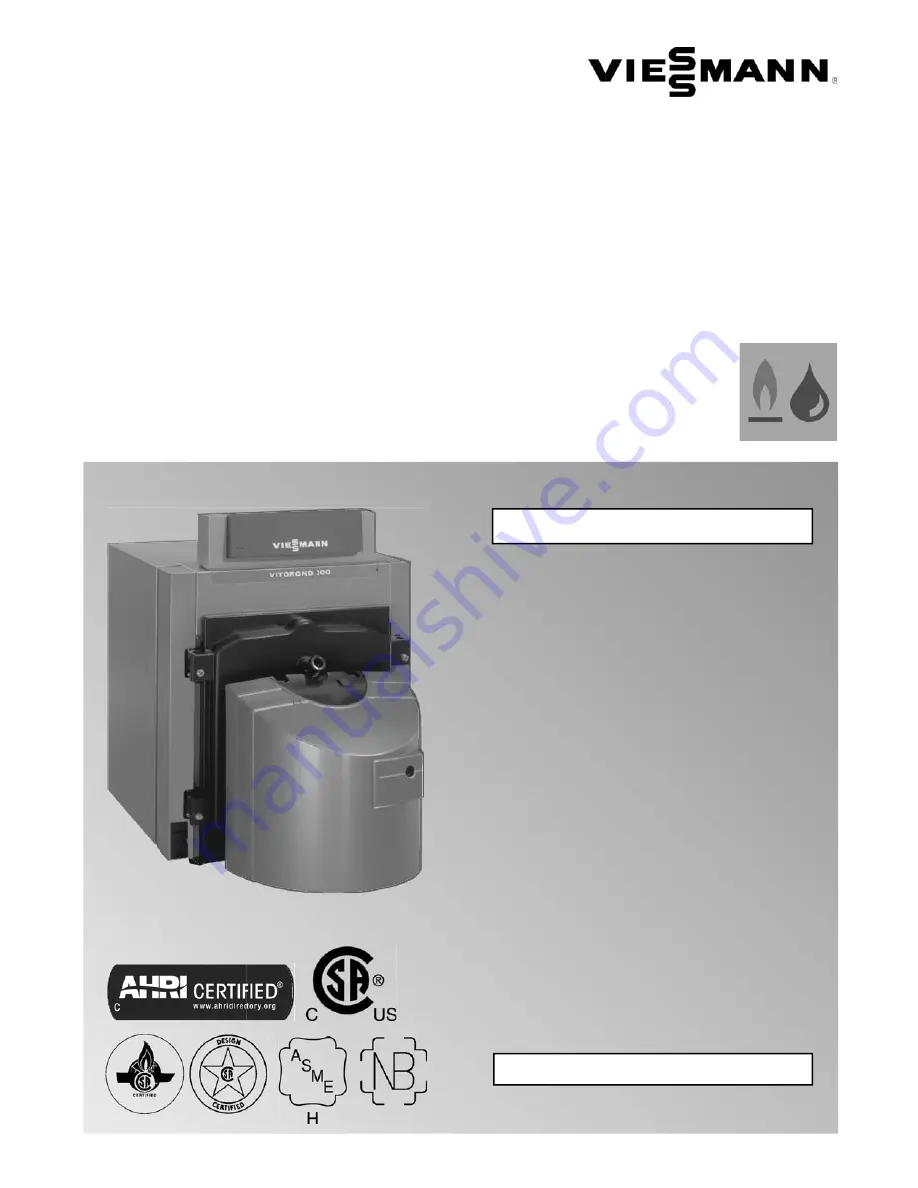
for use by heating contractor
Please file in Service Binder
Read and save these instructions for future
reference.
IMPORTANT
Product may not be exactly as shown
5354 788 - 03 03/2015
Installation Instructions
VITOROND 200
Vitorond 200
VD2A Series
Oil-/Gas-fired boiler
Heating input: 490 to 1096 MBH
144 to 321 kW
Working on the equipment
The installation, adjustment, service and
maintenance of this product must be performed
by a licensed professional heating contractor,
who is qualified and experienced in the installation,
service and maintenance of hot water heating
boilers. There are no user serviceable parts on the
boiler, burner, or control.
Ensure main power supply to equipment, the
heating system and all external controls has been
deactivated. Close main oil or gas supply valve.
Take precautions in all instances to avoid
accidental activation of power during service work.
Improper installation, service or maintenance can
cause product/property damage, severe personal
injury, and/or loss of life.
IMPORTANT
Please ensure that these instructions are read and
understood before commencing installation and
start-up. Failure to comply with these Installation
Instructions will render all warranties null and void.