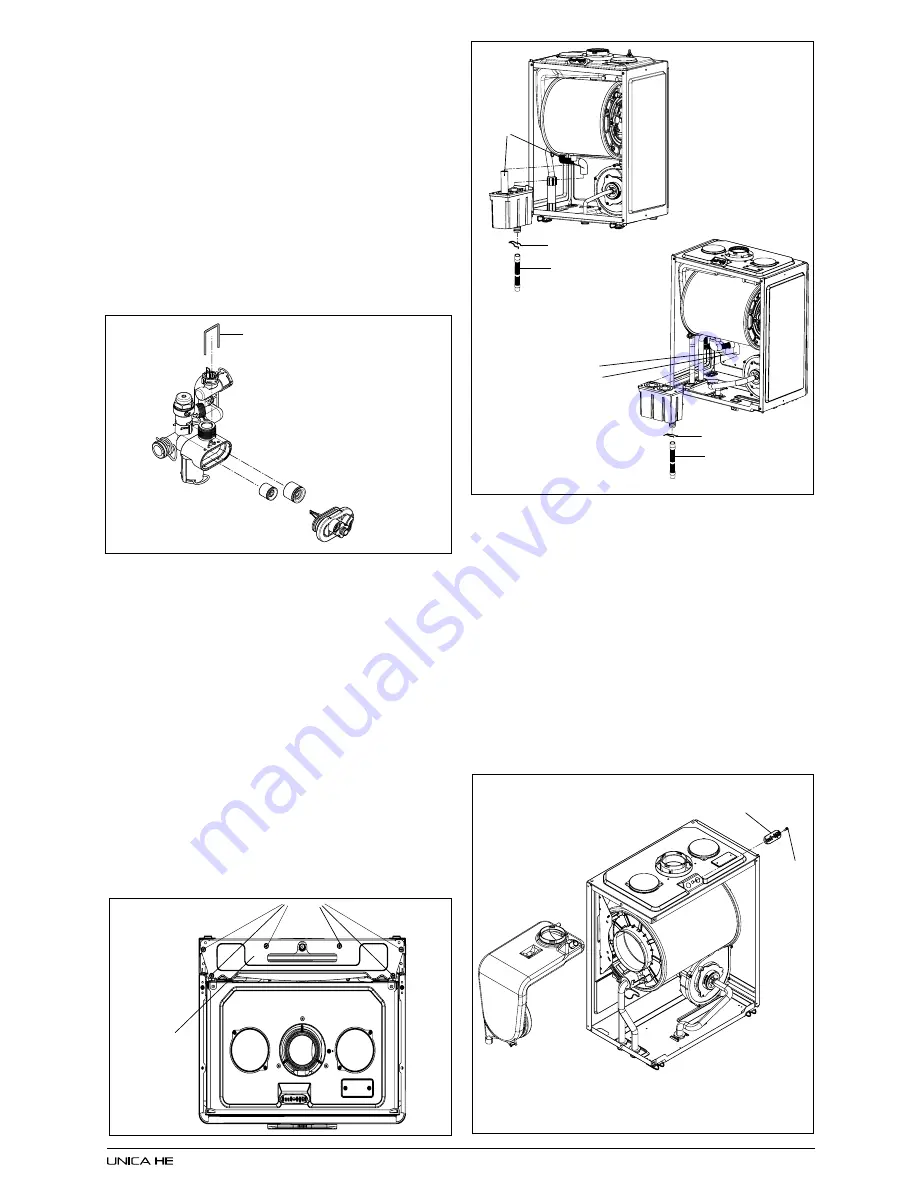
21
6.17
AUTOMATIC BY-PASS & DHW NON-RETURN
VALVE (fig. 32)
Carry out component removal procedure as de-
scribed in 6.4.
Remove the locking pin
(A)
that secures the cover
(B)
to the hydraulic manifold. Using a hooked piece
of wire, carefully withdraw the by-pass cartridge
(C)
and/or DHW non-return cartridge
(D)
. Ensure all seals
are in good condition, taking care to ensure they are
replaced correctly. Replace in the reverse order ensur-
ing the cartridge is facing the correct way.
6.18
EXPANSION VESSEL (fig. 1)
Should the removal and replacement of the
expansion vessel be deemed impractical, an
external expansion vessel may be fitted to the
return pipe as close to the appliance as possible.
6.18.1 EXPANSION VESSEL REMOVAL (with
sufficient clearance above, fig. 33)
Carry out component removal procedure as
described in 6.4. Disconnect the flue from the
appliance. Disconnect the expansion vessel from
the flexible expansion pipe. Disconnect the
flexible expansion pipe from the vessel. Unscrew
the nut that secures the vessel to the lower frame.
Locate and remove the 6 screws
(A)
that secure
the vessel top holding plate
(B)
, remove the plate.
The expansion vessel can now be removed.
Replace in the reverse order. Ensure all seals are
in good condition, taking care to ensure they are
replaced correctly.
fig. 34
6.19
CONDENSE TRAP REMOVAL (fig. 34)
Carry out component removal procedure as
described in 6.4. Disconnect the 2 upper rubbers
condense pipe
(A)
. Remove the pin
(B)
that secures
the trap to the air box plate. Disconnect the lower
rubber condense pipe
(C)
from the condense trap.
Carefully remove the condense trap. Replace in
the reverse order.
6.20
FLUE COLLECTOR REMOVAL (fig. 35)
Carry out component removal procedure as
described in 6.4. Unclip and remove the air
chamber front and left side covers. Locate and
remove the screw
(A)
that secures the flue gas
analysis test point cover
(B)
. Gently pull down
and to the left and ease the flue collector from its
location. Replace in the reverse order.
fig. 35
A
C
A
B
A
B
C
B
A
Fig. 31:
To remove the fan burner assembly
(A)
locate and remove the 3 external nuts
(B)
. Replace
in the reverse order. Ensure all seals are in good
condition, taking care to ensure they are replaced
correctly.
Fig. 32
A
D
C
B
fig. 33
B